CNC金属加工プロセス
AN Prototypeの内部3軸、4軸、5軸スイスNC工作機械は、スパーク加工、研削、穴あけ、タップなどの技術を組み合わせて、カスタマイズされた金属プロトタイプと最終用途の生産部品を1日内で迅速に製造することができます。
- 高速プロトタイプ作成からロット生産まで
- カスタム部品製造とMOQ1から対応
- ISO9001&13485 認証
- 数日で良質な部品作成
- DFM解析
CNC金属加工ガイドライン
CNC金属加工は、部品製造技術であり、CNC加工、ミリング、旋削、ドリル加工、電気火花とワイヤカット、および研削、タップ加工などの技術に関する加工技術であります。金属から余分な材料を除去し、必要な形状、寸法、表面仕上げにカットすることで、設計およびエンジニアリング図面仕様に合った部品を作成します。社内の最先端のCNC加工設備と経験豊富なメカニックにより、AN Prototypeチームは精密なCNC金属加工サービスを提供することができ、厳格な公差要求と複雑な幾何形状要求によって、カスタム金属部品を処理することができます。私たちのCNC金属能力には、プロトタイプ製造と小ロットカスタム品製造、特にアルミニウムやその他の金属(銅、黄銅、マグネシウム、亜鉛、チタン、鋼、ステンレスなど)のCNC加工、および各種金属部品の表面処理の専門知識を持っています。
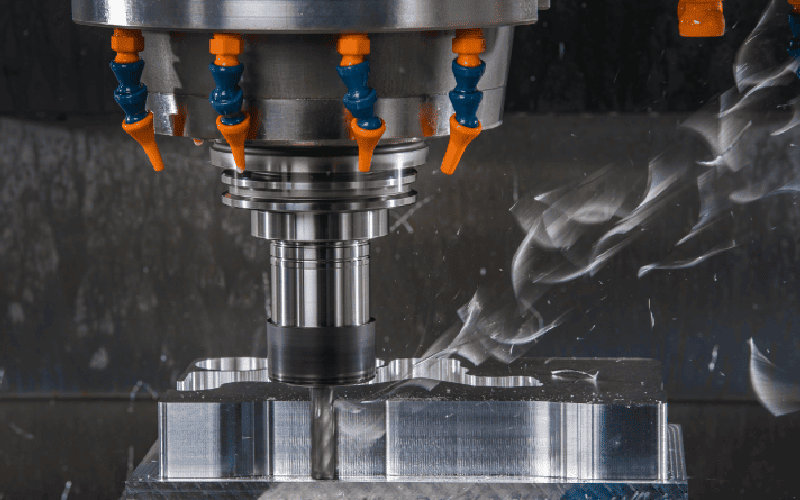
CNC フライス加工
3軸、4軸、5軸NCフライスは切削工具の動作と回転を利用して余分な材料を除去し、精密部品の加工に適用されて、金型を製造する理想的なツールでもあります。
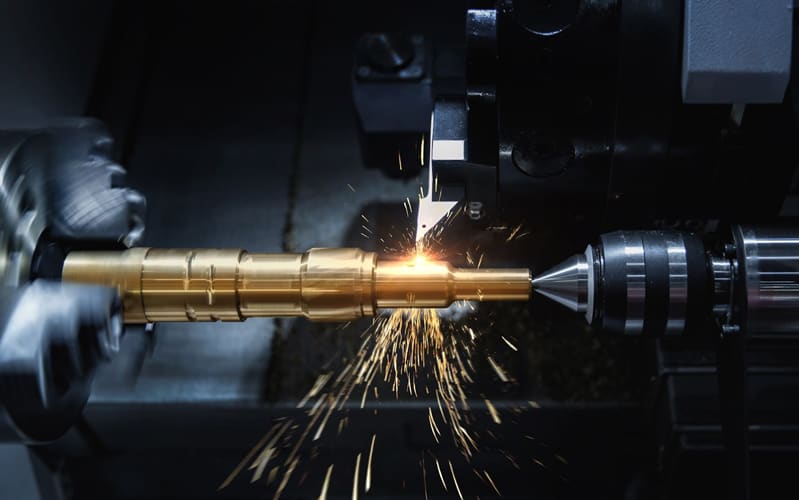
CNC旋削
CNC旋削は、工具を高速回転するワークに接触させることによって材料を除去する。これは通常、円形またはチューブ状の部品を製造するために使用され、さまざまなねじ、内側の穴、その他の構造を持つ部品を加工することもできます。
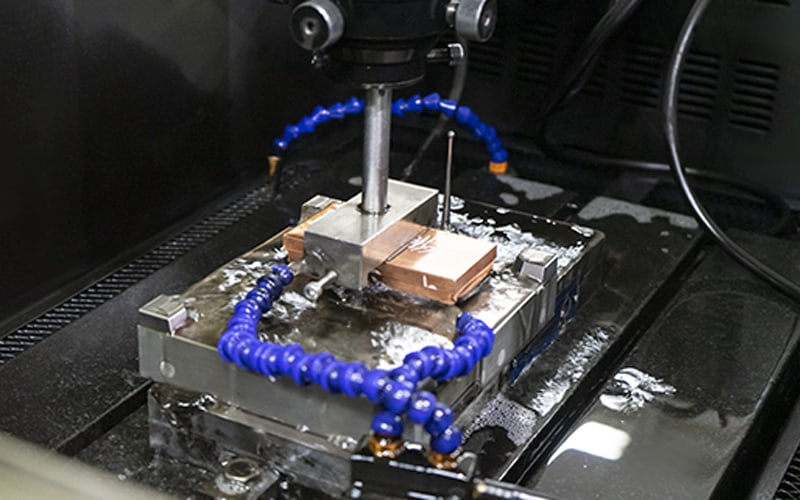
EDM
シンカーEDMとワイヤカットEDMはAN Prototypeが得意とする精密金属加工技術であり、電気エネルギーを使用してワーク上の余分な材料を切断または除去する方法であります。
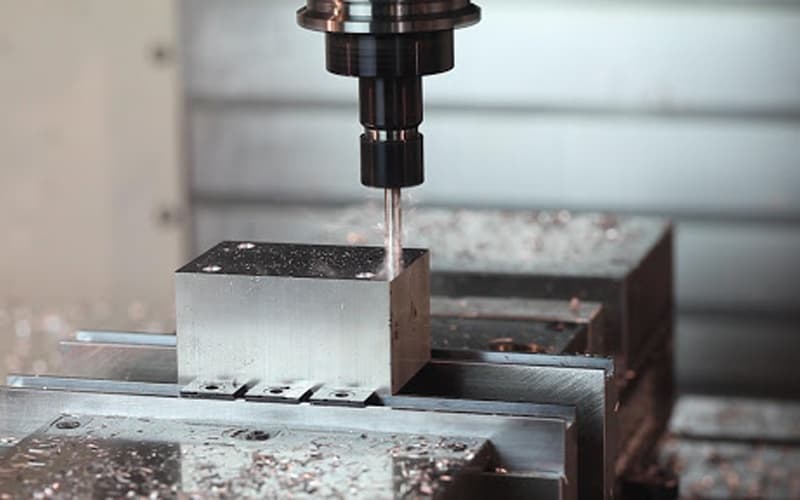
CNCドリル
CNCドリルは、回転切削工具が固定されたワークに丸穴を加工する方法です。このドリル穴は、後工程の部品を固定するネジとボルトを収容するためのものです。
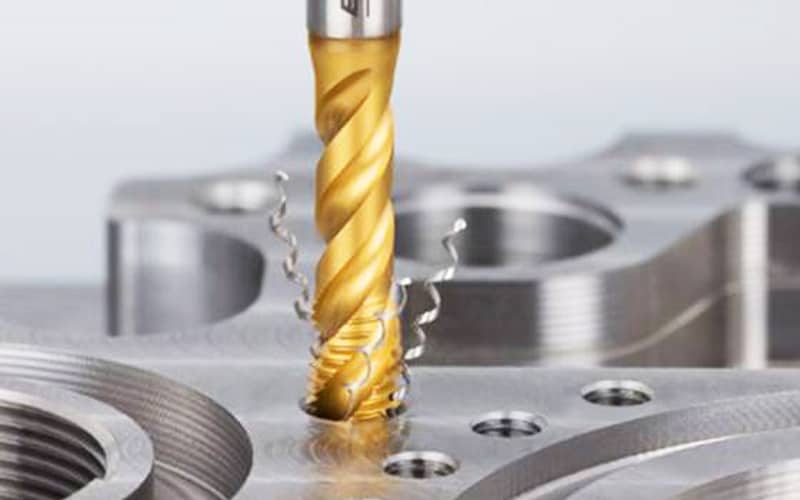
CNC タップ
CNCタップは、ドリル対象部品のベース穴にタップをねじ込んで、必要なねじ山を形成することです。これは非常に効率的で、経済的で、簡単なねじ加工技術です。
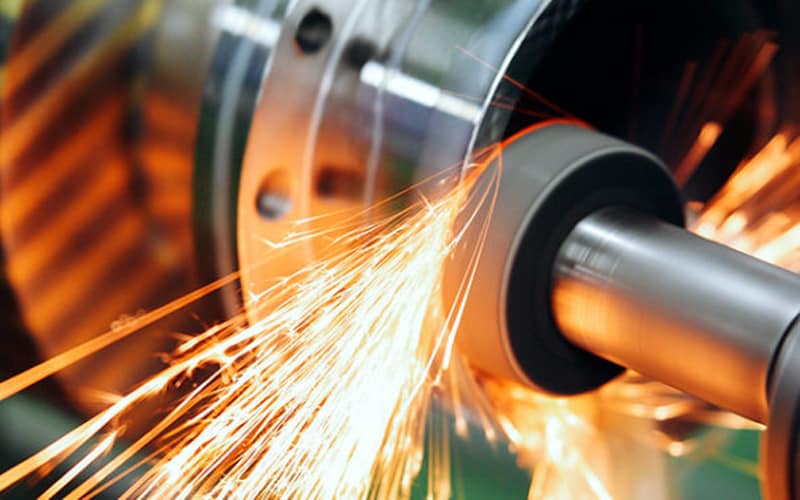
精密研磨
精密研磨は、研磨材粒子で作られた回転工具によって部品から余分な材料を除去し、部品に必要な正確な表面と寸法を作成する方法です。
CNC金属加工
CNC加工は、金属加工に最適なプロセスであります
精密CNCフランスと旋削により、さまざまな金属材料を使用して部品加工は簡単にできます。これは、設計エンジニアはプロトタイプと製品を加工する時、参考になります。
柔軟で効率的な製造
金属は一般的に硬いですが、鋭利なCNC工具は簡単に金属を切断することができ、高品質の金属部品を製造する最適な方法である。
短納期
CNCで最初の金属部品を加工するのに3日かかりますが、100個の金属部品を製造するのに7日しかかからないです。
人を減らす、コスト削減
CNC金属加工はコンピュータ制御のCNC旋盤であり、多くの作業者は必要なくなって、生産コストを削減できます。
高精度と再現性
CNC金属加工はより高い精度を実現でき、同じ部品を繰り返し製造するには自動プログラムによって加工作業を行います。
CNC金属加工プロセスはどのように作業されていますか
CNCは効率的な自動作業旋盤であり、機械設備とCNCシステム組み合わせた複雑な形状部品を製造する加工方法であります。CNC旋盤には自動的にチェンジ機能を備えたツールメモリ装置が設置されて、ワークを1回クランプして複数の工程加工を行うことができます。CNCシステムはツールの自動チェンジを制御することができ、各金属加工によって、主軸回転速度、送り速度など操作を選択し、それによってドリル、ボーリング、フライス、ヒンジ、タップなどの工程を連続的に完成する。CNC制御金属加工はワークのクランプ、測定、工作機械の調整などの補助クランプ時間を大幅に削減し、加工形状が複雑で、精度が高く、再現性の要求が高い部品に適用されます。
CNC加工に適用な金属材料
AN Prototypeの米国と日本から購入したCNC旋盤の剛性は、ほとんどの金属材料が加工できることを確保できます。普通のアルミニウムから各等級の鋼とステンレス鋼まで、超硬ニッケル鋼合金などを加工できます。CNC加工は、加工性パラメータが最も悪いマグネシウム合金とチタン合金にも適用されます。
- アルミニウム6061
- アルミニウム7075
- アルミニウム2024
- アルミニウム6063
- アルミニウム6082
- アルミニウム6060
- アルミニウム5083
- ブラス C360
- ブラス 110
- ブロンズC932
- ステンレス 17-4
- ステンレス 303
- ステンレス 304
- ステンレス 316
- ステンレス 1018
- A36 鋼
- 合金鋼 4140
- マグネシウム(AZ91D / AZ31B)
- チタン(Ti-6AI-4V)
- 亜鉛 (亜鉛合金3 / 亜鉛合金5)
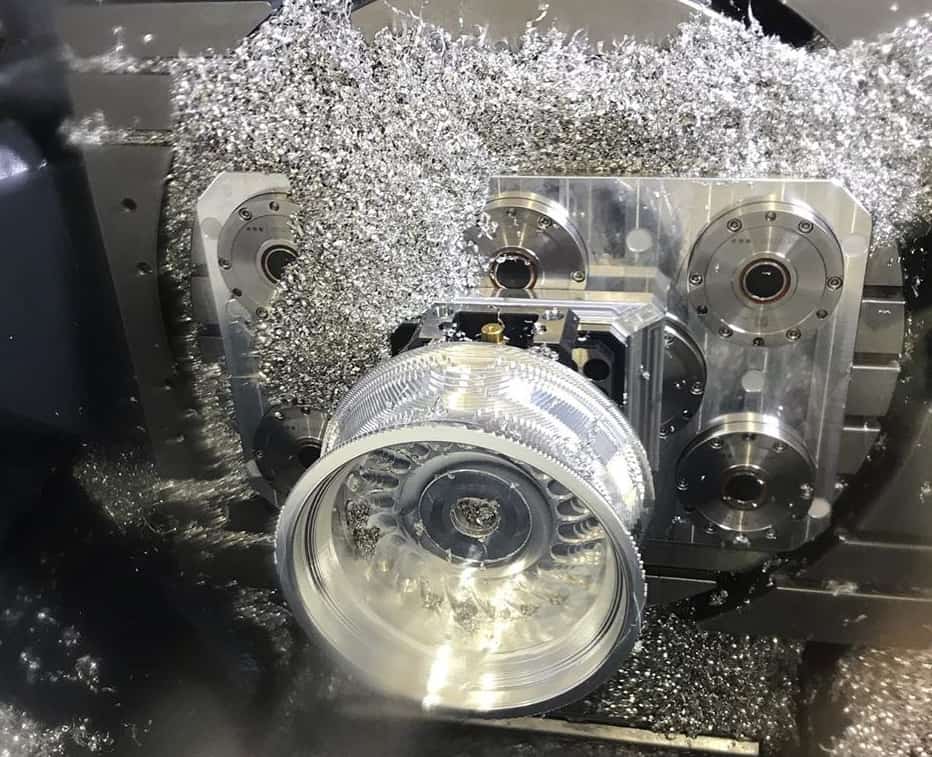
一般的な金属の性質について
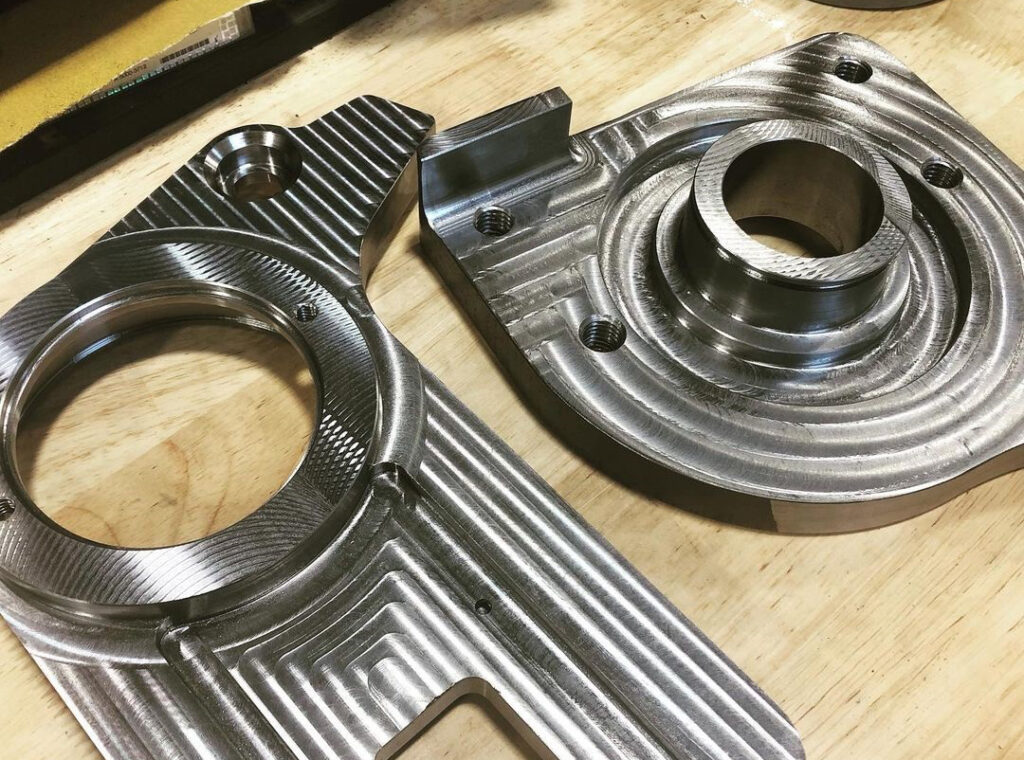
アルミニウム 6061
アルミニウム6061はCNC加工の最も一般的な材料である。アルミニウム6061の合金元素はマグネシウム、シリコン、鉄である。他のアルミニウム合金と同様に、良好な強度比重を持って、天然耐腐食性を持っています。アルミニウム6061は良好な加工性とCNC加工性を持って、溶接とアルマイトが可能であり、その広く使用されているのはそれが経済的であることを表示しています。
熱処理がT 6状態になると、6061の降伏強度はアニール後の6061よりはるかに高くなり、その分価格もやや高くなります。6061の欠点の1つは、塩水または他の化学物質に暴露されると、その耐食性が相対的に劣ることである。アルミニウム6061は、自動車部品、自転車フレーム、ハウジングなどによく使用される材料であります。
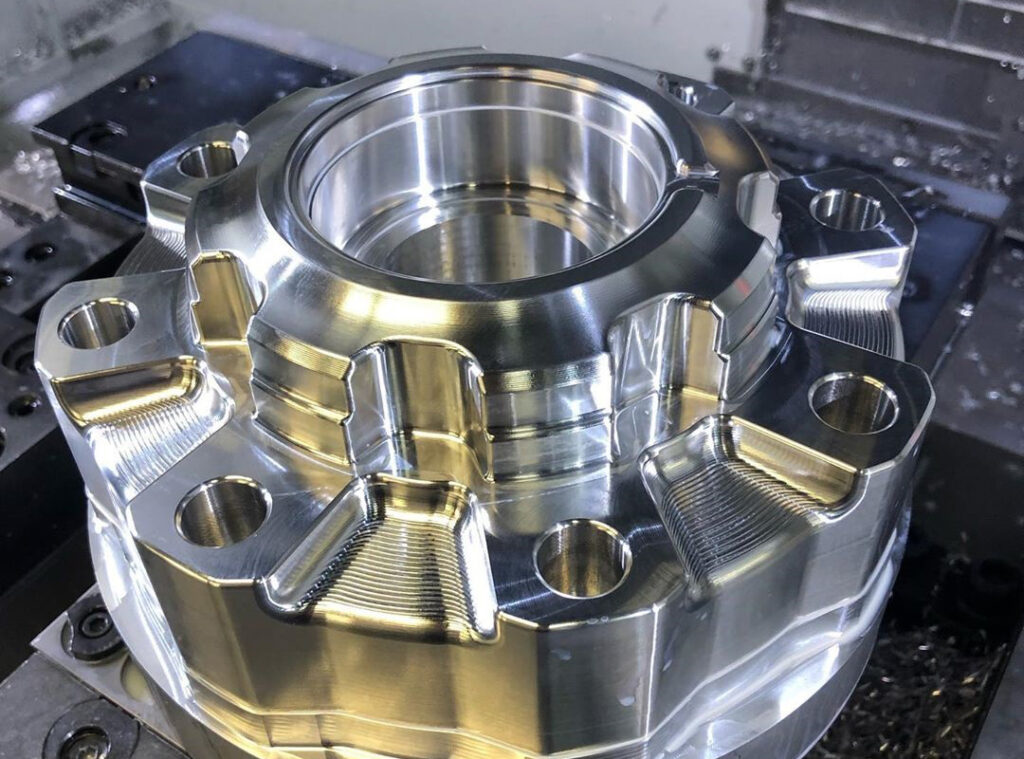
アルミニウム7075
アルミニウム7075は高級アルミニウム合金であり、その主要合金元素の亜鉛含有量が比較的に高い。アルミニウム7075は強度が最も強いアルミニウム合金の1つであり、優れた強度重量比を有する。アルミニウム7075は、アルミニウム6061よりもCNC加工が難しい。強度の原因で、冷間成形する時に元の形状に戻ります。アルミニウム7075もアルマイト可能です。
アルミニウム7075は通常、T 6まで硬化してからアニールされますが、これは溶接に対して悪い影響があるので、ほとんどの場合は避けるべきである。私たちは通常アルミニウム7075 T 6によって高速射出成形金型を作ります。通常、自動車、航空宇宙フレーム、およびより軽量な力を必要とする他の部品に使用されています。
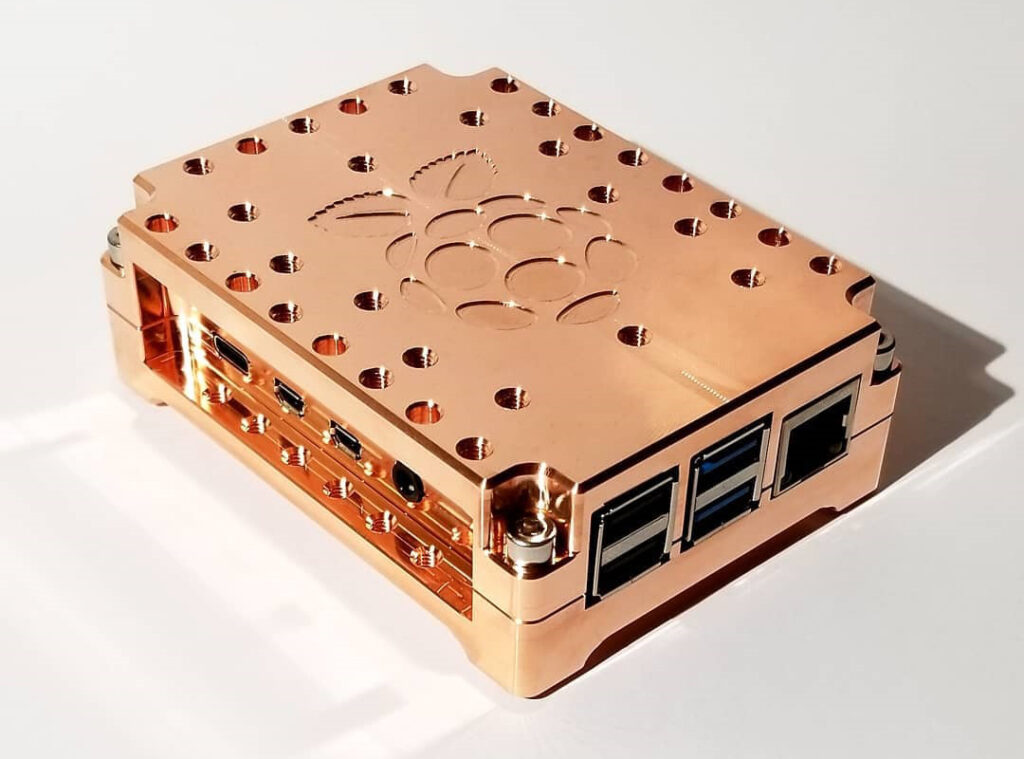
銅
黄銅と同様に、銅はCNC加工において非常に有効である。これは、CNC加工金属の最もコスト効率の高い方法の1つでありますが、原材料の価格が銅のコストを押し上げている。それでも、銅は良好な導電性と熱伝導性を必要とする用途で人気があります。自動車、消費電子、医療保健などの業界では、このCNC金属加工品すごく役に立っています。その他の性能としては、良好な耐食性が挙げられる。AN PrototypeはCNC加工用の2種類の銅合金を扱っています。
- 110銅は優れた導電性と成形性を持っています
- 101銅の銅含有量が最も高く、導電性が最も良い。
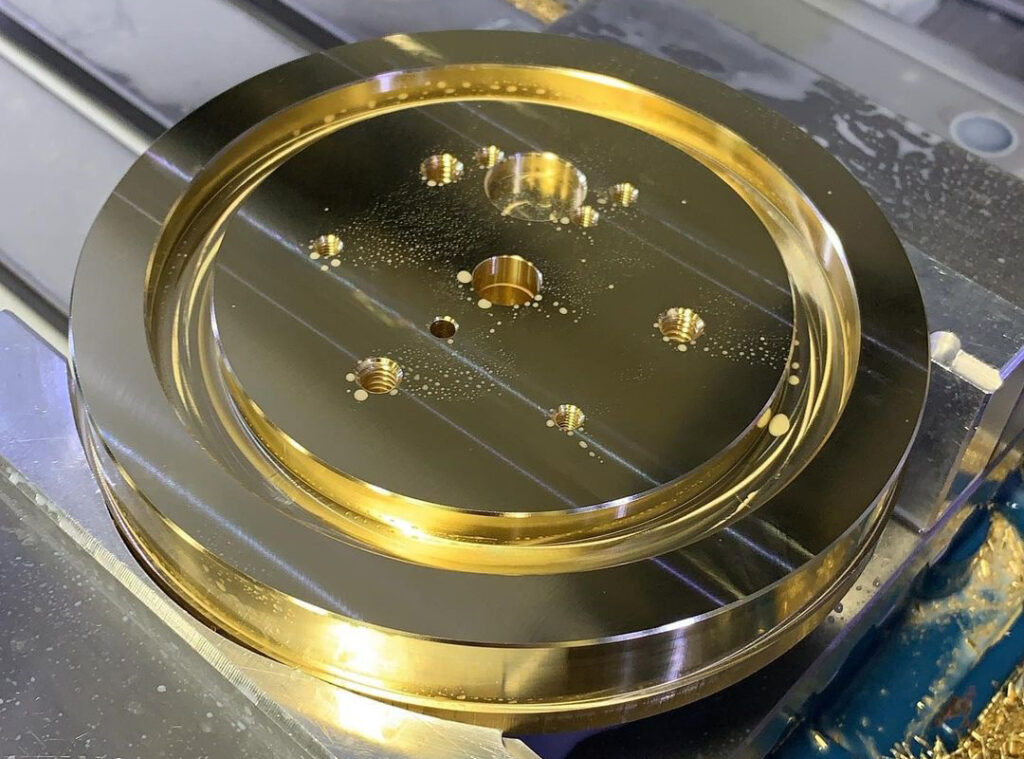
黄銅
黄銅は銅と亜鉛の合金で、比較的柔らかい金属であり、通常は潤滑なしでCNC加工を行うことができる。黄銅は室温でも加工が容易であるため、通常は高強度を必要としない用途範囲に使用されています。亜鉛の含有量によって、黄銅の種類が変わります。亜鉛の比率が増えることによって、耐食性は低下されます。黄銅は高度に研磨されることにより、金のように見えるので、飾り範囲によく応用されています。黄銅は導電性がありますが、磁性がないので、簡単にサイクル利用できます。
黄銅は溶接されますが、最も一般的なのはろう付けなどの低温プロセスで溶接されます。黄銅のもう1つの特性は、他の金属と衝突したときにスパークが発生しないので、潜在的な爆発性環境に使う部品に適用されます。黄銅は天然的な抗菌性と抗菌性を持って、その薬用価値はまだ研究されています。黄銅は通常、配管部品、家庭装飾金物、ファスナー、楽器に良く使用されています。
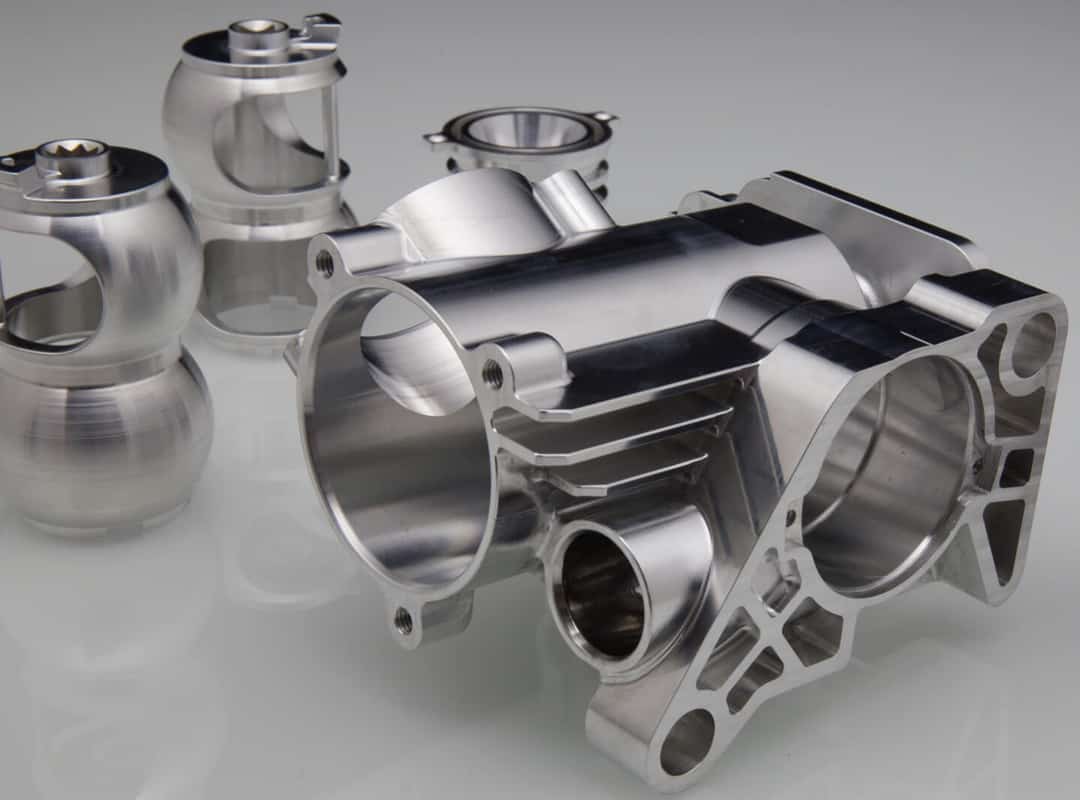
ステンレス 303
ステンレス303合金には硫黄が含まれている。この硫黄は303を最も加工しやすいステンレスになるのに役立ち、同時に耐食性を低下させます。ステンレス303は熱処理ができず、溶接に適していない。優れたCNC加工能力を持っていますが、速度/投入と工具の鋭さに注意しなければなりません。303は通常、ステンレスナットとボルト、部品、シャフト、ギアなどに使用されます。
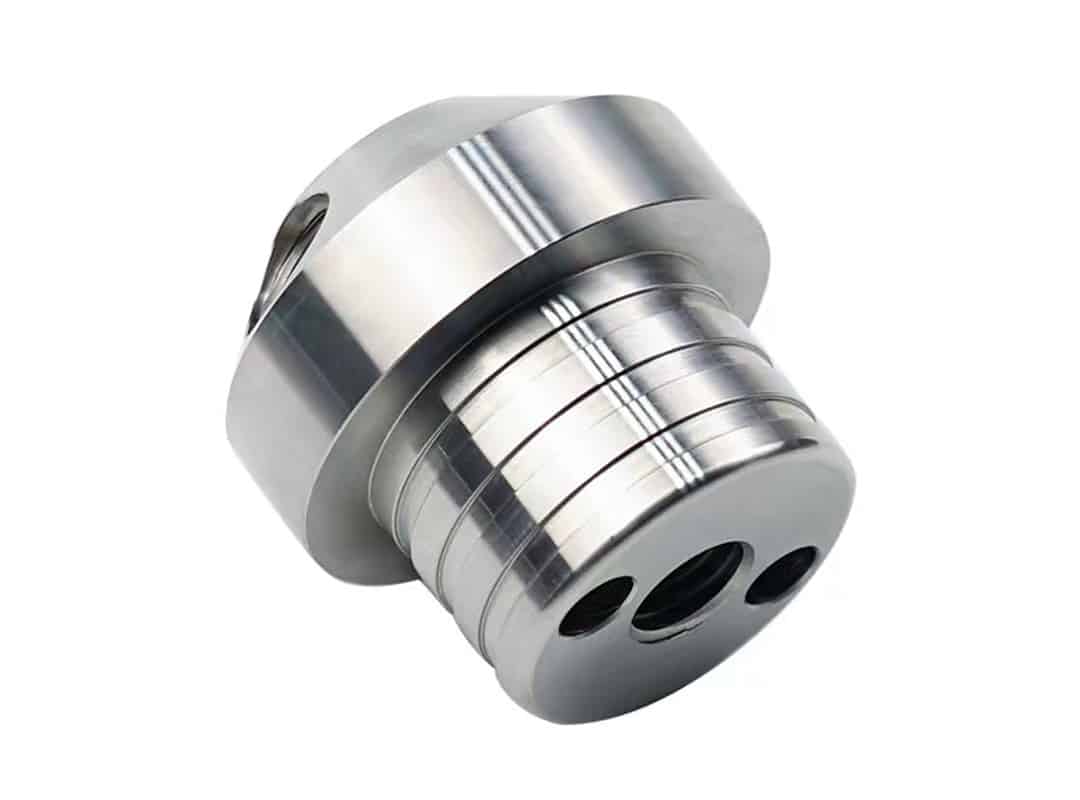
ステンレス304
ステンレス304は、簡単にCNC加工できる材料である。その大きな利点は溶接ができることです。ほとんど(非化学)環境で耐腐食性であります。加工するには、他の金属に汚染されないように、非常に鋭いCNCカッターを使用する必要があります。ステンレス304は工業、建築、自動車に広く応用されて、台所部品、食器、タンク、配管を製造する絶好の材料選択であります。
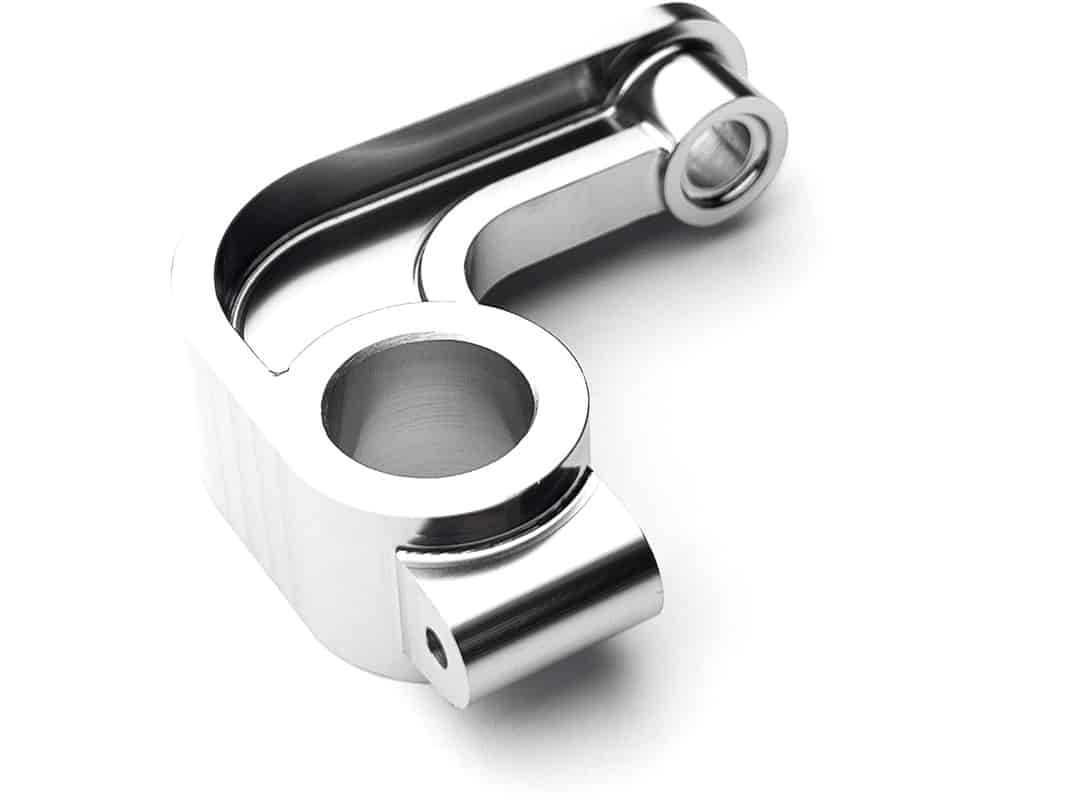
ステンレス316
316ステンレスは、オーステナイトステンレスであり、合金元素モリブデンが入って、優れた耐食性があります。それ以外にも、高い成形性と溶接性を持っています。316は、建築物及び船舶部品、工業用配管及びタンク、自動車装飾及び台所用具に使用されてます。海洋や化学工業など、より極端な応用に適用されています。
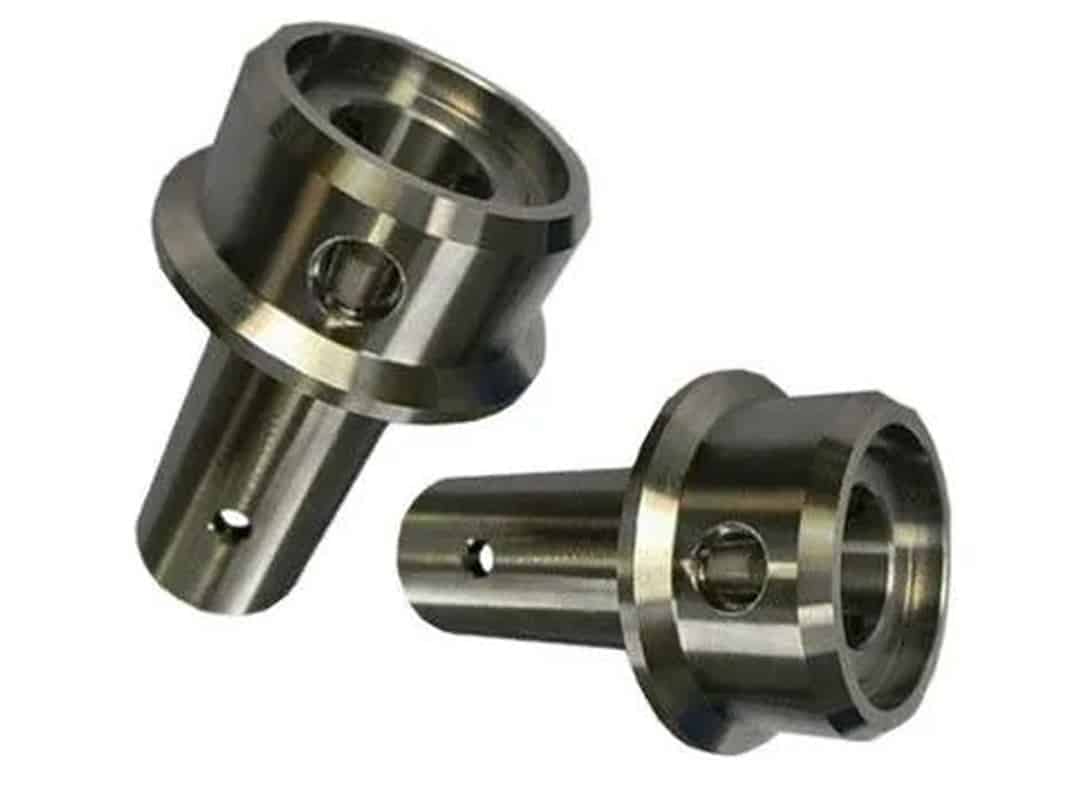
炭素鋼1045
炭素鋼1045は、ステンレス鋼ではない一般的な低炭素鋼であり、通常ステンレスより安いですが、より固くて強靭であります。炭素鋼1045でCNC加工と溶接が簡単であり、硬化と熱処理によって、様々な硬度に加工することができます。1045鋼は、ナットとボルト、歯車、シャフト、リンク、およびステンレス鋼よりも高い靭性と強度を必要とする他の機械部品を製造するために使用されています。建築にも使用されていますが、環境に露出すると錆を防ぐために表面処理が行われることが多いです。
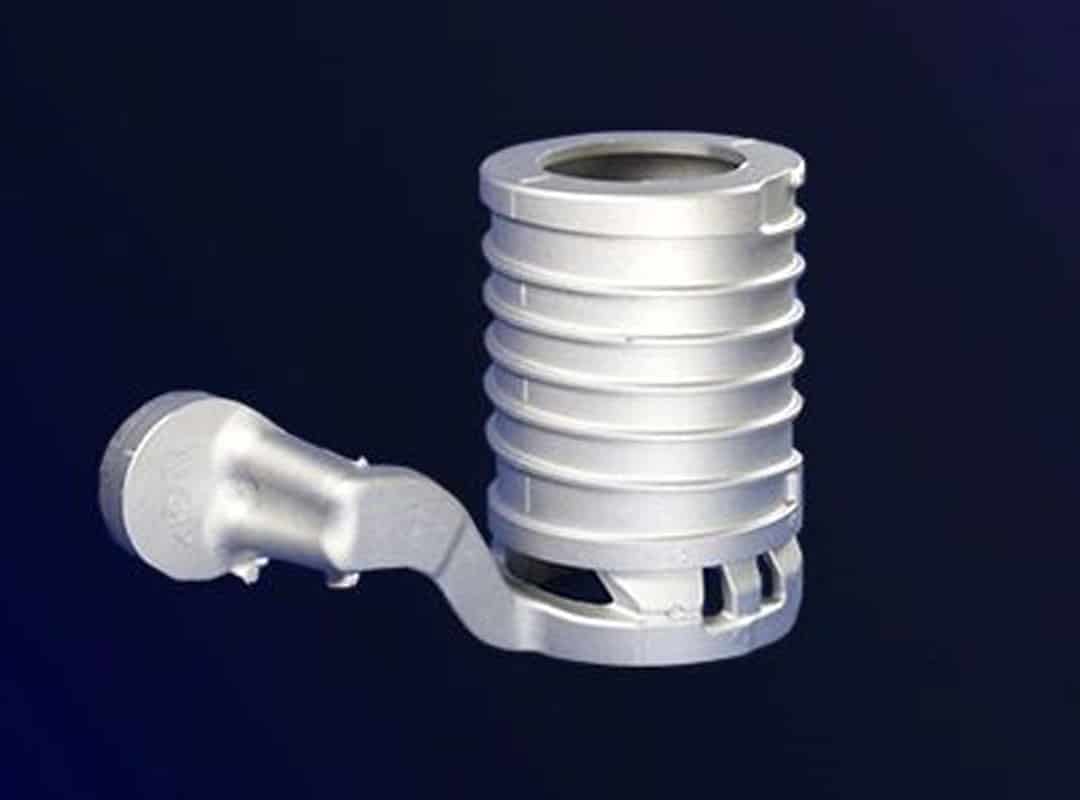
マグネシウムAZ 31
AZ 31マグネシウムはアルミニウムと亜鉛が入っている合金元素で、最も軽い金属の一つである。同じ強度では、AZ 31マグネシウムはアルミニウムより35%軽いですが、値段がアルミニウムより高いです。マグネシウムでCNC加工するには非常に難しくて、非常に燃えやすいため、CNC加工には液体潤滑剤を使う必要があります。マグネシウムはアルマイト後、耐食性が高くなります。AZ 31マグネシウムは通常、軽量で高強度を必要とする航空機部品に使用されて、カメラケース部品にも使用されます。
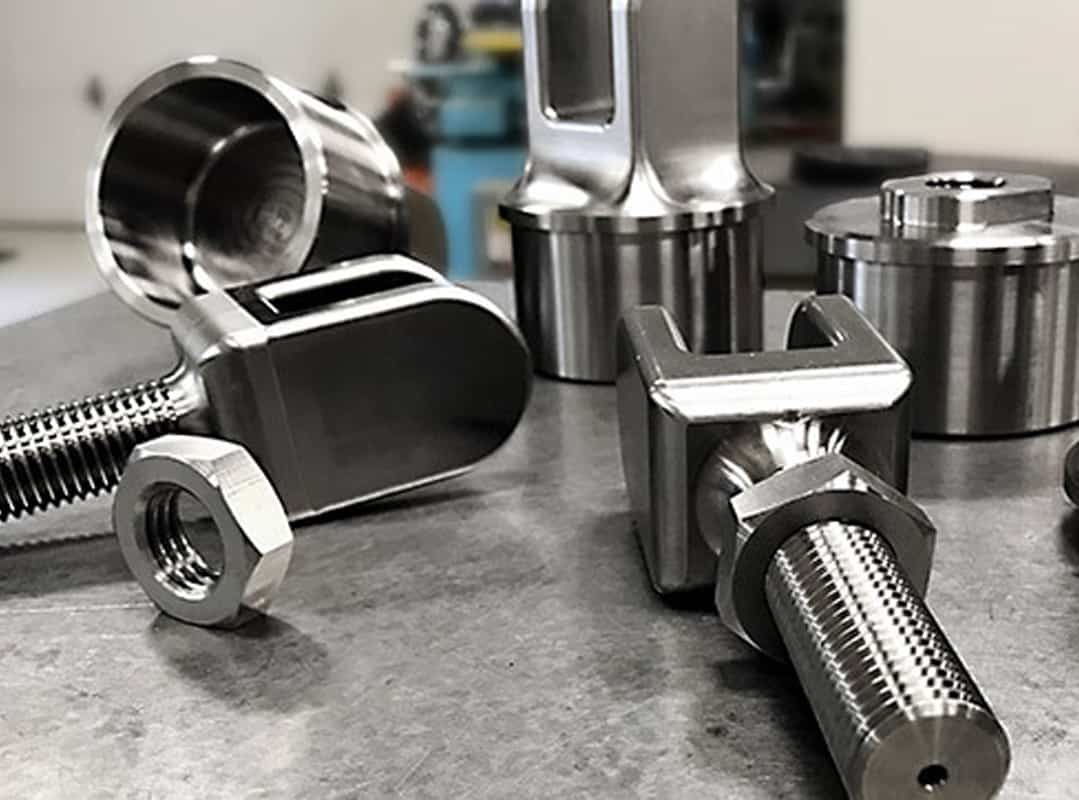
チタン合金
チタンはその強度、軽量、靭性、耐食性で知られている。また、溶接、クロメート、アルマイトを行うことができ、保護性を高め、外観を改善することができます。チタンは良い熱導体であり、悪い電気導体の材料です。CNCでチタンを加工するには非常に難しくて、専用のツールしか使用できません。チタンは通常、生体適合性があり、融点が高いことに注意していただきたいです。それは最も要求の厳しい航空宇宙、軍事、生物医学と工業応用に適用されて、高温と腐食性酸によく耐えられます。チタンも3 Dプリントによく見られる材料です。
CNC加工部品の仕上げプロセス
CNC加工は、原材料から余分な部分を除去して必要な形状を形成するプロセスである。加工部品の表面にはツール跡が残ります。CNC加工部品の性能と見栄えを向上させるために、AN Prototypeはサンドブラスト、ミラ面研磨、塗装、シルク印刷、レーザーエッチング、アルマイト、めっき、クロメート、ニッケルめっき、クロムめっき、粉末コーティングなどが含めたCNC加工部品にワンストップ表面処理サービスを提供しています。
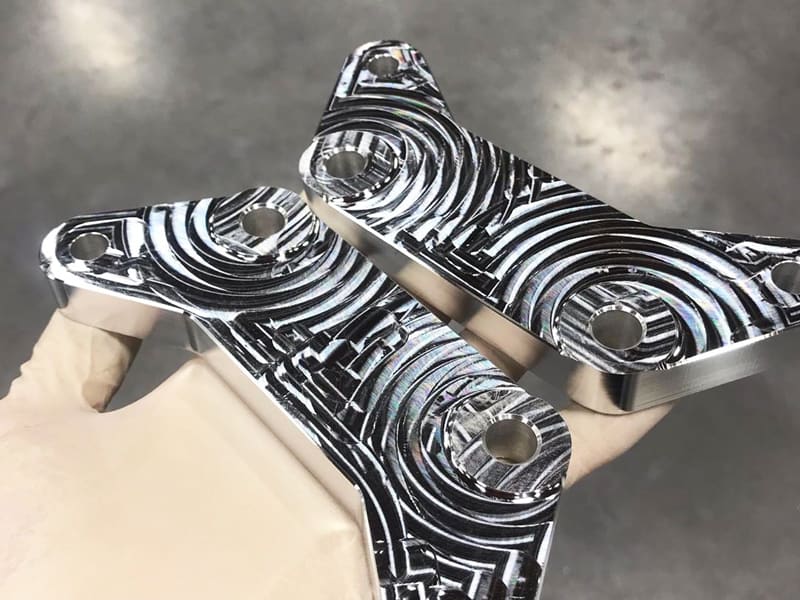
機械加工
標準の「機械加工」部品の表面粗さは3.2µmで、鋭いエッジとバリ取り部品をきれいに除去することができます。滑らかな加工表面粗さはRa 1.6〜0.8μmで、超仕上げ加工の表面粗さはRa 0.8〜0.2μmまで対応できます。
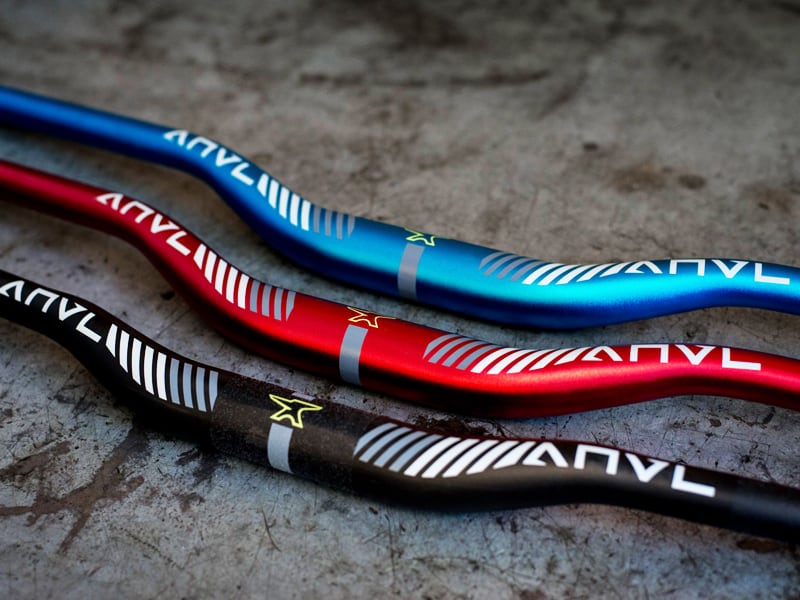
アルマイト
アルマイトは耐食性、耐摩耗性、絶縁性の特徴があり、部品の性能を長い時間維持することができる。アルマイトは一般的にアルミニウム合金部品に使用されて、美学的効果が作られます。すべてのiPhone製品はアルマイト処理されています。
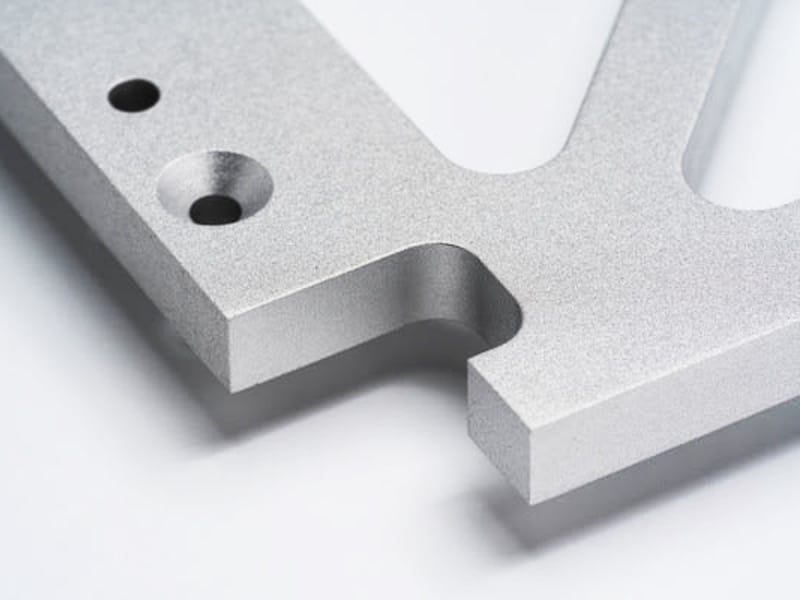
粉末塗装
粉末塗装はコロナ放電現象を利用して部品表面に薄い保護ポリマーを付けて、厚さは約50μmから150μmまでで、耐摩耗性の層により頑丈で耐摩耗性のある表面を作ります。
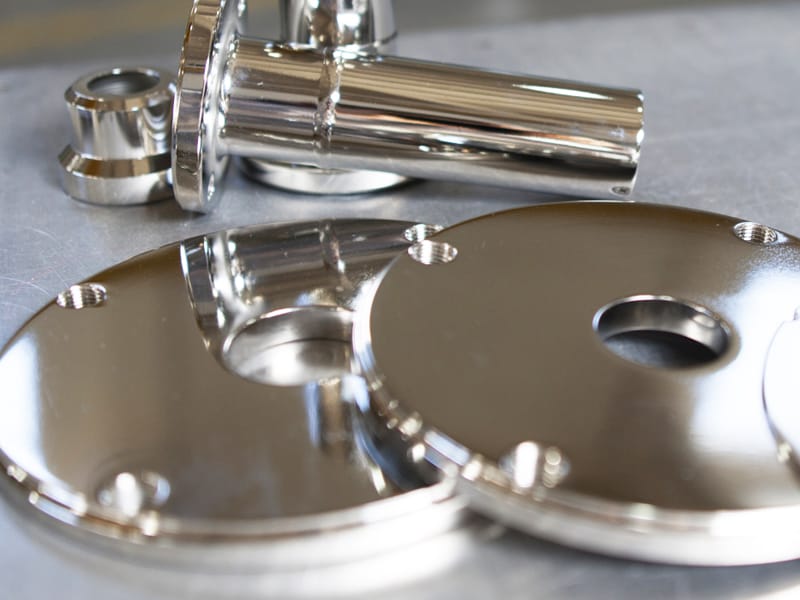
メッキ
めっきは、合金、カドミウム、クロム、複合材料、金、ニッケル、ロジウム、銀、錫、亜鉛、亜鉛ニッケルなどの金属を導電性表面上に堆積するための精密加工プロセスであります。
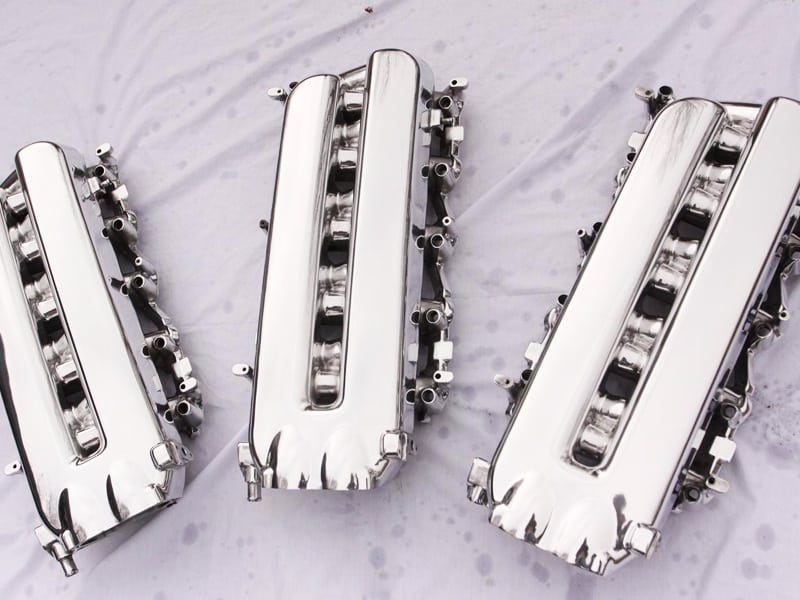
ミラ面研磨
ミラ面研磨 ミラ面研磨は粗い研磨ペーパーから、プロトタイプに光沢や鏡面的な外観を持たせる2000粒度まで徐々に追加します。例えば、透明な自動車ライトガイド、ヘッドライト、リアテールランプがあります。プロトタイプの表面は十分に滑らかであります。
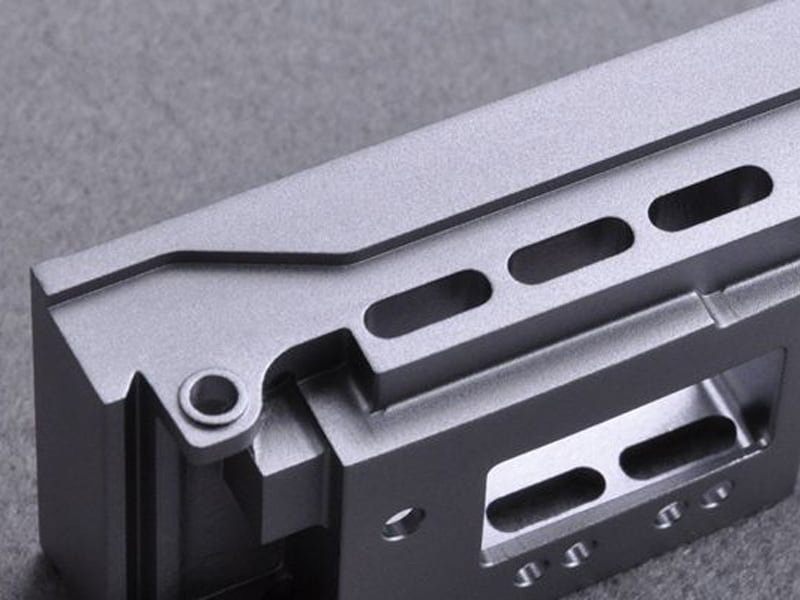
サンドブラスト
サンドブラストとは、微粉砕ガラスビーズ粒子が高圧条件でプロトタイプ表面に衝撃を与えることによって、CNCプロトタイプの表面に粒子状の凹みが発生して、それによってサブライトまたは侵食表面の仕上げが作られます。ガラスビーズのサイズは、#80から#220までです。
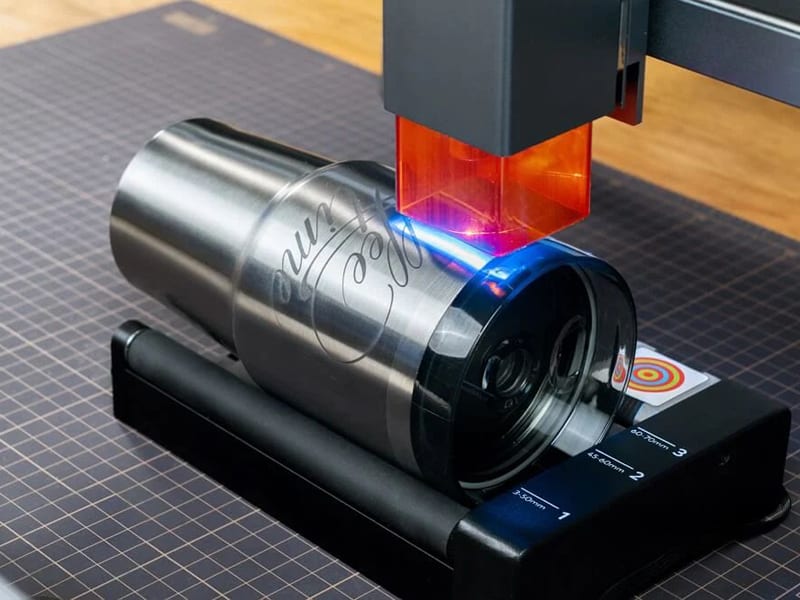
レーザエッチング
レーザエッチングは、特性または美的価値のある永続的なマーキングを作成するために材料の表面を変更するプロセスである。レーザーエッチングに最も一般的に使用される金属材料としては、アルミニウム、ステンレス鋼、亜鉛が挙げられ、その他の非金属材料としては、ガラス、ポリマー、セラミックスが挙げられます。
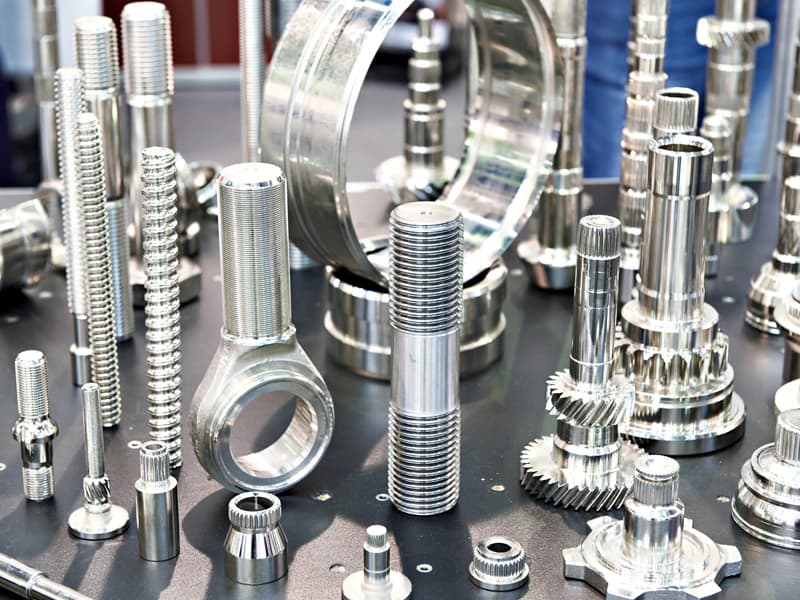
クロメート
クロメートは金属表面を酸化しにくい状態にして、金属腐食速度を遅らせる方法である。クロメートの過程でよく使われる材料はステンレス鋼であり、その耐食性をさらに高めます。