カスタム部品製造能力
- 高速プロトタイプ作成からロット生産まで
- 45,000+製造された独自の部品
- カスタム部品製造&最小発注量1件から
- 3,000社以上の企業へサービスを提供
標準製造サービス
独自のプロトタイプ設計と低ロット生産のニーズに対応するために、カスタム部品製造総合的な能力を持っています。私たちの専門知識はCNC加工、射出成形、板金製造、3 Dプリント、真空鋳造などの先端技術などが含めています。私たちはお客様のアイディアを完璧な物理的な形で現実にすることができると信じています。
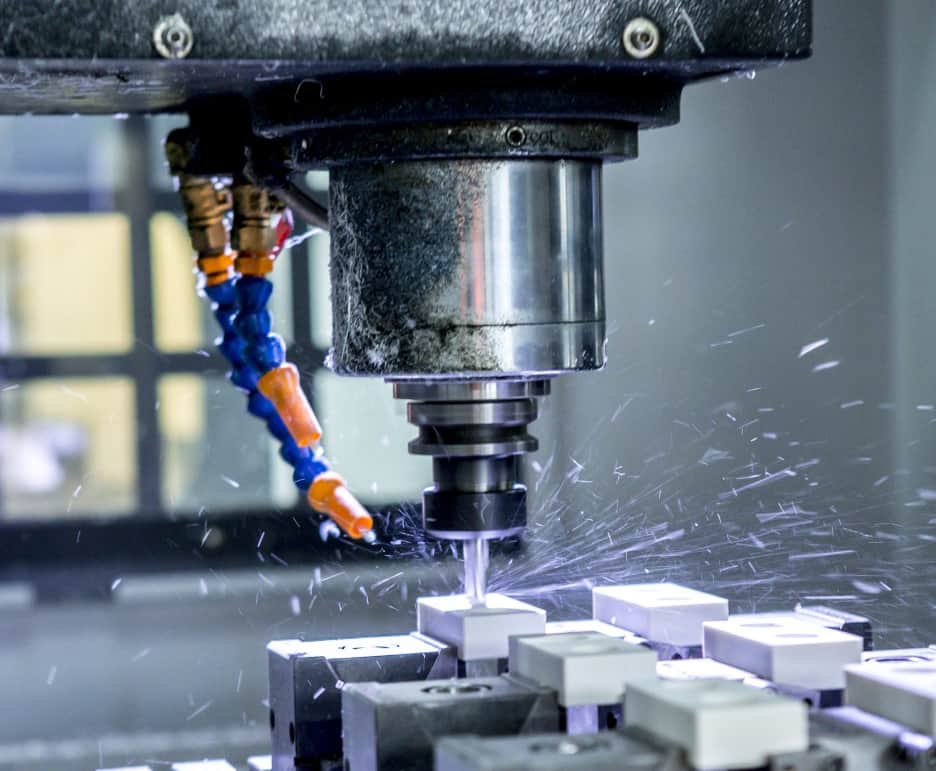
CNC加工能力
AN Prototypeは、カスタム部品の多種製造ニーズによって、3、4、5軸CNCフランス、CNC旋削、表面処理サービスなどの精密CNC加工サービスを提供しています。
- リニア公差:+/-0.005mm
- 钻孔公差: +/- 0.005mm
- 穴径公差: +/- 0.005mm
- 軸直径公差: +/- 0.025 mm
- スレッド公差: Φ 1.5-5 mm
- スレッド深さ: 3×diameter
- タップ穴直径: >Φ 5 mm
- タップ穴深さ: 4-6×直径
- 部品最大寸法:4000mm×1500mm×600mm
射出成形能力
AN Prototypeは、お客様のプラスチック部品製造要求によって、カスタム射出成形サービスを提供しています。私たちのサービスには、高速金型、シングルキャビティ金型、マルチキャビティ金型、被覆成形、インサート成形、マイクロ成形、医療成形などが含まれています。加工品種類によって、それの製造基準に従っています。
- 最大部品サイズ: 1200×1000×500 mm
- 最小部品サイズ: 1 x 1 x 1mm
- 模腔公差: +/- 0.05mm
- 金型タイプ:鋼とアルミニウム
- 製造種類: 101/102/103/104/105
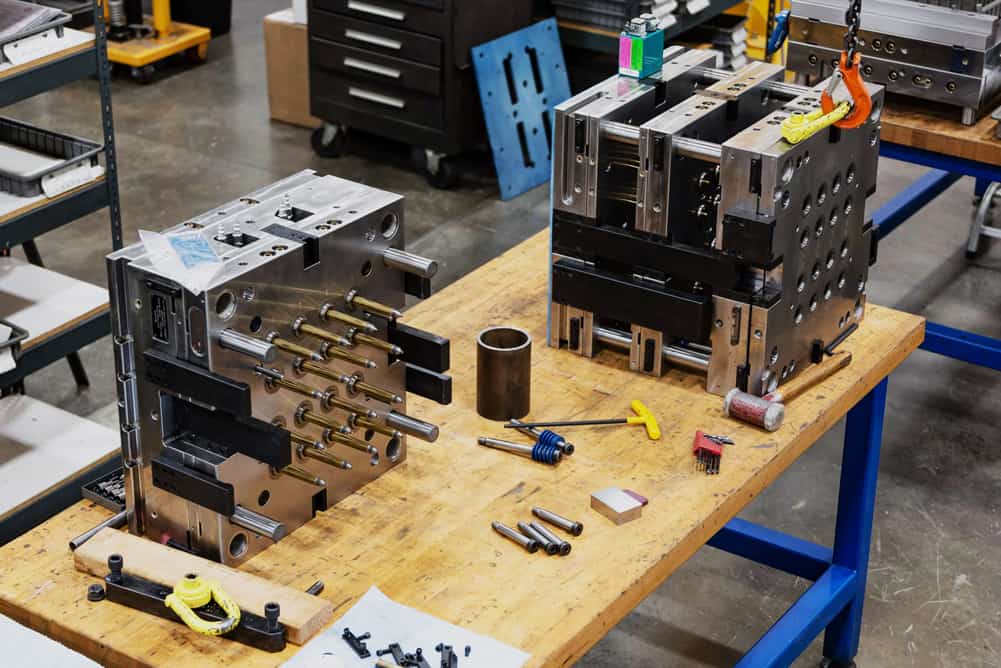
真空注型能力
标准精度
標準公差は±0.15 mm/100 mmで、最高精度は±0.05 mmに達することができる。
最大真空注型部品
真空設備は最大2.0 M*1.2 M*1.0 Mの金型仕様を収容できる。
最小肉厚部品
最小肉厚は0.5 mm、最適には1.5 mm~2.5 mmに設定して、部品公差を確保します。
シリコン金型寿命
基本的な数は、各金型では20〜25個コピーできる。プラスチック部品に複雑な構造などの高品質が必要な場合、通常は1つの金型で10個から15個のコピーができます。
標準納品時間
金型の複雑さと必要な部品の数によって、通常は7~10日以内に最大50個のプラスチック部品を製造することができます。
表面テクスチャとその他のオプション
真空成形は射出成形と類似しており、部品の表面には着色、テクスチャ化、塗装、コーティング、透明研磨、インサート、被覆成形ができる。
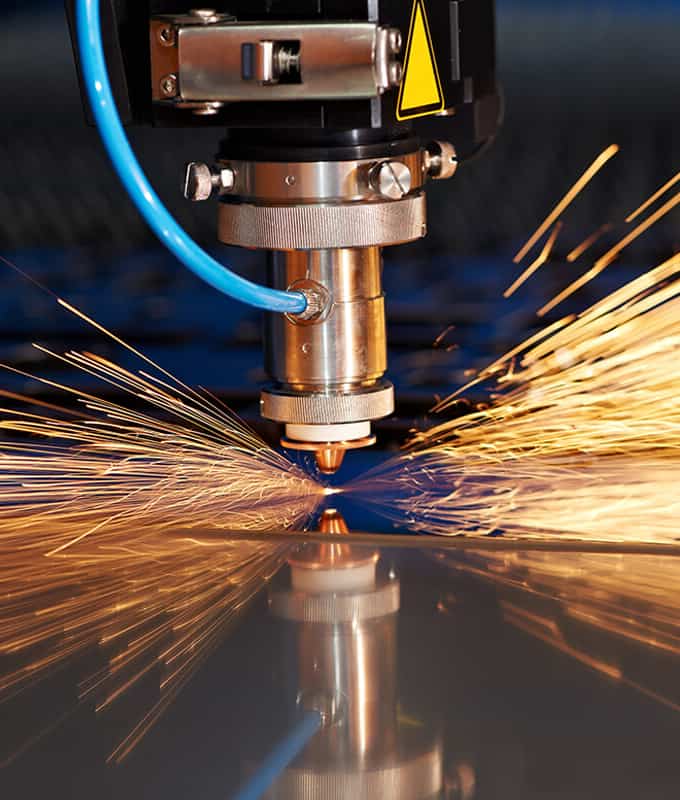
板金製造規格
エッジからエッジ、片面
+/- 0.127 mm
+/- 0.005 in.
エッジから穴、片面
+/- 0.127 mm
+/- 0.005 in.
穴ペア穴、片面
+/- 0.127 mm
+/- 0.005 in.
ベンドからエッジ/穴、片面
+/- 0.254 mm
+/- 0.010 in.
エッジからフィーチャー、マルチサーフェス
+/- 0.762 mm
+/- 0.030 in.
オーバフォーム部品、多数面
+/- 0.762 mm
+/- 0.030 in.
3 Dプリント製造規格
3 Dプリントサービスは、機能的で複雑なプラスチックや金属の高速成形に最適なソリューションです。FDM、SLA、SLSなど、最先端の3 Dプリント技術を提供しています。
- SLA: 最大サイズ 250*250*250 mm, Tolerance ± 0.2 mm
- SLS: 最大サイズ 420*500*420 mm, Tolerance ± 0.15 mm
- FDM: 最大サイズ 500 * 500 * 500 mm, Tolerance ± 0.2 mm
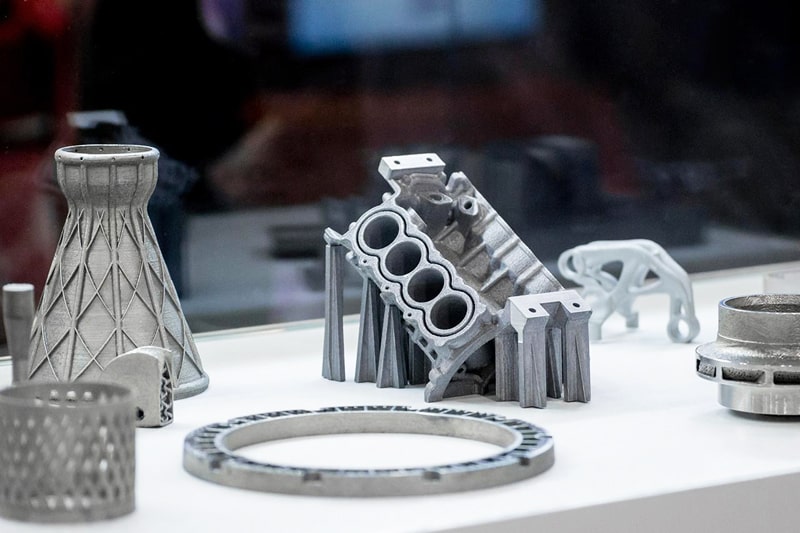
お客様ご要望のカスタム製造
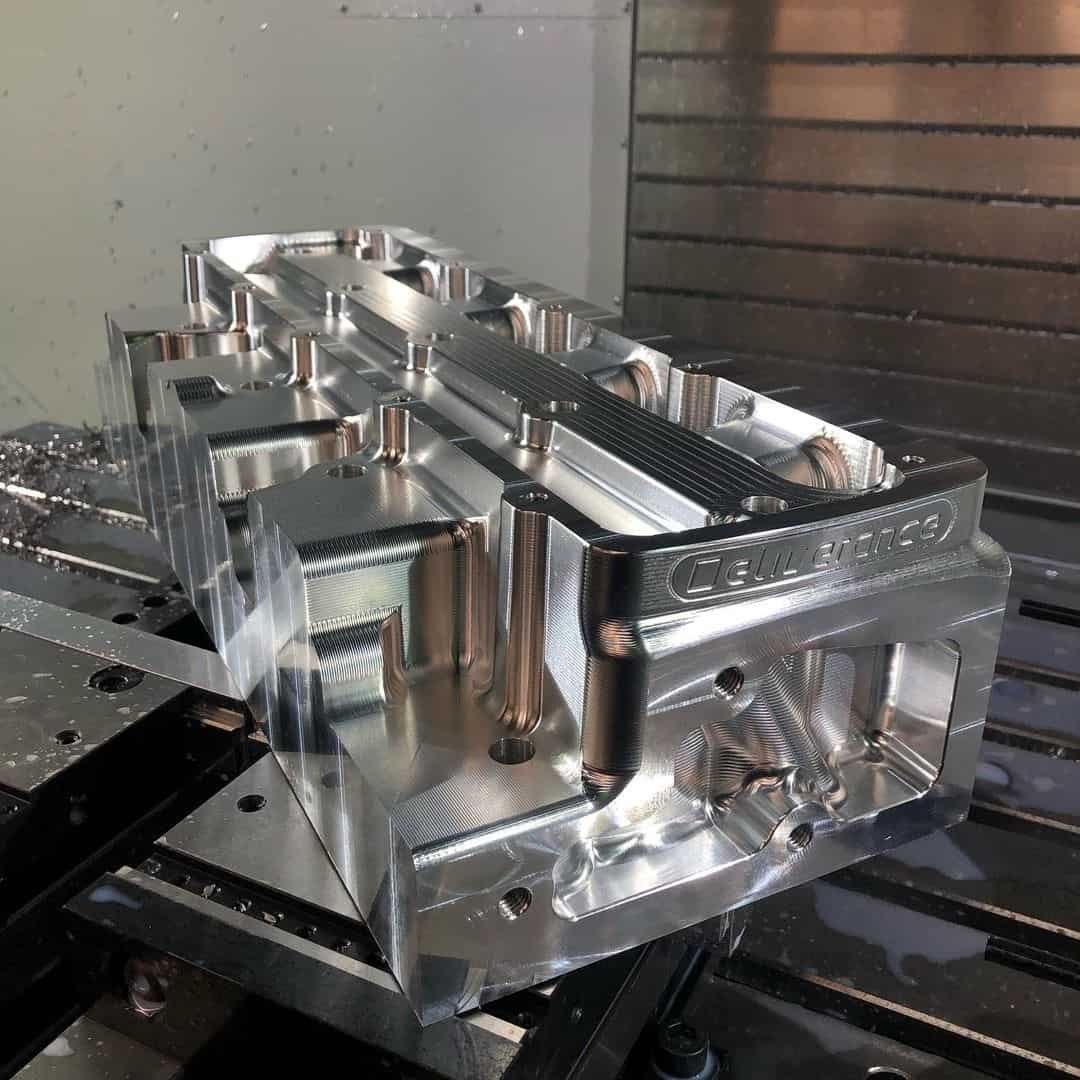
高速プロトタイプ作成サービス
最新のテクノロジーと設備を使用してプロトタイプを迅速かつ正確に製造することで、開発時間とコストを削減できます。
能力: 1-50
納品時間: 7稼働日以内
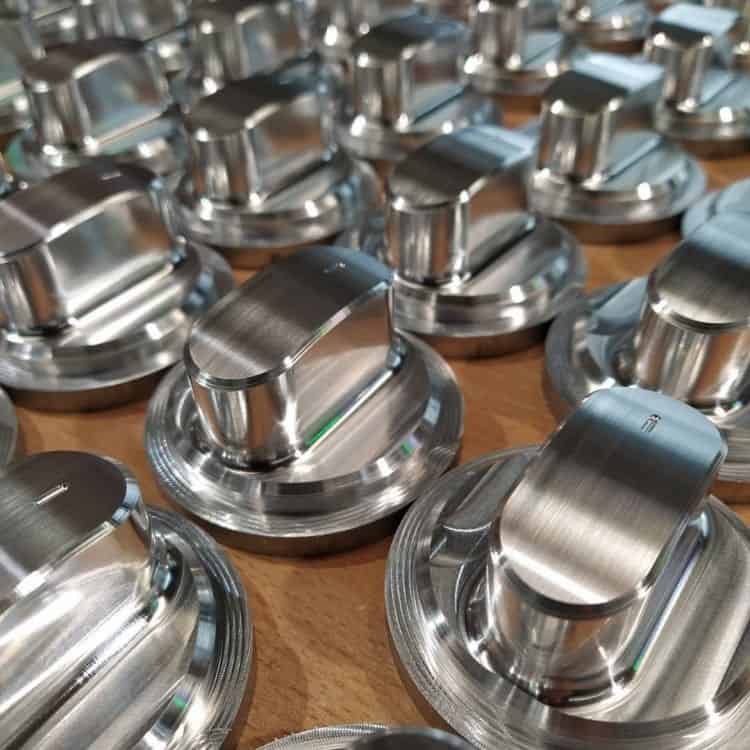
小ロット生産
小ロット生産には、真空注型、NC加工、高速金型など各プロセスオプションがあります。
能力: 50-2000
納品時間: 15稼働日以内
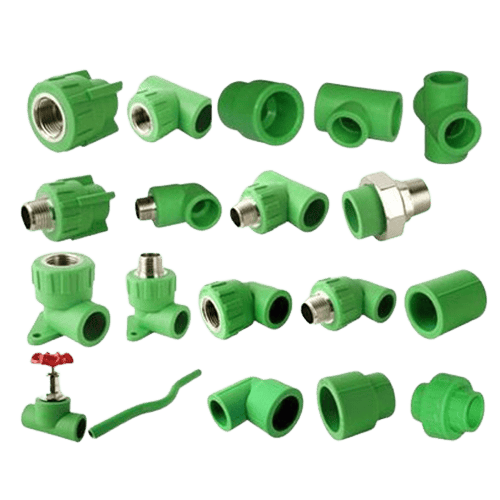
量産
カスタム部品の大量製造には、プラスチック射出成形、板金製造、その他の製造プロセスを使用しています。
能力: 1000+
納品時間: 25稼働日以内
全面的な表面処理サービス
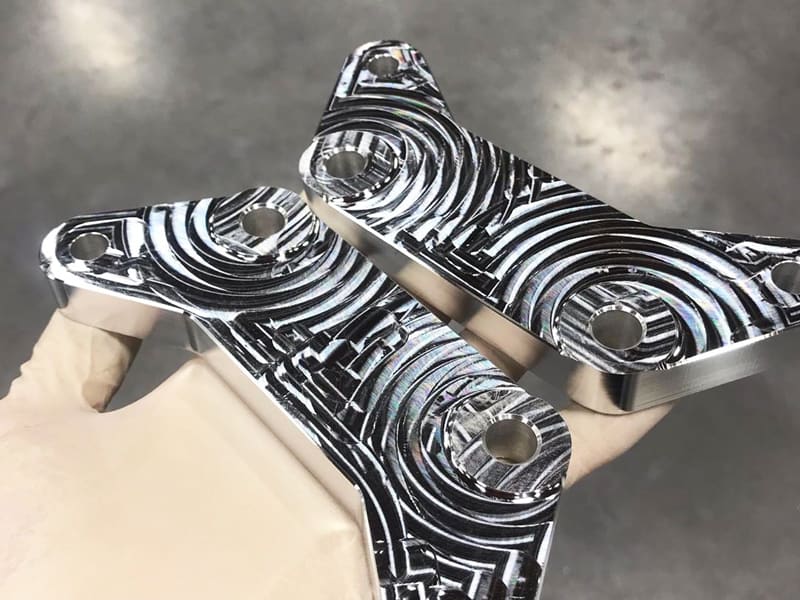
機械加工
標準の「機械加工」部品の表面粗さは3.2µmで、鋭いエッジとバリ取り部品をきれいに除去することができます。平滑加工の表面粗さはRa 1.6〜0.8μm、超仕上げ加工の表面粗さはRa 0.8〜0.2μmであります。
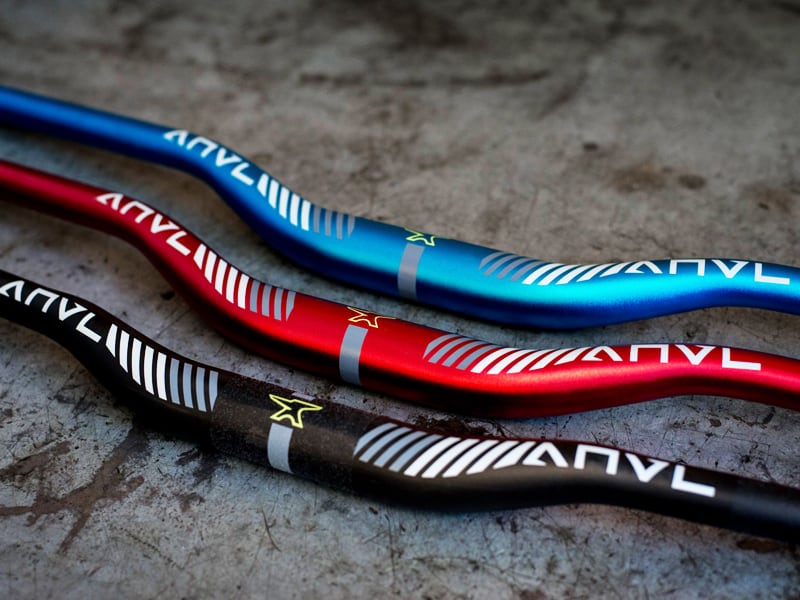
アルマイト
アルマイトは耐食性、耐摩耗性、絶縁性の特徴があり、部品の性能を長時間維持することができる。アルマイトは一般的にアルミニウム合金部品に用いられ、美学的効果を達成する。すべてのiPhone製品はアルミニウム処理されています。
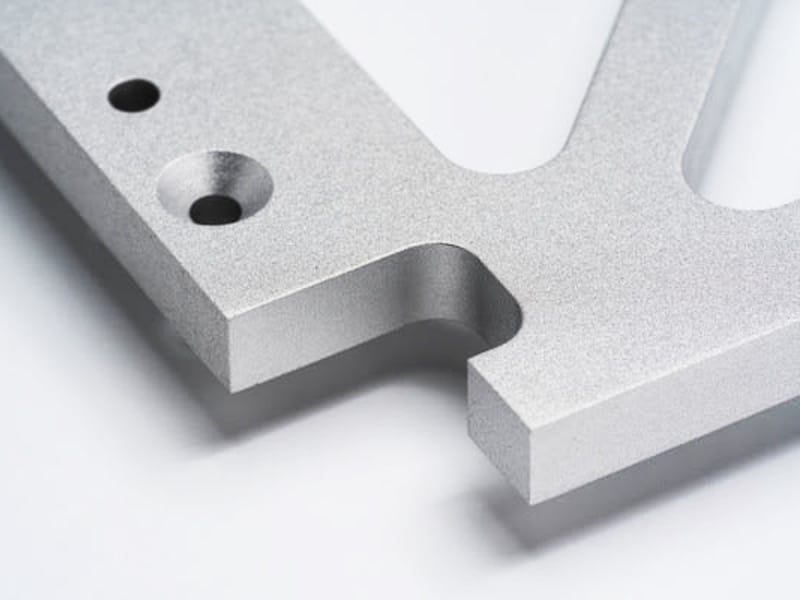
粉末コーティング
粉末コーディングは、コロナ放電現象を利用して部品表面に薄い保護ポリマーを付けることで、厚みは約50μmから150μmである。より耐摩耗層になって頑丈で耐摩耗性のある表面が作成されます。
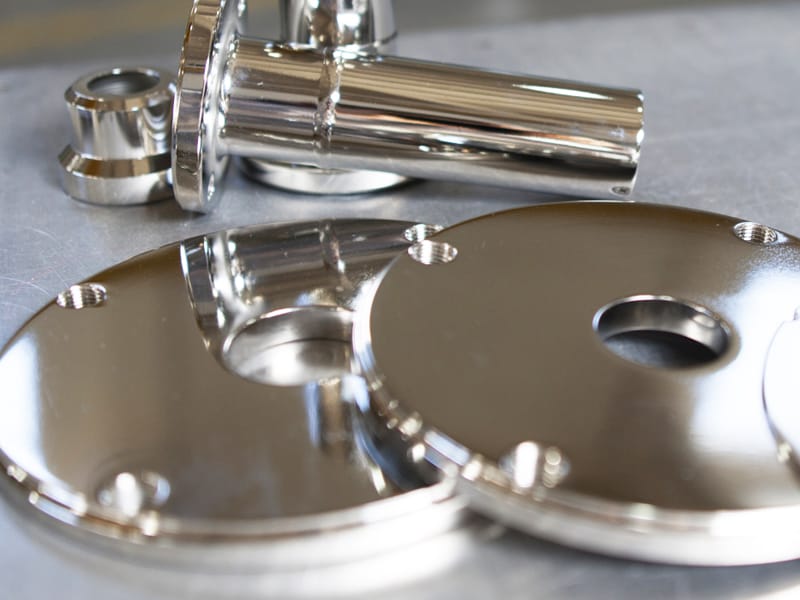
メッキ
めっきは精密加工プロセスであり、合金、カドミウム、クロム、複合材料、金、ニッケル、ロジウム、銀、錫、亜鉛、亜鉛ニッケルなどの金属を導電性表面上に沈積する方法です。
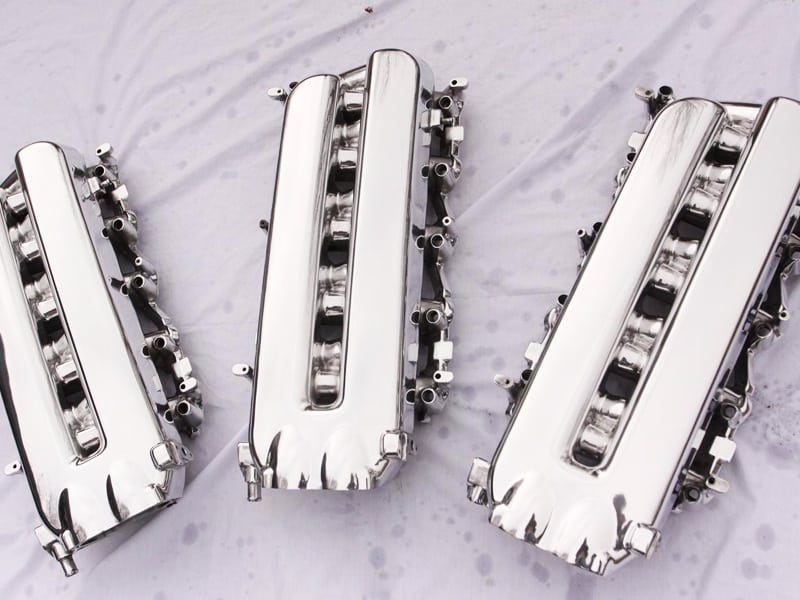
ミラ研磨
ミラ研磨は粗い研磨紙からプロトタイプに光沢やミラ面的な外観を持たせる2000粒度レベルまで研磨効果を徐々に増加する方法。例としては、透明な自動車ライトガイド、ヘッドライト、リアテールランプがあります。原プロトタイプの表面は十分に滑らかになります。
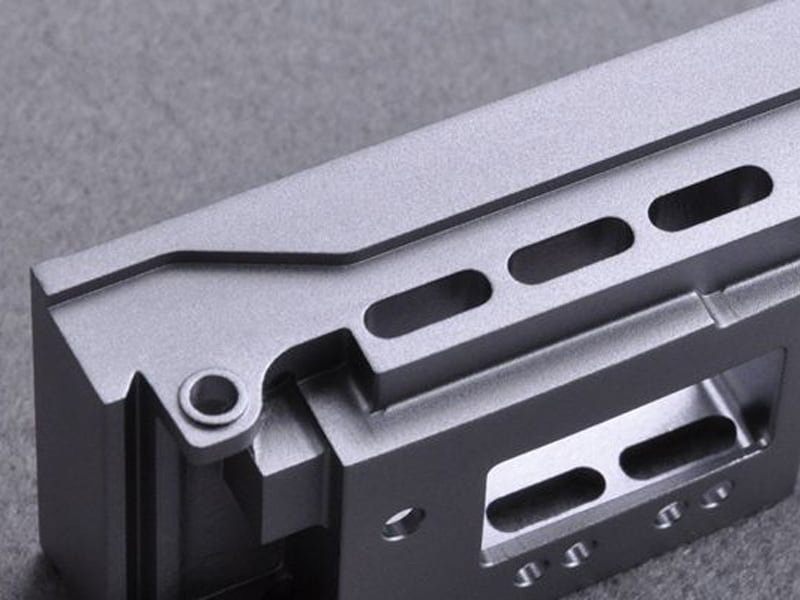
サンドブラスト
サンドブラストとは、細かい粉砕ガラスビーズ粒子が高圧下でプロトタイプ表面に衝撃を与える。CNCプロトタイプの表面に粒子状の凹みを生じらて、それによって艶出しまたは侵食表面が作られます、艶出し表面の仕上げ度をもたらします。ガラスビーズのサイズは、#80から#220までの範囲です。
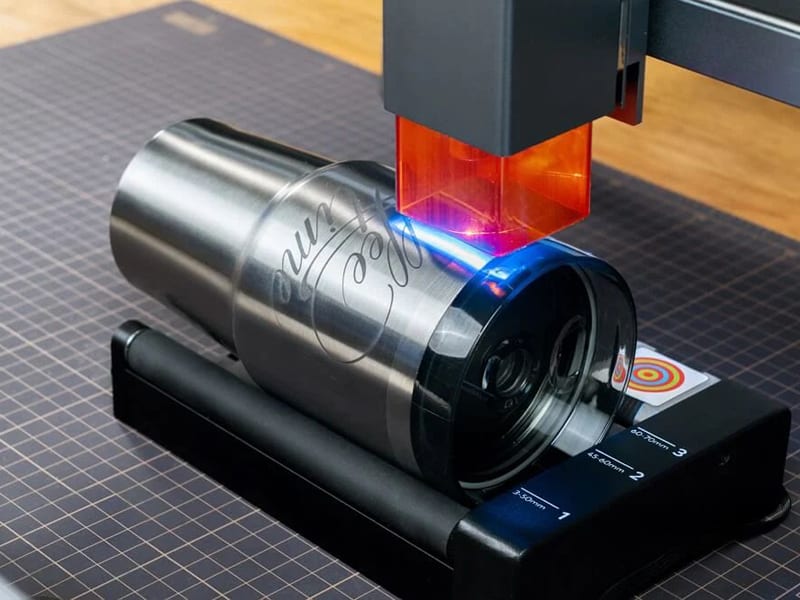
レーザーエッチング
レーザエッチングは、特性的または美的価値のある永続的なマーキングを作成するために材料の表面を変更するプロセスである。レーザーエッチングに最も一般的に使用される金属材料としては、アルミニウム、ステンレス鋼、亜鉛が挙げられ、その他の非金属材料としては、ガラス、ポリマー、セラミックスが挙げられます。
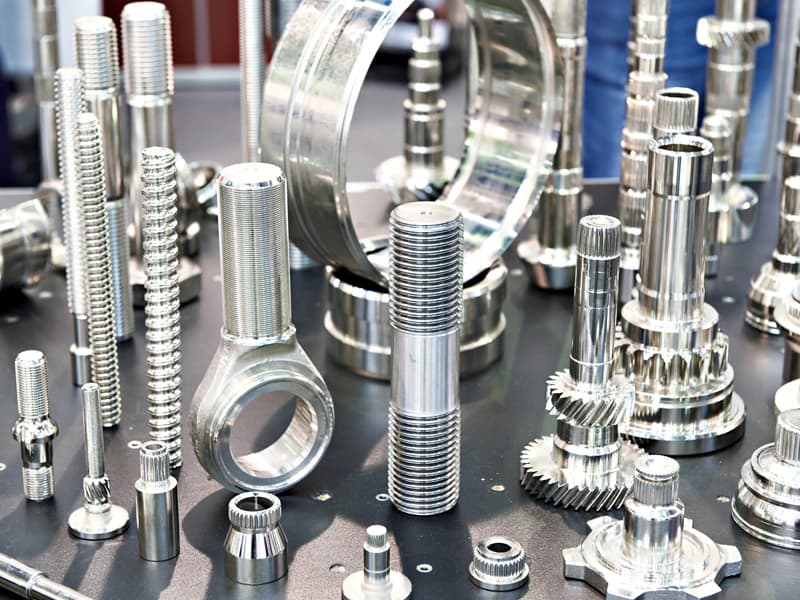
クロメート
クロメートは、金属表面を酸化しにくい状態に変換し、金属腐食速度を遅らせる方法である。クロメートの過程でよく使われる材料はステンレス鋼であり、その耐食性をさらに高めます。
品質検査報告書
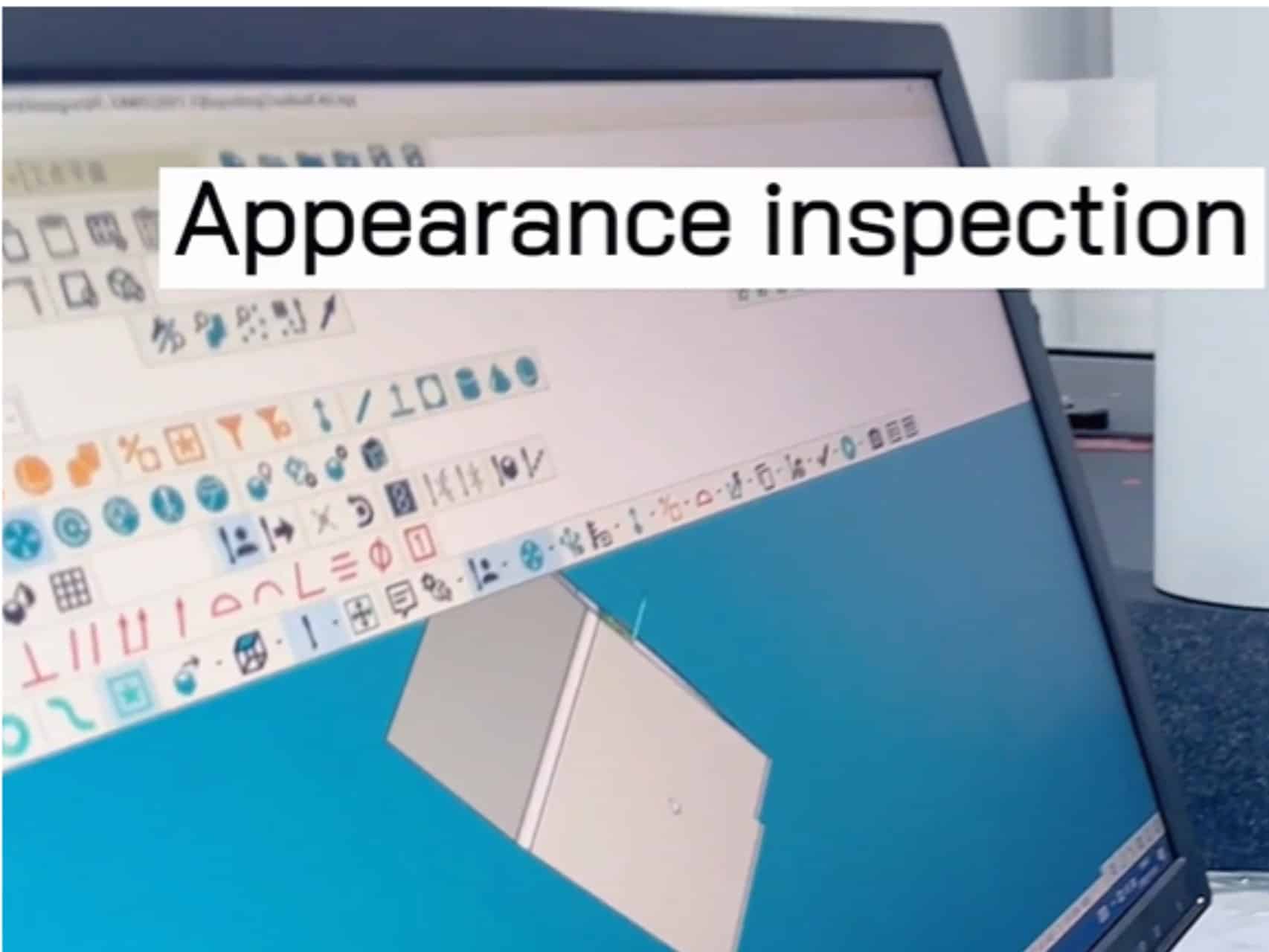
外観品質検査
まず、カスタム部品は、色、品質、その他の物理的属性などの外観要求に合っているかどうかを確認します。
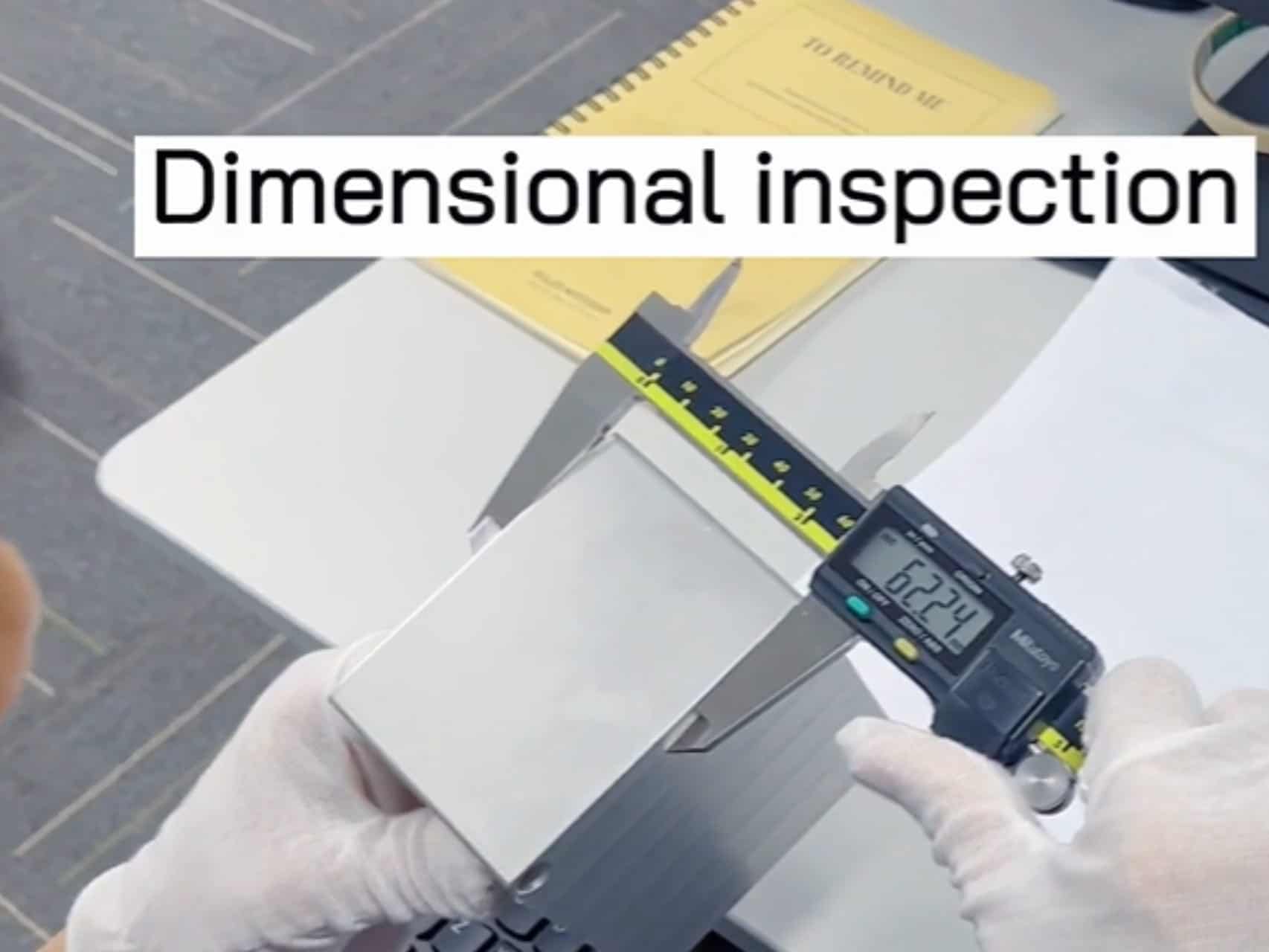
寸法検査
複雑な物体には、それらの寸法を正確に測定するために3座標測定機が必要です。
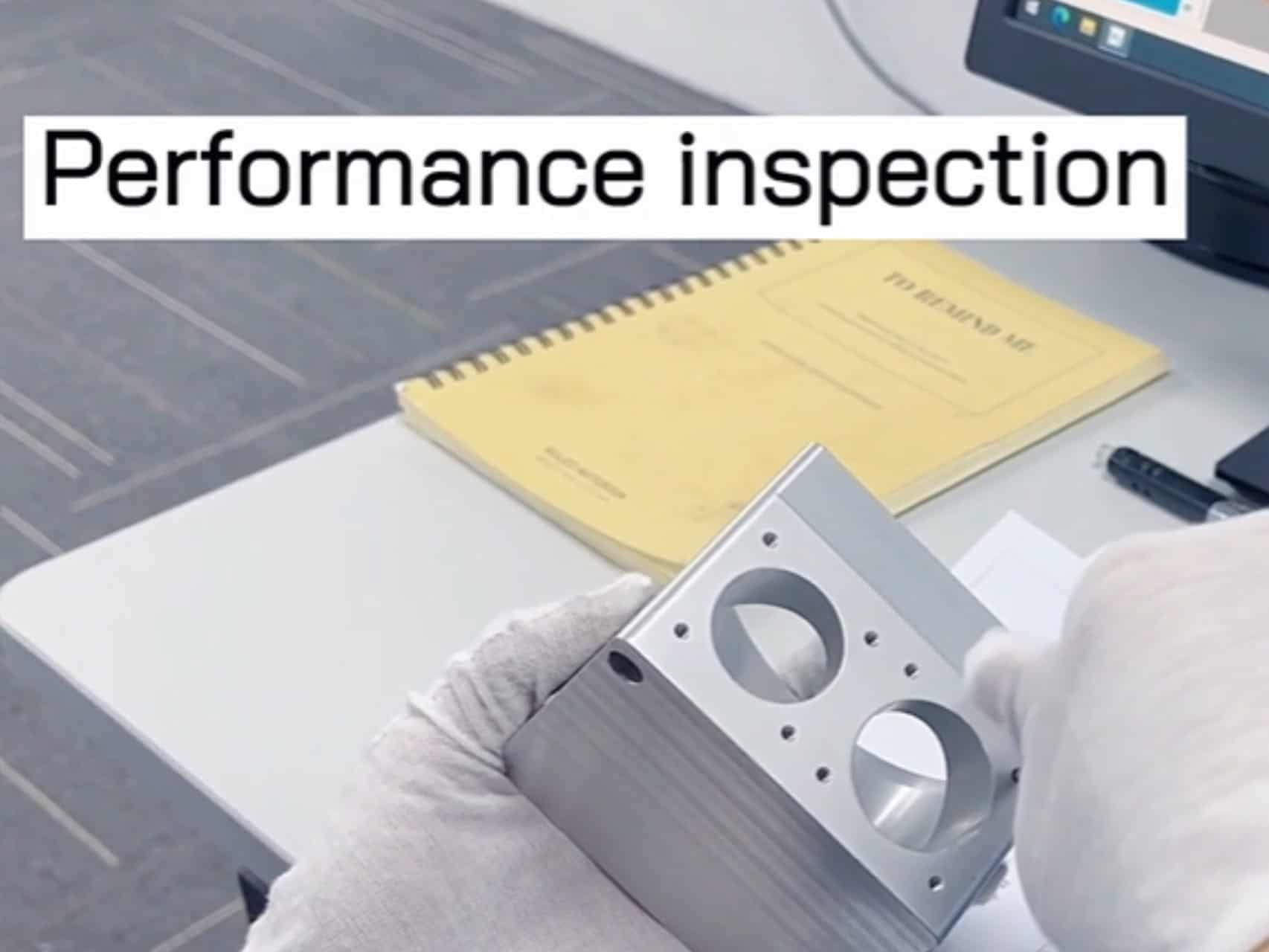
性能検査
部品の機能と性能が検査範囲で、部品にドリル穴やねじ穴があれば、組み立て要求に合っているかの検査を行います。
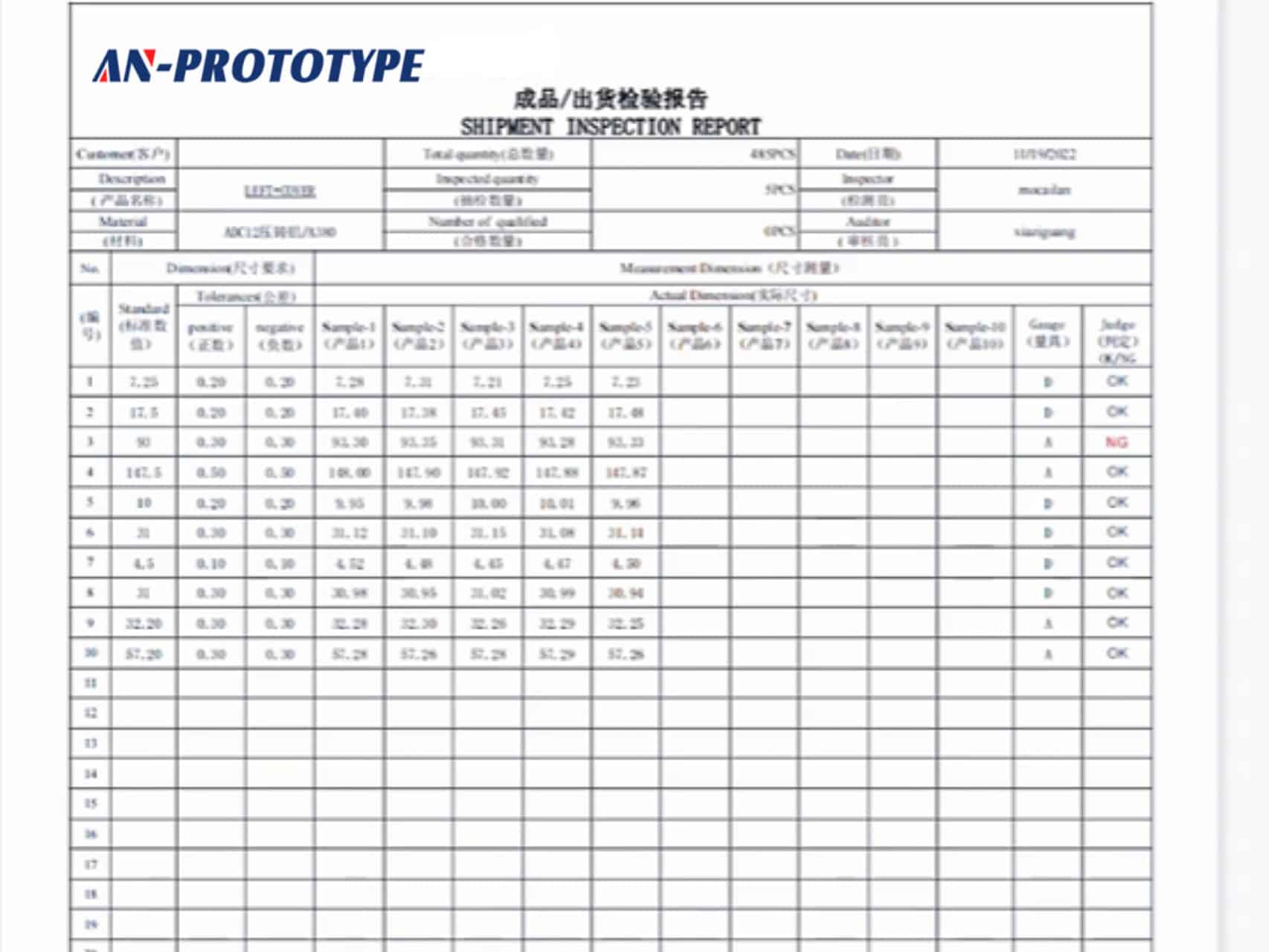
初品検査
検査プロセスの最終段階では、最終的な検査報告書を提供します。報告書にはすべての検査機器と検査データを表示します。
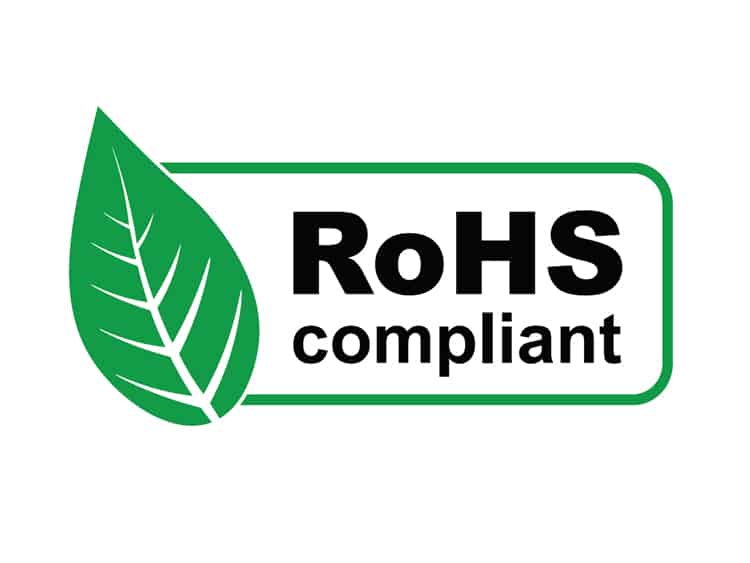
材料認証
特定の材料または製品がRoHS指標に適合していることを検査して、お客様の要求によって、お客様の要求によって、RoHSレポートを提供加可能です。
お客様の評価
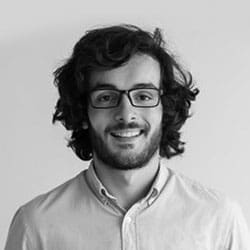
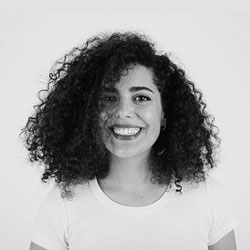
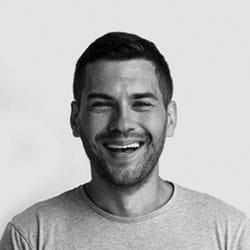