表面処理技術
高い品質レベルの表面処理方法は、部品の見た目性と機能を高めるだけでなく、プロトタイプや想像の一部を形にすることもできる。
- ISO 9001:2015, ISO 13485 証明書
- 160種類以上材料ミルシート
- 24/7エンジニアリングサポート
- 100%品質保証
- グローバル配送
カスタム部品の表面処理方法
AN-Prototypeは優れた仕上げ技術を持って、プラスチック、複合材料、金属表面処理のプロであります。工場に最先端の機器と施設を備えており、お客様のアイデアを形にするサポートをしています。AN-Prototypeは、多様なニーズに対応するために一体化された部品仕上げ提案を提供しています。部品の色、質感、光沢、表面仕上げをお客様の期待以上確保ききます。部品仕上げについて、お気軽にご連絡ください。下記は、表面処理サービスの詳細です。
AN−Prototypeの仕上げ加工方法には、手作業加工、研磨、サンドブラスト、バフ仕上げ、塗装とスクリーン印刷、レーザーエッチング、アルマイト、黒な染め、粉末塗装、金属めっき、真空メッキ、クロム化、化学表面処理、クロメート、熱処理などが含まれます。
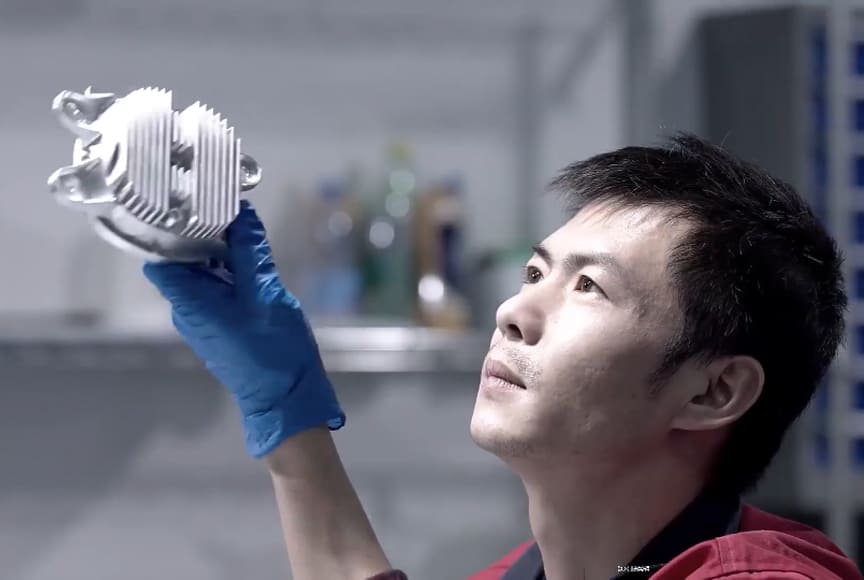
AN-Prototypeの表面処理方法
研磨とバフ仕上げ
バフ仕上げは、通常のプラスチック、金属部品及び透明アクリル酸及びポリカーボネート部品を鏡面処理して、正確で均一な平面及び専門レベルの光沢を実現できる、透明部品の光学的鮮明度を高めるため使用される方法です。
機械加工表面処理
手作業仕上げ
サンドブラスト
ビーズには、#80から#220まで異なるサイズがあります。
塗装
ペイント仕上げ
性能的コーティング
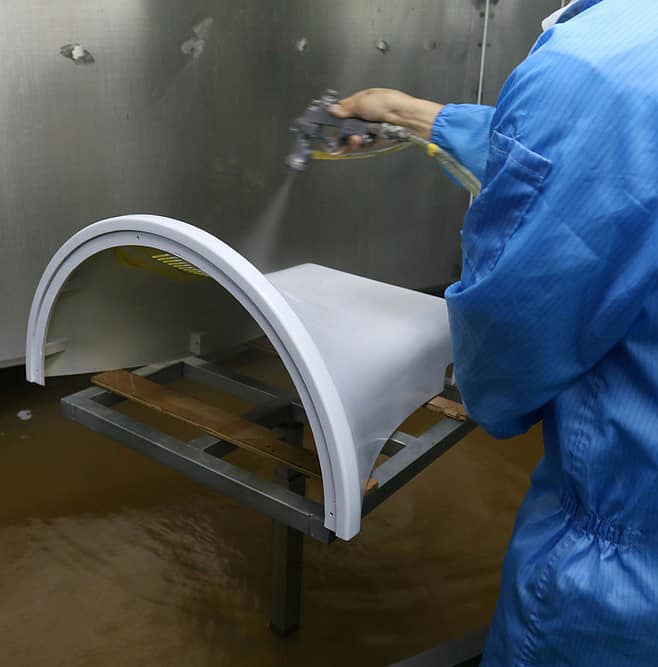
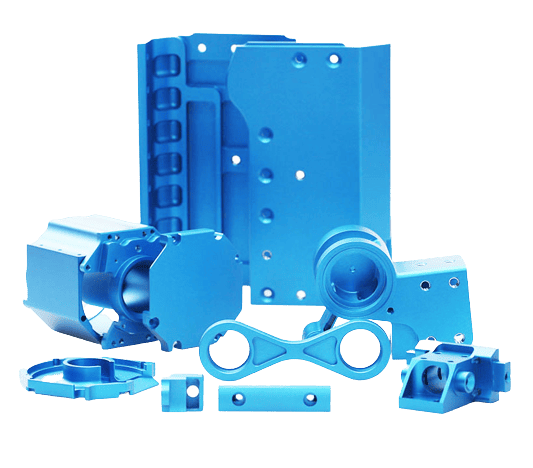
アルマイト
II型アルマイトは、主に均一で綺麗な表面を持つ部品の生産に使用されて、非常な耐食性と限られた耐摩耗性を持って、多種の色染料が選択できる。代表的なコーティング厚さ:ブラック12〜18μm、透明8〜12μm、カラー4〜8μm。
III型アルマイトは、硬質アルマイトとも呼ばれ、優れた耐食性と耐摩耗性があり、機能的な応用に適用されていますが、色はより限定されており、通常は透明または黒色のみである。代表的な厚さは30〜125μmである。
真空金属コーディング
メッキ
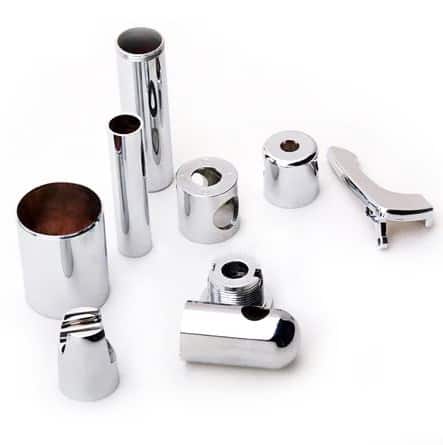
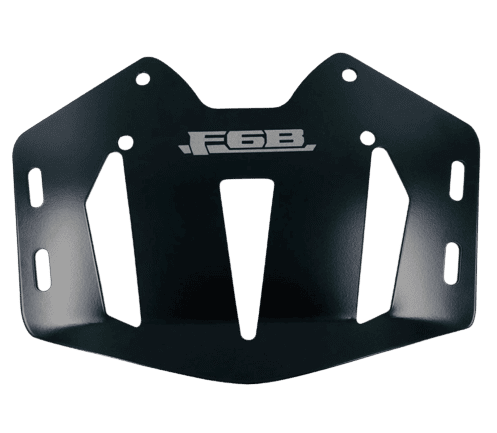
パウダーコーティング
プリンティングとエッチング
Powder coating adds a thin layer of protective polymer to the surface of a part. It uses the phenomenon of corona discharge to cause the powder coating to adhere to the workpiece, resulting in a strong, wear-resistant finish. Typical thicknesses vary from approximately 50 μm to 150 μm.
黒な染め
表面仕上げ部品写真
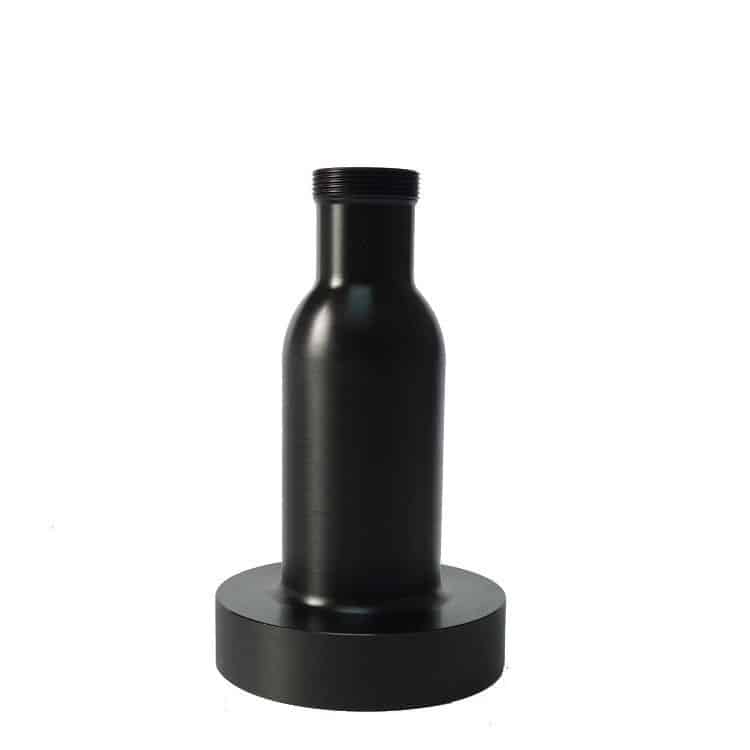
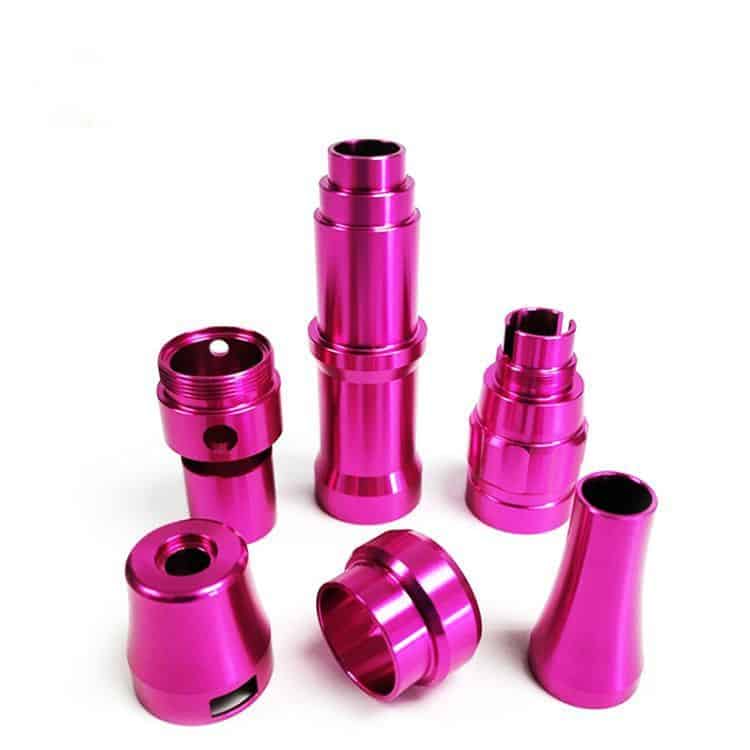
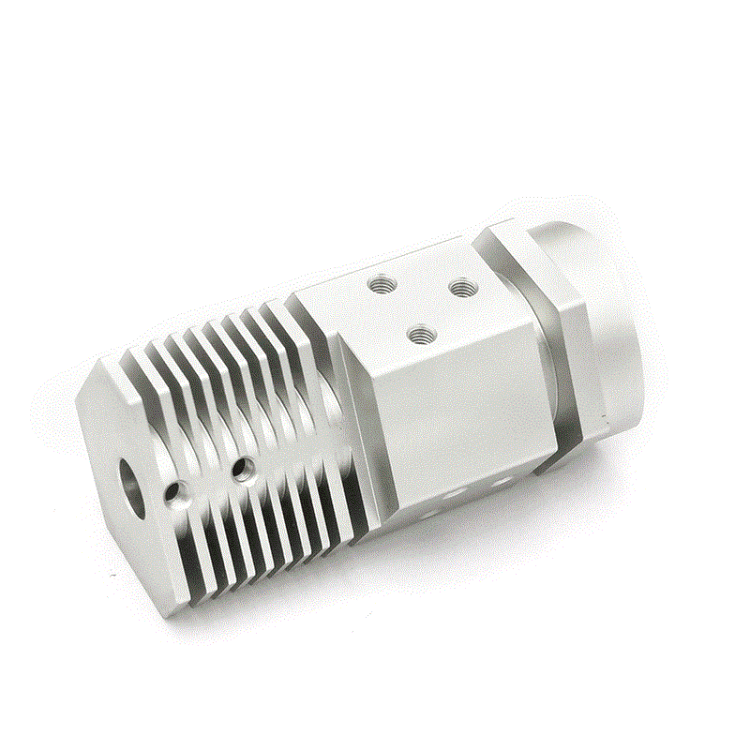
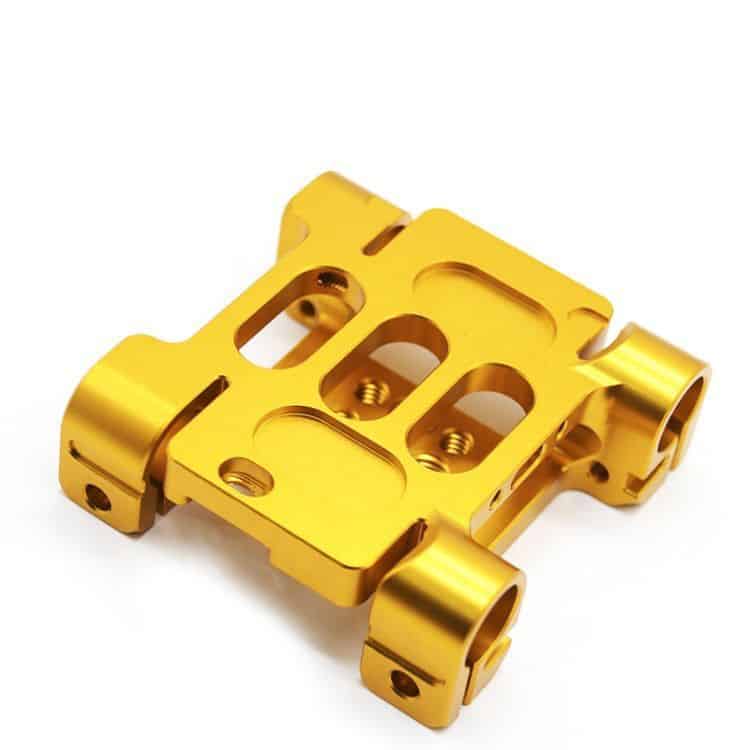
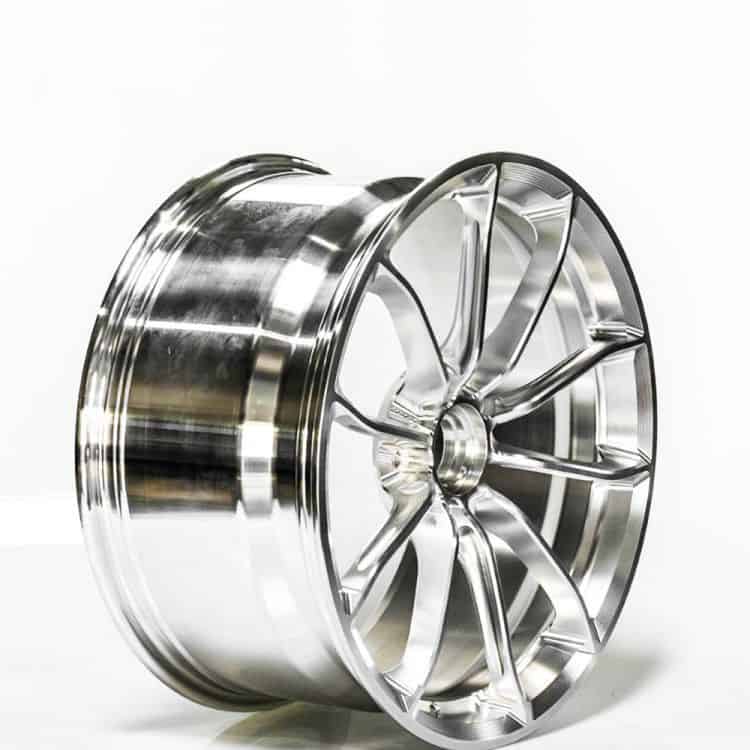
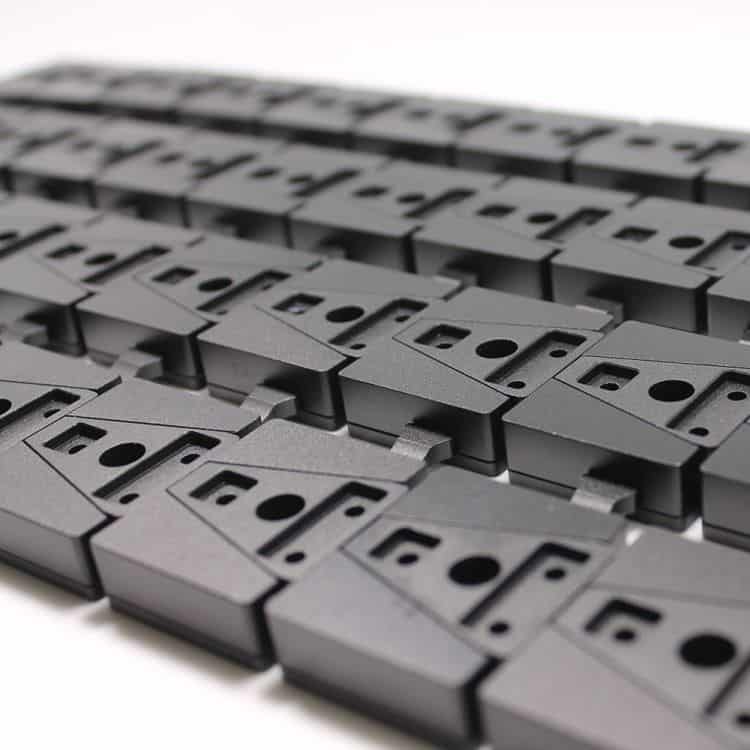
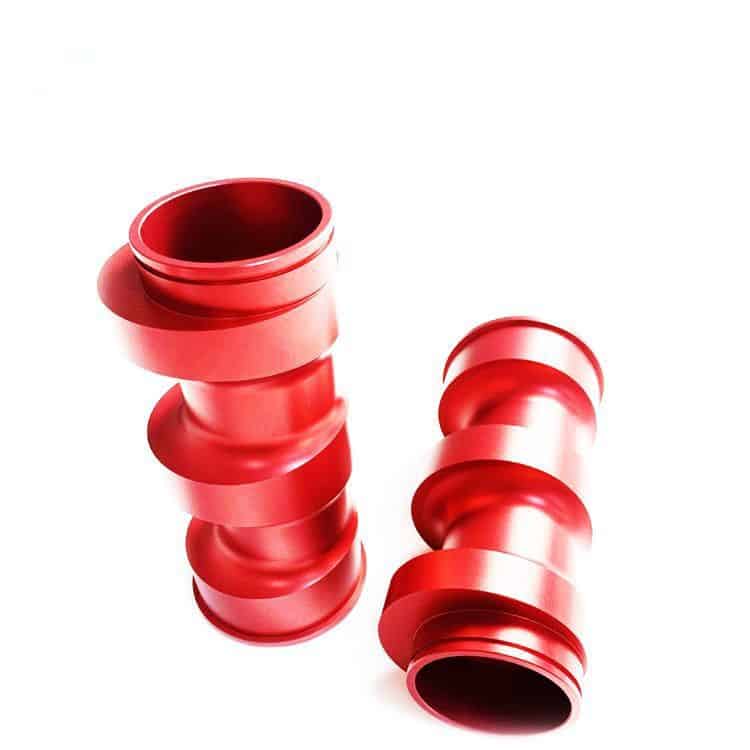
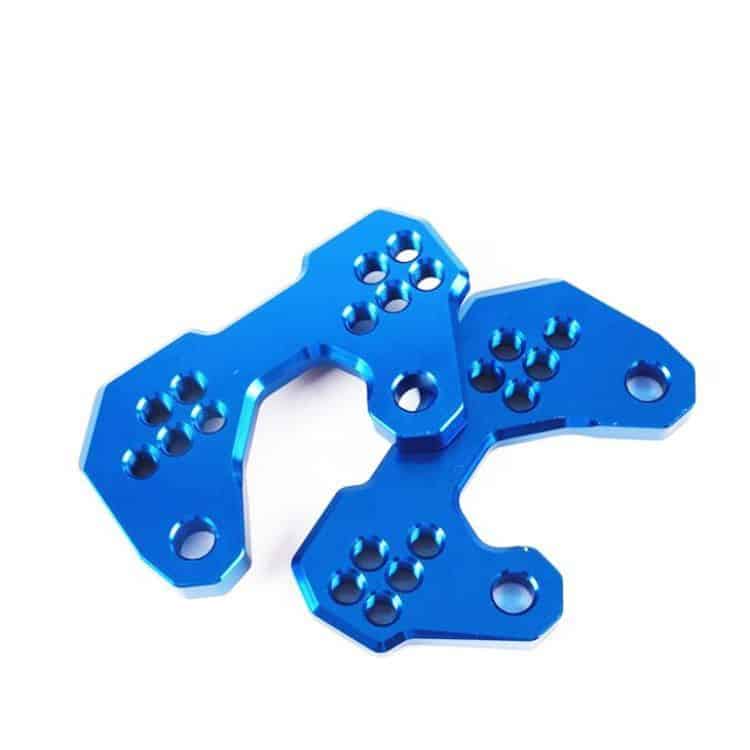
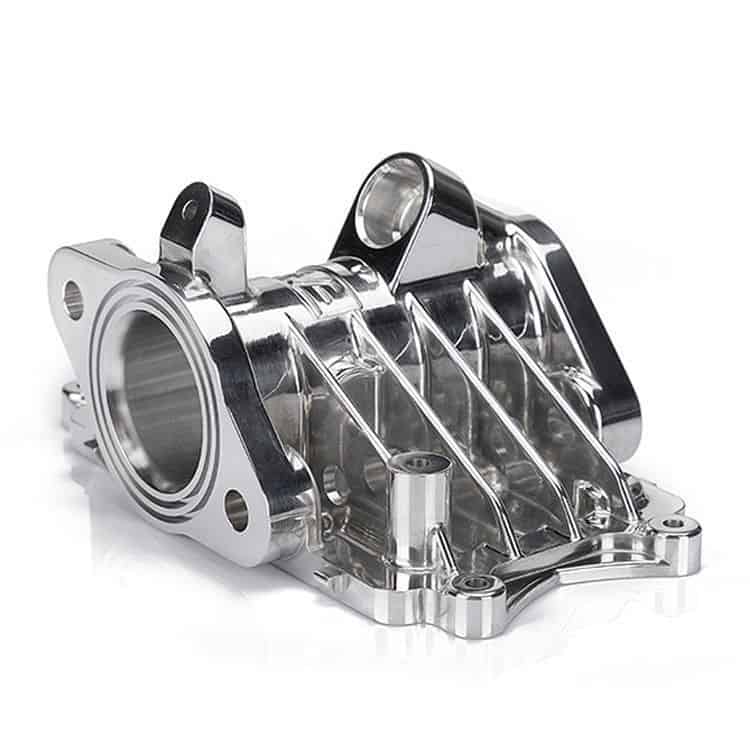
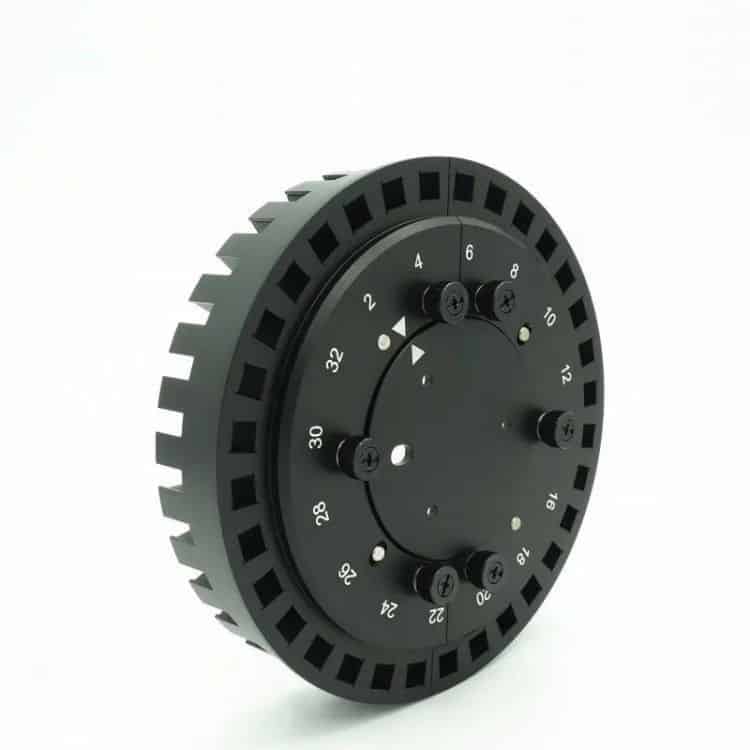
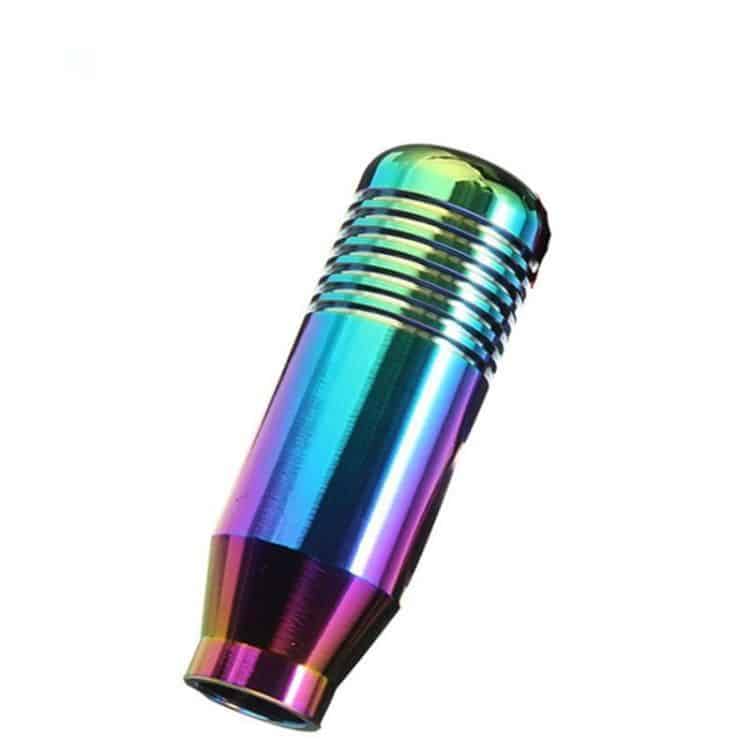
お客様からの評価
「私がAN-Prototypeと協力した経験は素晴らしいです。彼らのコミュニケーションは非常に優れており、Michinはいつも私の質問に答えることができます。私たちが受け取った完成品は予想通りの最高品質を持っています。本当に存在するのは、私がいつもMitchinから得ている良質なサービスです。彼はいつも私たちの満足を確保することに力を入れている。総合的には、信頼できるベンダーを探している人にAN-PrototypeとMichinを強く推薦します。
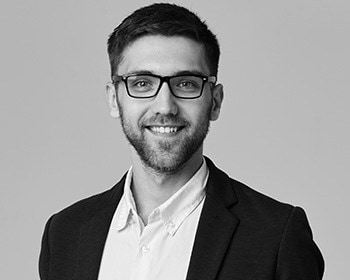
「複雑な5軸CNC加工部品であっても、AN-Prototypeからは非常に良い結果が得られました。過去2年間、AN-Prototypeと共に多くのプロジェクトを手掛けてきましたが、彼らは常に非常に優れた品質(彼からCNC加工サービスとアルマイト処理を薦めてもらったこともできます)、信頼性、非常に迅速で完璧なコミュニケーションを提供してくれました。DavideとVivianとの協力に感謝し、すでに多くのパートナーに紹介しました。

「私のAN-Prototypeに対する体験はとても特別です。最初から通信は正確で迅速であり、難しい設計に対しても、ソリューションを提供します。プロトタイプ制作の価格は競争力があります。最終製品のQCも非常に優れています。続けて加工部品を依頼します。
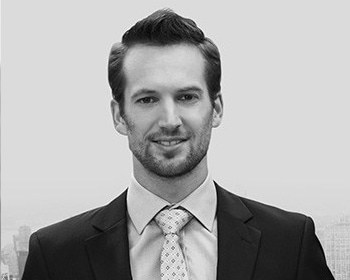