真空注型
真空注型(ポリウレタン注型)は非常にポピュラーな技術であり、小ロット生産レベルの品質である硬質プラスチック、ゴム、シリコン部品を制作します。
- ISO 9001 & ISO 13485 認定書
- 7日間内に1~50個以上納品
- 24/7技術サポート
- 材料範囲広い

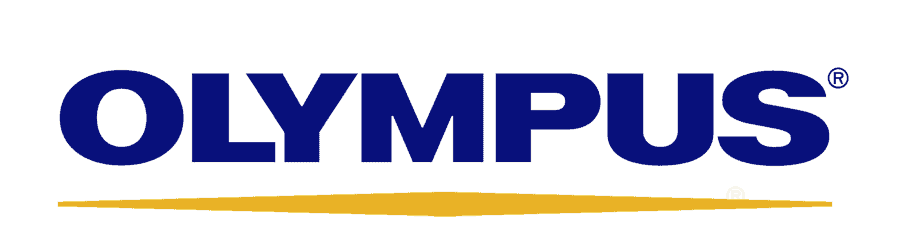
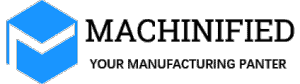

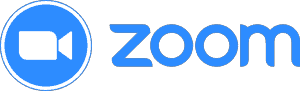
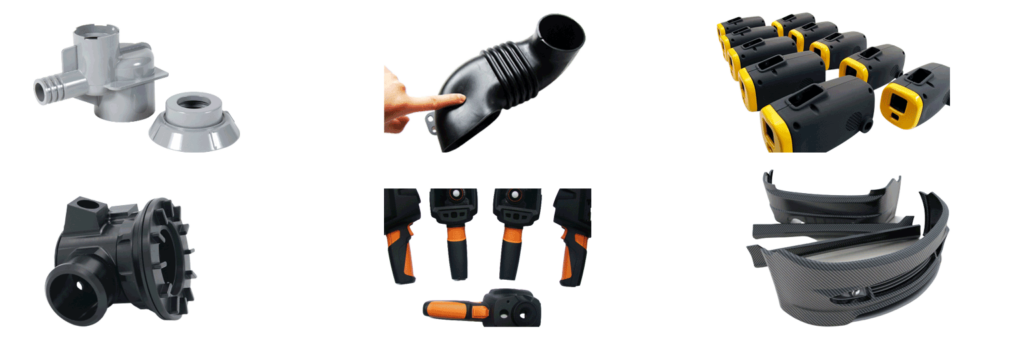
真空注型お見積りはこちらから
STEP | STP | SLDPRT | IGS | X_T | PDFファイル
- すべてのアップロードデータは安全で秘密保持されている
真空注型(ポリウレタン注型またはポリウレタン注型)
真空注型は射出成形に似ている製造プロセスであり、ポリウレタン樹脂は2つのシリコン金型のキャビティに注型されます。真空注型により、生産レベルの品質である硬質プラスチック、ゴム、シリコン部品を製造します。
注:真空注型はアメリカや欧米では、ポリウレタン注型やポリウレタン注型とも呼ばれている。本文では、この用語を両方とも利用して紹介します。
真空注型とは?
ポリウレタン注型は、キャビティの周りにシリコン金型を注型することによりキャビティを複製するプロセスである。プログラムによって、金型は2つに切断されて、メイン型を除去した後、ゲートと換気システムを追加します。メーカはポリウレタン系樹脂をキャビティに注入して、泡発生を防止するため、真空状態で硬化します。最後は元のオブジェクトの高精度コピー品になります。ポリウレタン注型プロセスは、真空状態で行われるため、表面テクスチャが滑らかで傷のと気泡なし高品質のプラスチック部品を製造することができます。
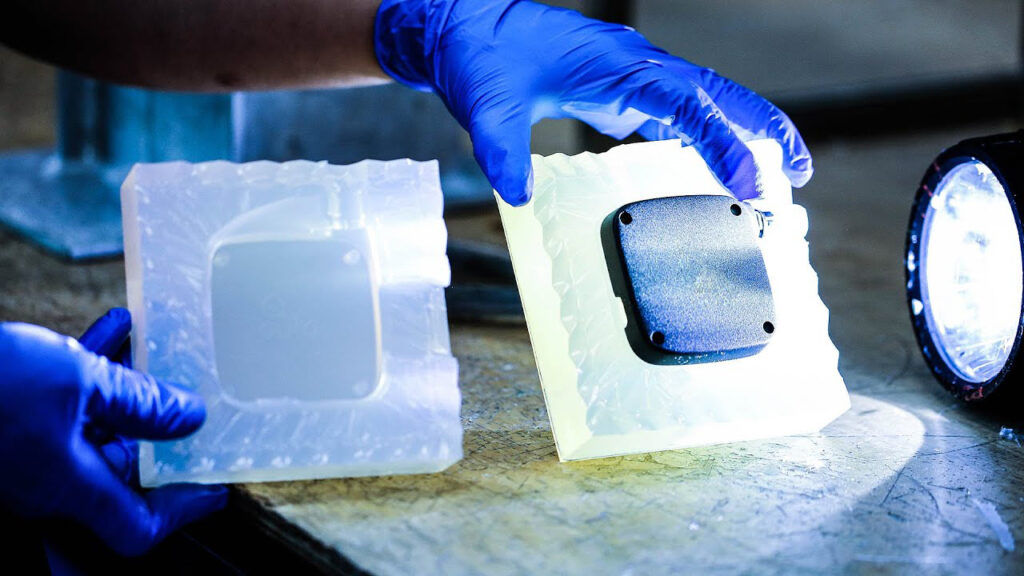
真空注型作業フロー
ポリウレタン真空注型品の生産は一般的に3つのステップに分けられる:先にマスタモデルを作って、次に金型を作り、最後に注型部品を作ります。
ステップ1.マスターを作製する
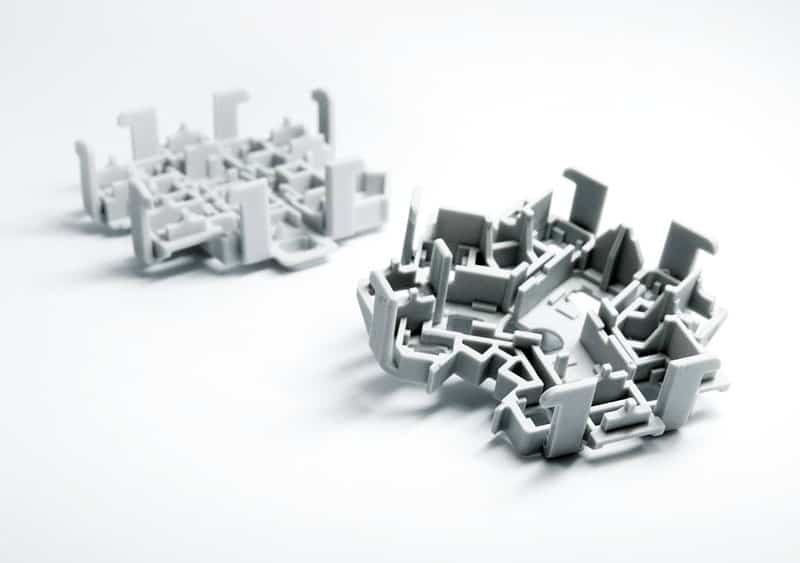
注意していただきたいのは、このモデルは40°Cの加熱に耐えられる必要があることです。
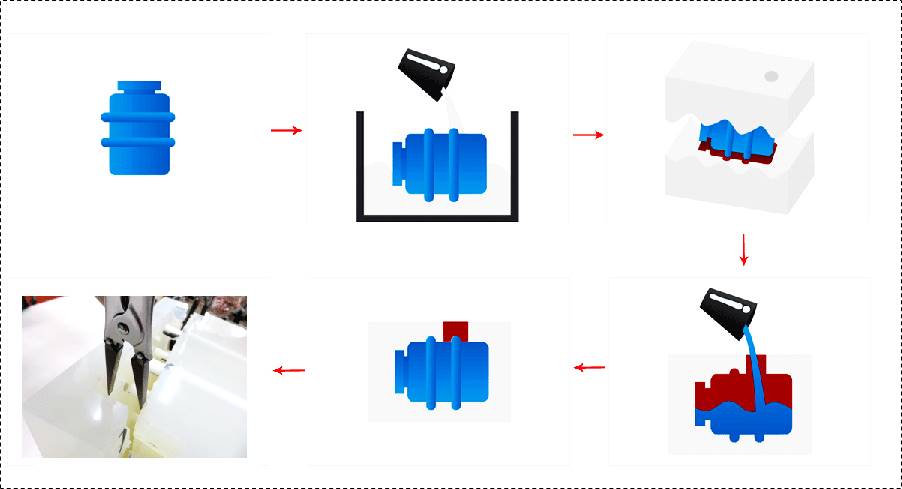
ステップ2 .シリコン金型製造
- マスタモデルの周囲の平坦な場所にテープを置いて、後で金型を切断しやすいようにして、この位置も最終的なシリカゲル金型の分裂面になります。
- 注型箱にマスタモデルを掛け、プラスチック棒を配置してゲートと換気口を設定します。
- 液体シリコンをマスタモデルの周囲に注入して、すべての空気を除去し、マスタモデルに気泡がないように真空室を形成する。次に、液体材料をオーブンに入れて、40℃で硬化させる、金型の体積によって、通常8〜16時間かかります。
- シリコーンゴムが硬化した後、金型ケースを切開し、シリコーンゴムからマスタモデルを取り出す。金型を切開して母型を取り出した後、元の形状と全く同じキャビティが残ります。
ステップ3.真空注型プロセス
- 最初にシリコン型をオーブンに入れ、60 ~ 70℃まで予熱して、型合わせ前に適切な離型剤を選んで、粘着性と表面欠陥が発生したないように正しく使用することが非常に重要であります。
- ウレタン樹脂を使用する前に40°C程度に予熱して準備して、二成分注型樹脂を正確な割合で混合した後、真空条件で50〜60秒間完全に攪拌して、脱泡して、気泡などが発生しないようにする。
- 自動制御によって、樹脂を真空チャンバ内の金型に入れて、オーブンで再度硬化する。平均硬化時間:小さい部品は1〜3H、大きい部品3〜6Hかかります。
- 硬化後、シリコン金型から注型品を取り出す。
- 上記んお真空注型プロセスを繰り返します。
真空注型公差
真空注型物の公差は、マスタモデルの精度、幾何形状、および使用する注型材料の種類に依存します。一般に、収縮率は0.15%と予想されます。
信頼できる真空注型メーカ
真空注型ではAN-Prototypeが選べれる理由
中国の先進な真空注型メーカーとして、AN-Prototypeは高品質プラスチック部品は低コストで製造する提案を提供しています。ポリウレタン注型方法により、お客様高価な初期投資を回避でき、高品質のプロトタイプと小ロット生産部品を作成用の完全なソリューションを提供しています。
低コスト
ポリウレタン注型品は、安価な金型から作られており、高価で時間かかる金型に投資する必要はなくて、高品質の原型と小ロット部品を製造する用の経済的で効率的な方法です。
短納期
真空注型の場合、7~15日内に最大50個のポリウレタン注型プラスチック部品が製造できます。それに複数の材料が選びられます。
複雑な幾何構造サポート
真空注型により、最終用途部品に高精度と量産レベルの品質が実現できます。高品質のエラストマー材料を使用することで、複雑な構造がある真空鋳造プラスチック部品を確実に生産できます。詳細な設計提案も提供可能です。
材料と表面処理の選択
AN-Prototypeは、お客様に柔らかいと柔軟性、剛性、耐衝撃性、カラーと透明性の注型樹脂素材、さまざまな表面処理オプションと素晴らしい製品を提供します。ポリウレタン注型方法は、CNCプロトタイプ作成または3 D印刷よりも優れた表面テクスチャ(木目)を提供することができます。
安定的な品質
AN-Prototypeは、ISO 9001&ISO 13485認定書が取得でき、私たちの製品とサービスが国際品質基準に適合することを保証することは誇りと思っています。最高基準の医療用プラスチック部品を納品できるように製造性分析と厳し品質管理を行っています。
専門な真空注型メーカ
AN-Prototypeは熟練の経験を持って、専門的な真空注型メーカとして、お客様に信頼性が高いカスタム真空注型製品を提供しています。AN-Prototypeに、真空注型業界で最も優れた技術とエンジニアがいて、真空注型、材料選択、表面処理などの専門知識を提供する能力があります。
真空注型用素材

ABS-系
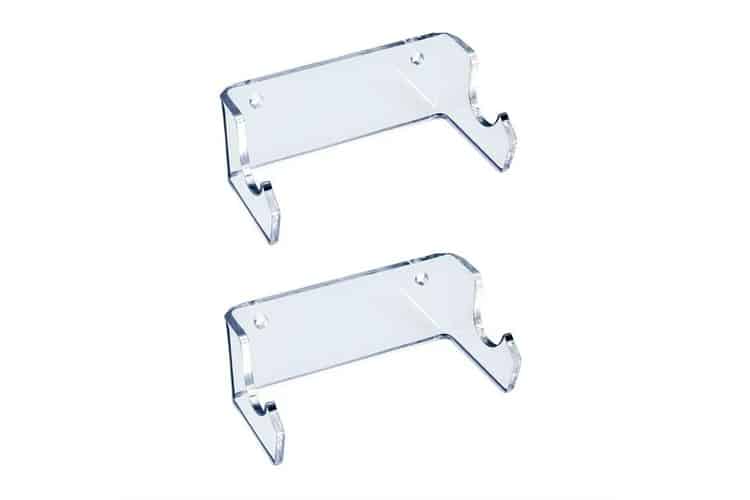
アクリル-系
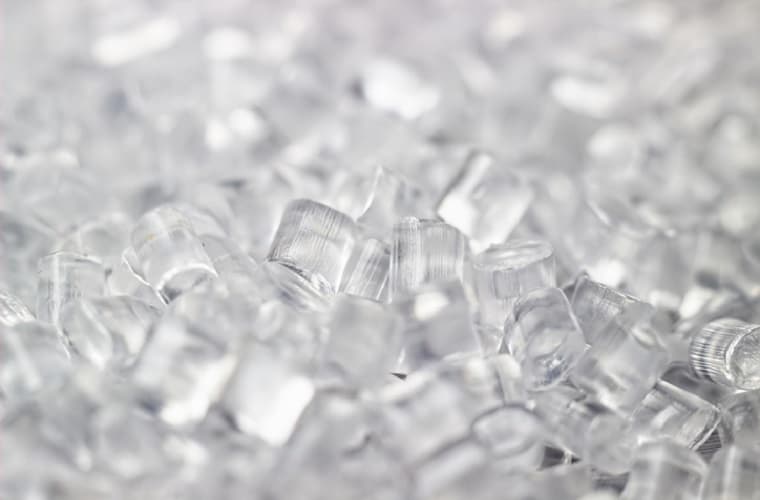
ポリプロピレン-系
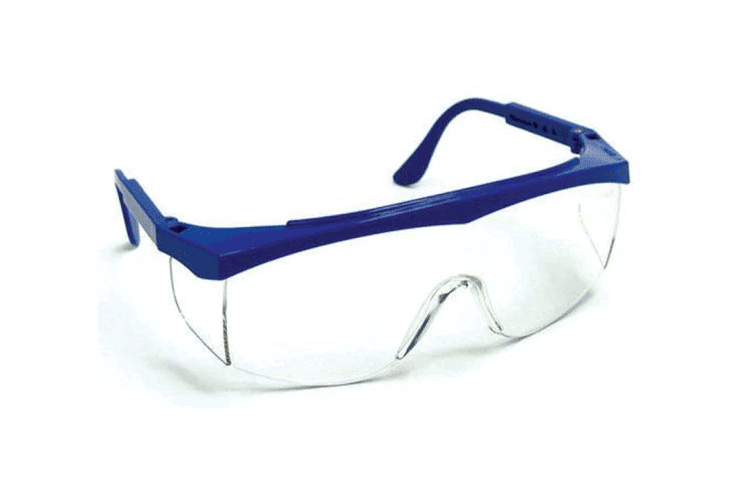
ポリカーボネート-系
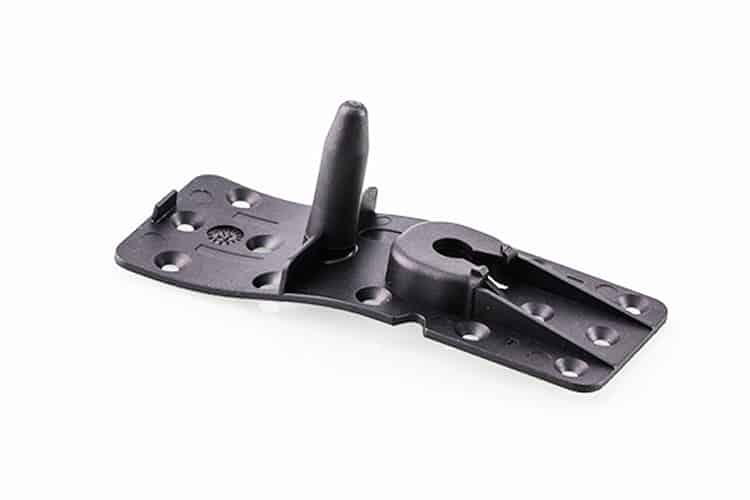
PA-系
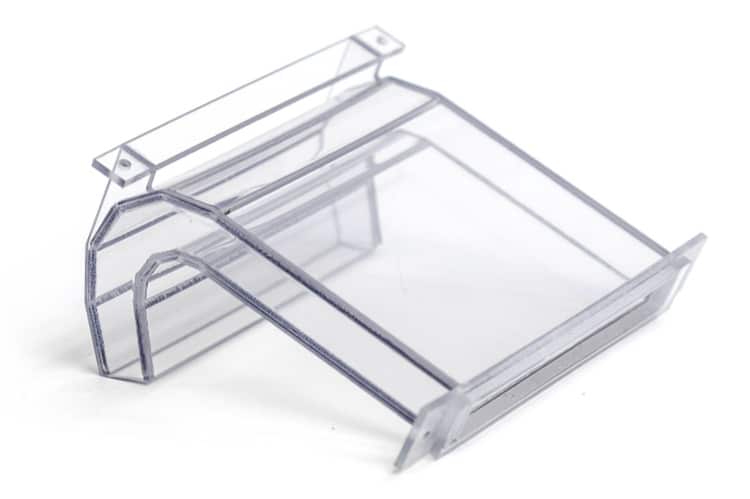
PC-系
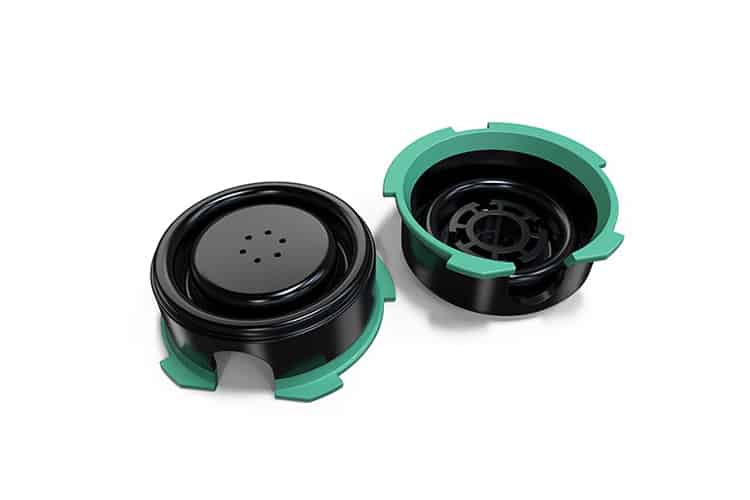
PP-系
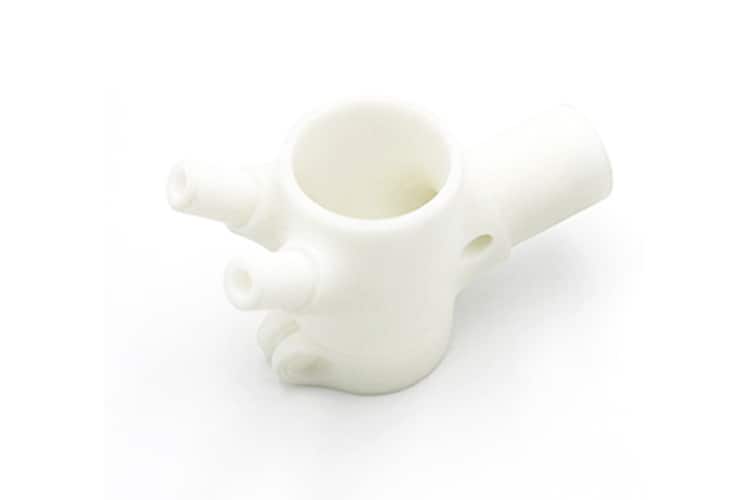
ガラス充填ナイロン-系
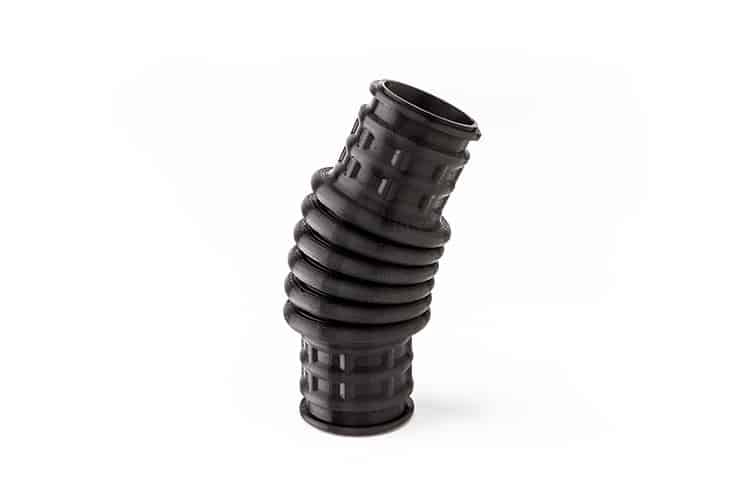
弾性体
キャスティングシリコン材料
- ショアA 10(TC-5005または同等製品)
- ショアA 20-30(TC-5130または同等製品)
- ショアA 30-40(TC-5140または同等製品)
- ショアA 40-50(TC-5150または同等製品)
- ショアA 50-60(Smooth-Sil™ 960または同等製品)
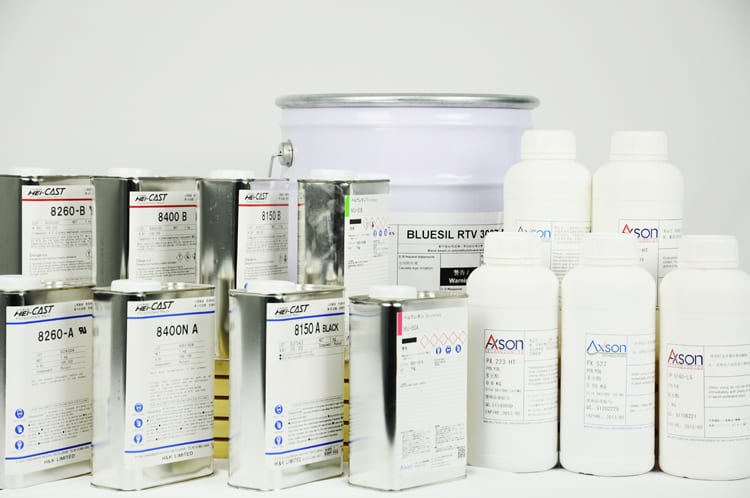
真空注型技術ガイドライン
標準精度
最大真空注型部品
一番小さい肉厚部品
シリコン金型の寿命
一般的な納品時間
表面テクスチャ(木目)とその他の選択肢
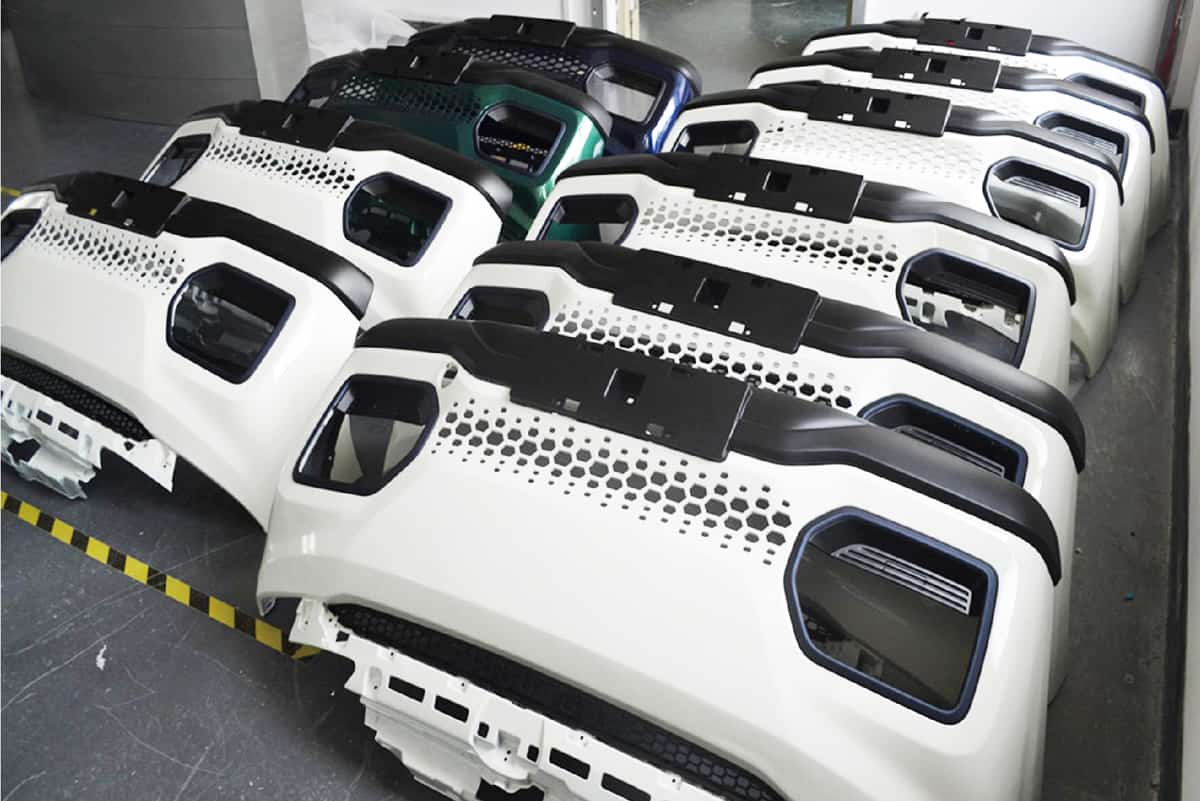
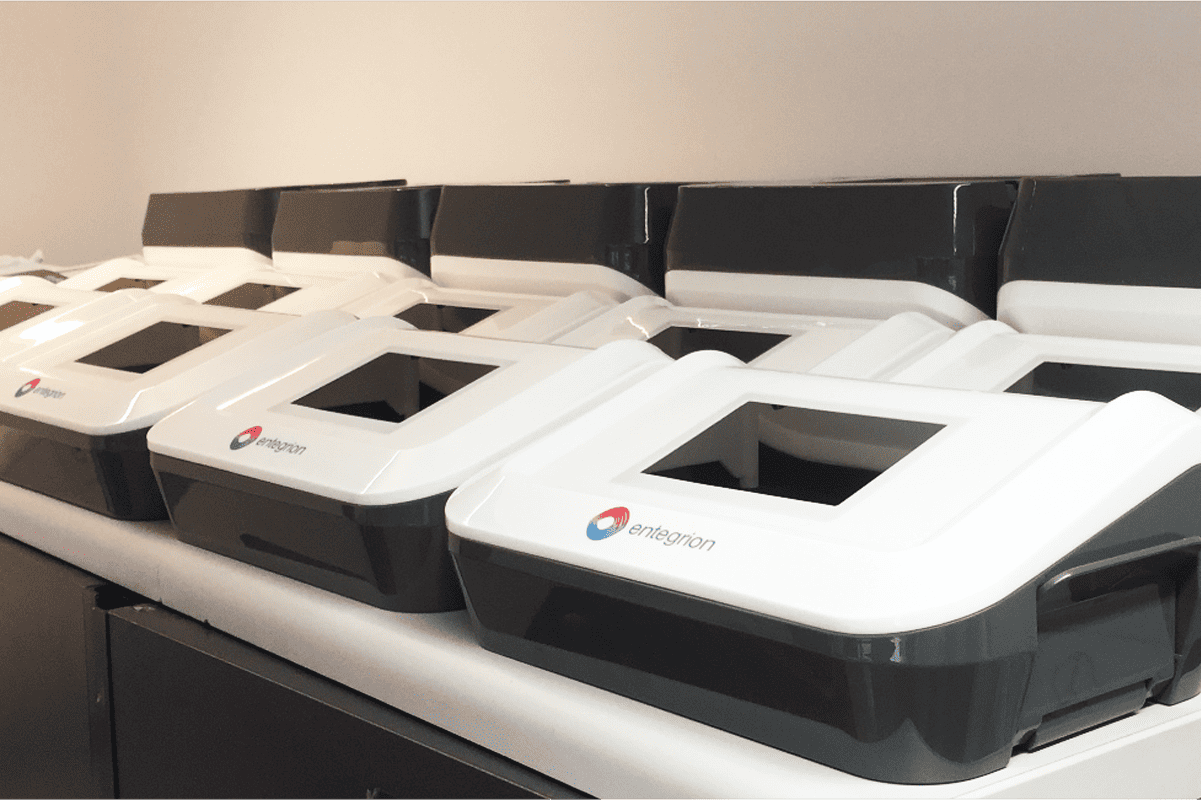
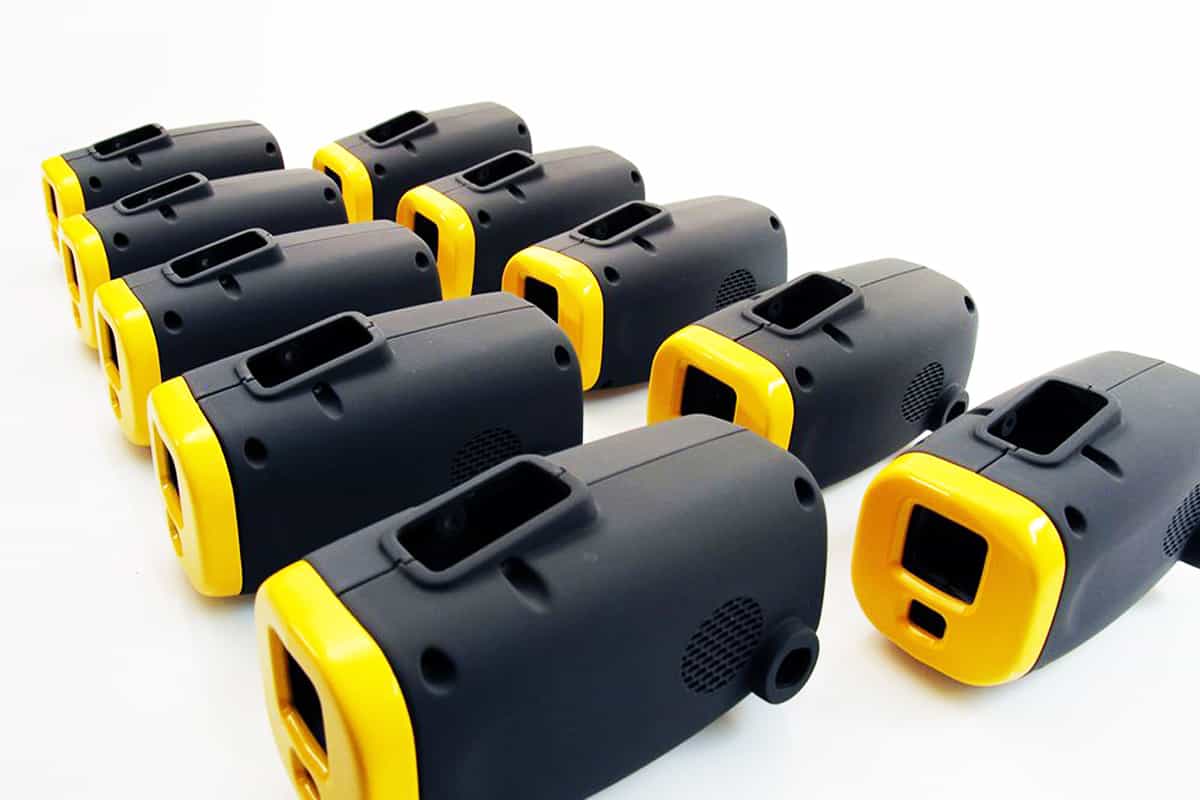

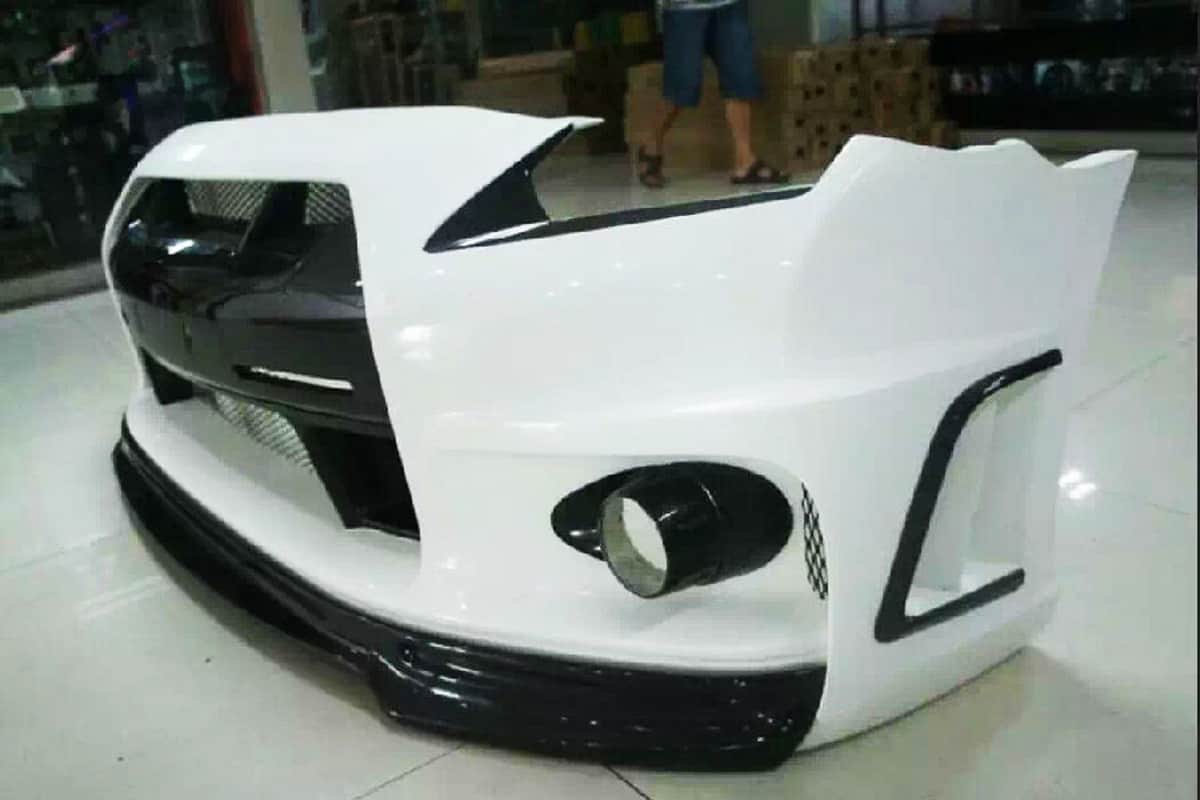
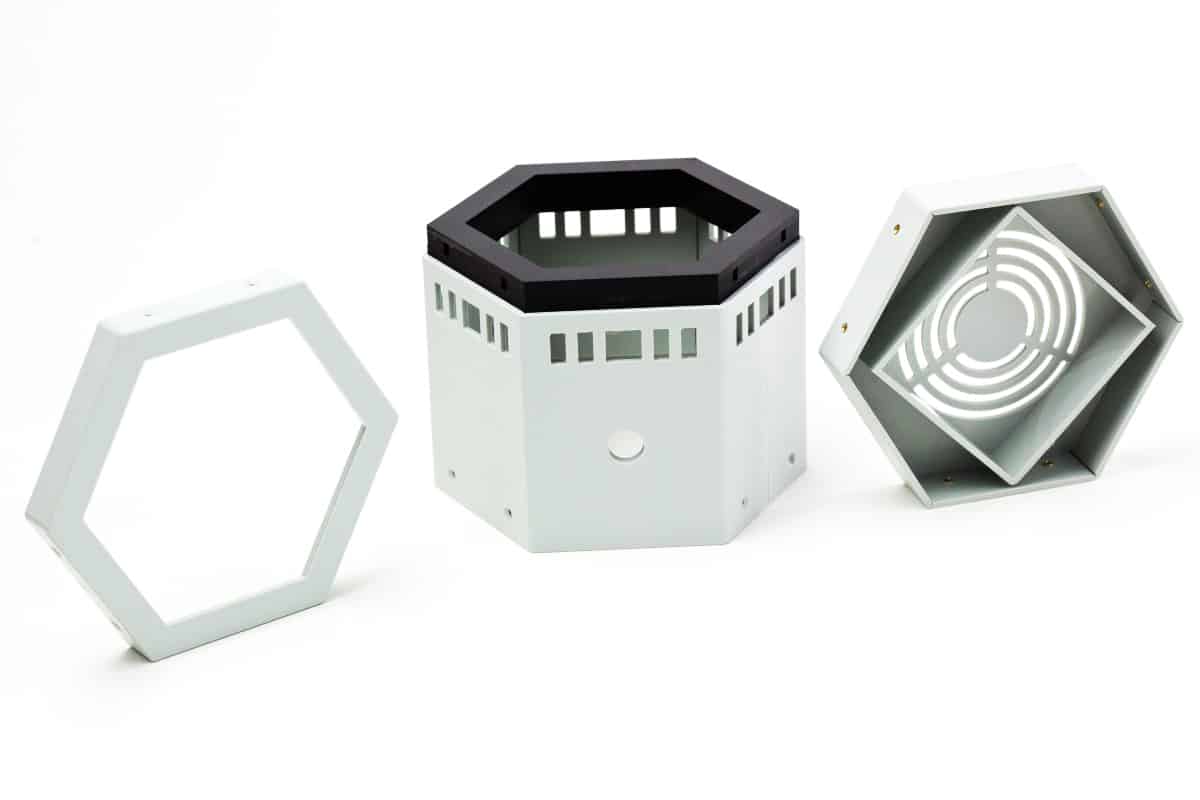
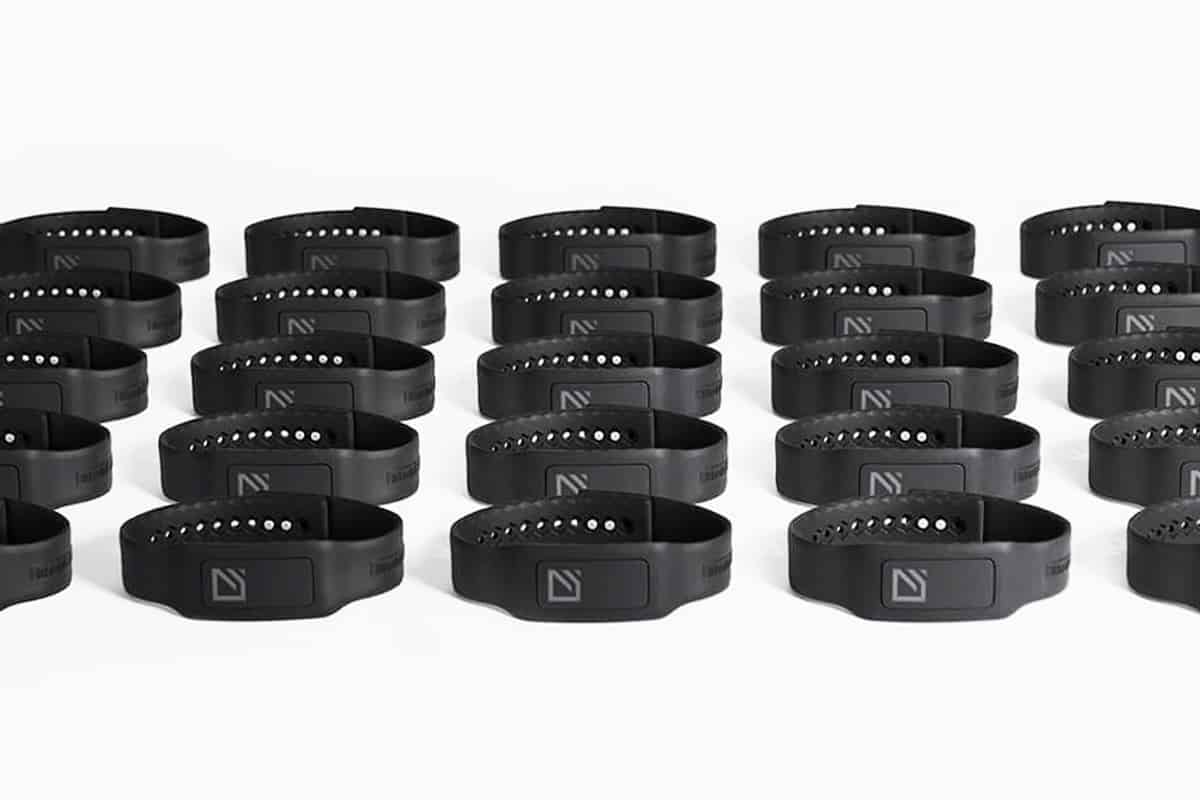
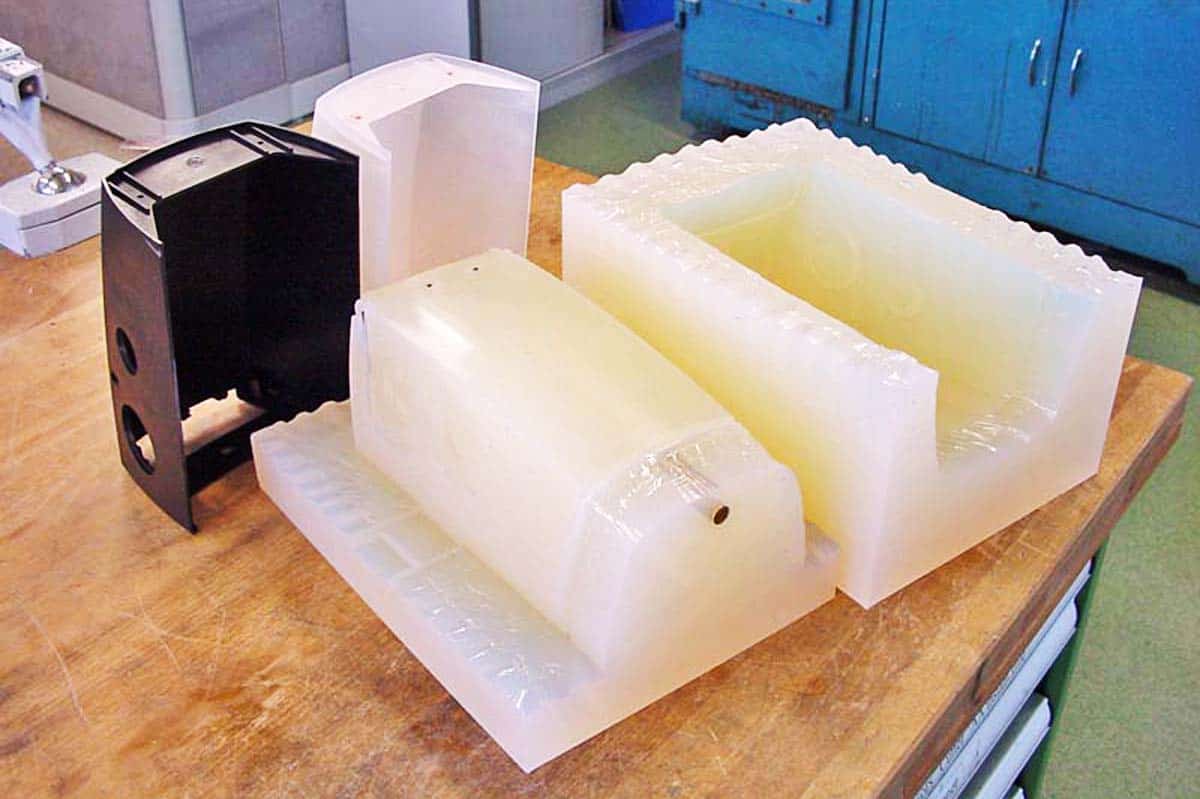
真空注型応用範囲
ポリウレタン注型も小ロットインサート成形または被覆成形の完璧な代替品であり、多種の素材が選択できます。ポリウレタンまたはシリコン注型品は、3 Dプリントの快速プロトタイプ作成と射出成形の間の生産ギャップを埋めることができ、品質、コスト、時間のバランスを取ることができます。ポリウレタン注型品は、透明品、カラーインサート品でも可能です。1つのマスタ品が約20〜50個の複製品を製造できるため、真空注型により、開発者は、初期市場テストのため、最初シリーズ製品として発売されることも可能です。
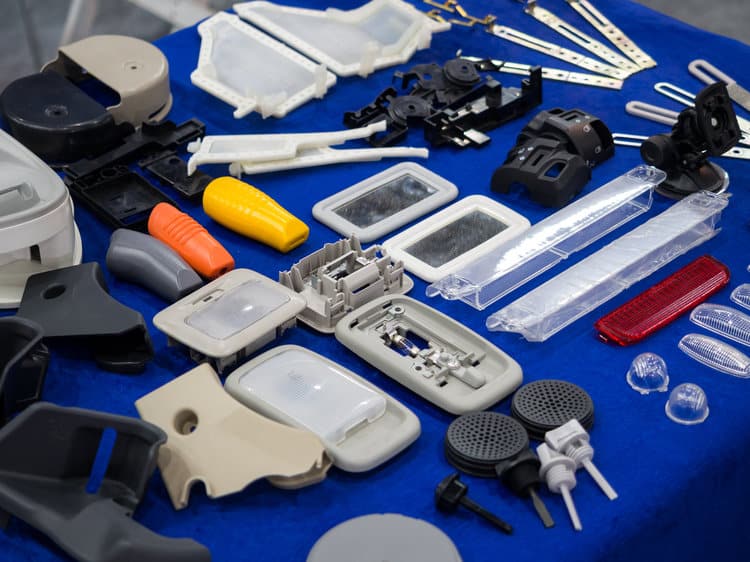
お客様の評価
「私がAN-Prototypeと協力した経験は素晴らしいです。彼らのコミュニケーションは非常に優れており、Michinはいつも私の質問に答えることができます。私たちが受け取った完成品は予想通りの最高品質を持っています。本当に存在するのは、私がいつもMitchinから得ている良質なサービスです。彼はいつも私たちの満足を確保することに力を入れている。総合的には、信頼できるベンダーを探している人にAN-PrototypeとMichinを強くお勧めします。
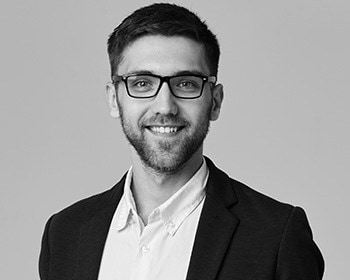
「複雑な5軸CNC加工部品であっても、AN-Prototypeからは非常に良い結果が得られました。過去2年間、AN-Prototypeと共に多くのプロジェクトを手掛けてきましたが、彼らは常に非常に優れた品質(彼からCNC加工サービスとアルマイト処理を薦めてもらったこともできます)、信頼性、非常に迅速で完璧なコミュニケーションを提供してくれました。DavideとVivianとの協力に感謝し、すでに多くのパートナーに推薦しました。

「私のAN-Prototypeに対する体験はとても特別です。最初から通信は正確で迅速であり、難しい設計に対しても、ソリューションを提供します。プロトタイプ制作の価格は競争力があります。最終製品のQCも非常に優れています。続けて加工部品を依頼します。
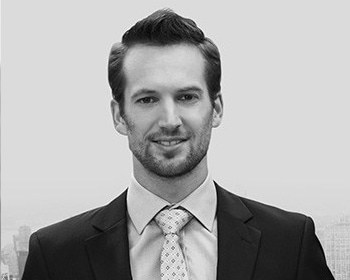