CNC 旋削加工サービス
AN-Prototype CNC旋削加工は社内の一つの加工作業として、迅速な輸送手配、最も厳しい公差制御と競争力のある価格でお客様に信頼されています。
- ISO 9001:2015, ISO 13485 認証.
- 160+種類素材認証
- 公差 ± 0.005mmまで
- 100% 品質保証.
- グローバル配送
CNC 旋削加工プロセス 公差 ±0.001mm まで
AN-Prototypeは、お客様新製品開発者に最も親切な精密CNC旋削サービスを提供することに力を入れています。私たちの旋削作業工場は、CNC旋盤、アメリカ及び日本から輸入した切削工具を使用しています。CNC旋削センターは、複雑・重要なサイズ高品質要求のカスタム金属部品またはプラスチック部品を製造できます。クイックプロトタイプ作成または小ロット生産には適用な加工工芸になります。
CNC旋削とは
CNC旋削は、CNC旋盤上の工具は沿道経路によって、回転しているワークから材料を除去するプロセスである。簡単に言えば、このプロセスに関連する主要な要素は、ワークをクランプする回転主軸と、カッタータワーに取り付けている切削工具である。CNCフラストと異なり、CNC旋削工芸では、切削工具自身が回転しないです。
CNC旋盤が微細切削工具を使用する場合、旋削部品の表面仕上げは非常に綺麗にできて、後処理は必要ありません。旋削加工は、雌ねじ山と雄ねじやめ、溝、テーパ、リング状溝、および基本的な円形断面及び多くの特徴を作るためのただ一つの実用的な加工方法です。
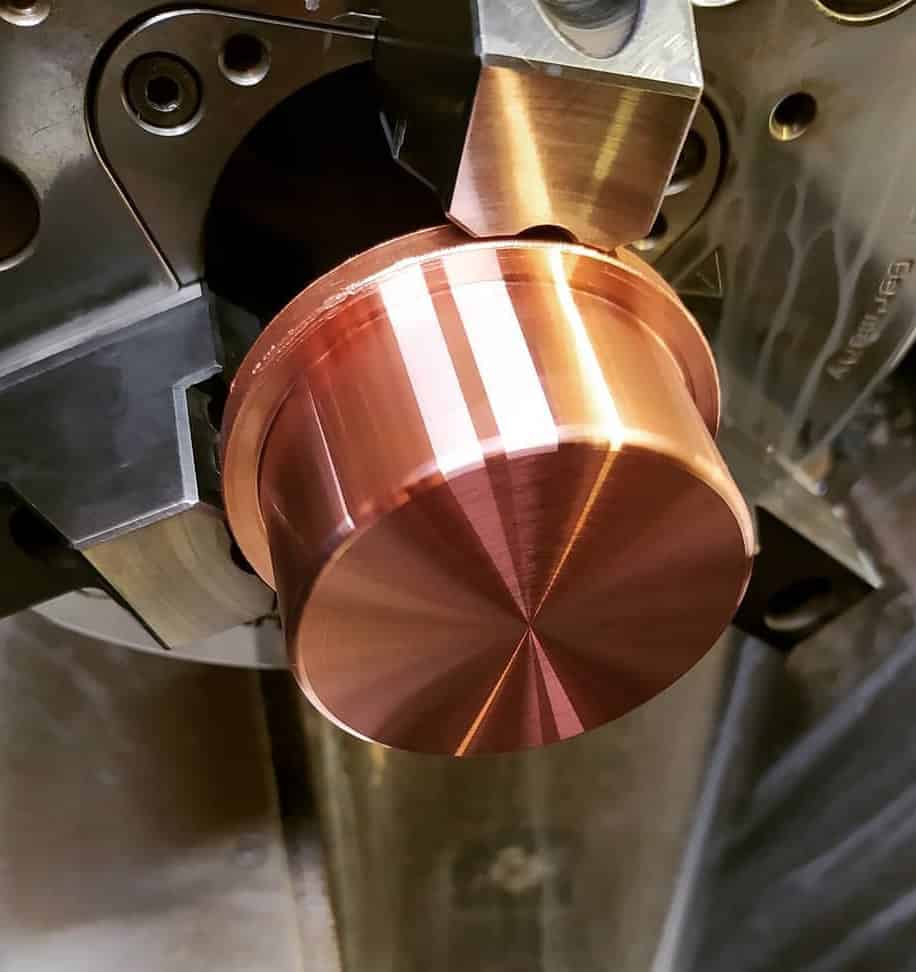
CNC旋削加工を選ぶ理由?
- すべて円角表面の部品に適用
CNC旋削工芸は、円形または円筒形の部品を製造するための理想的なプロセスです。CNC旋盤はこれらの部品を迅速かつ正確に製造することができ、優れた再現性があります。
- 自動化され、コスト効果を持っている
CNC旋盤は自動化と拡張性が高くて、CNC旋削は最低なコストで小ロットと大ロットの生産に適応できます。
- CNCフライス盤はより良い加工能力を持っている
多軸CNC旋削センターと旋削の複合旋盤により、1台の工作機械上で複数の作業と複数ステップの加工作業を実行でき、経済的・効率的な方法で複雑な幾何形状を加工できます。
AN-Prototypeの高精度なCNC旋削サービス
AN-Prototypeは、航空宇宙、消費製品、自動車、医療製品、電子部品、スポーツ用品及び多く工業のお客様に高精度CNC旋削サービスを提供している。私たちのCNC旋削工芸では、切断、端面、ねじ加工、成形、ドリル、ローレット、引抜き、ボーリング加工方法があります。溶接、バレル詰め、研磨、サンドブラスト、クロメート、熱処理、 メッキ及び組立など一連の付加価値サービスは、私たちの旋削能力をもっと改善しています。
- 自動化・低コスト・高効率
- 付加価値サービス
私たちのCNC旋削工芸では、切断、端面、ねじ加工、成形、ドリル、ローレット、引抜き、ボーリング加工方法があります。溶接、バレル詰め、研磨、サンドブラスト、クロメート、熱処理、 メッキ及び組立など一連の付加価値サービスは、私たちの旋削加工能力をもっと改善しています。
- 専門的な技術チーム
AN-Prototypeは、専門的なCNCエンジニアと技術者により、最先端のCNC旋削技術で、どんな複雑な構造や難しい形状の製品でも、お客様の要求より高い精度、正確性、品質基準で製品を提供しています。
- お客様へ熱心なサポート
AN-Prototype、CNC旋削作業を絶えず改善し、新しい業界技術を採用することによって、すべてのお客様の独自のニーズを十分に満たすことに力を入れています。お客様が安心して部品加工の依頼できるパートナーになります。
CNC 旋削加工範囲
旋削以外にも、NC旋盤はさまざまな追加作業を実行することができます。回転面、外円旋削、内円旋削、テーパ旋削、切断、端面、ボーリング、ヒンジ穴、ドリル、ローレット、ねじ加工、溝切りなど加工も対応可能です。
- 外径と内径旋削は、精密な円筒状特徴のCNC加工であり、CNC旋削部品をさらに加工続けることができ、目で見える工具跡が付く(使う工具:汎用旋削工具)
- 切断と溝切りは、部品の内部または外部の溝プロファイルを切断または切断するために使用する加工方法(使う工具:切断とノッチブレード)
- 端面加工は、ワークの表面を平らにする(使う工具:端面ツール)ボーリングとヒンジ加工は、既存の穴を拡大または仕上げて高精度の直径を加工できる加工(使うツール:ボーリングとヒンジ穴ツール)
- ドリル加工は、材料を除去してワーク内部から高精度の直径穴を加工する(使う工具:ドリル)。
- ねじ山加工は、旋削でネジ山加工する、ワークの内部または外部領域で行う加工作業(使う工具:ねじツール)
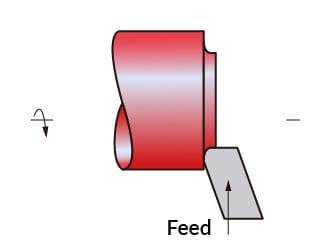
フェースミリング
先端工具は、回転ワックの外面を回転軸と平行な方向で線形に削って、円筒体にねじが形成されます。
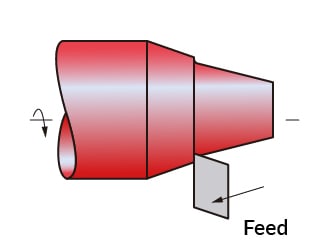
テーパ旋削
テーパ旋削はテーパ軸を製造する最も経済的な方法である。 工具の外周旋削中に、切削加工物の直径が徐々に変化する。
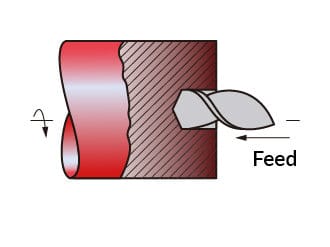
ドリリング
旋盤にドリルをその軸線に沿って回転ワークに送り込むことによってドリル穴をあける。ヒンジ加工は同じ方法で加工することができます。
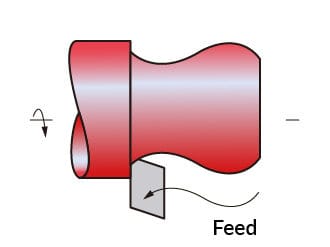
形状旋削
成形ツールは、ワークを半径方向に切断し、ワークに形状を付与することを成形とします。
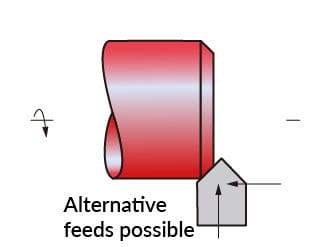
面取り
このツールは、部品のコーナーで角度をカットし、いわゆる「面取り」を作成します。
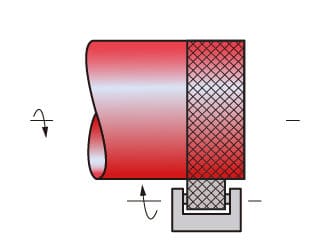
ローレット
専用ツールは、ワークの表面で動作し、ワークに規則的なクローズ形を作る工芸で、金属成形操作とします。
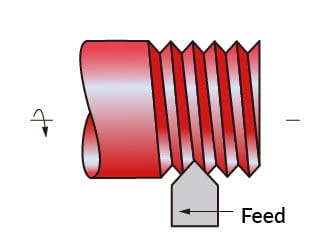
スレット
尖ったカッターは回転軸に平行な方向に回転ワークの外面リニアフィードして、円筒体にねじ山を形成すします。
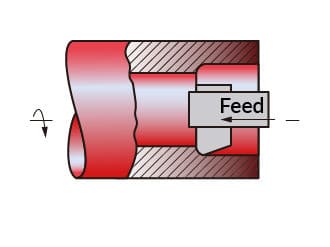
穴あけ
工具は回転軸に平行で、ワーク内部既存の穴径にリニアフィードすることで形成されます。
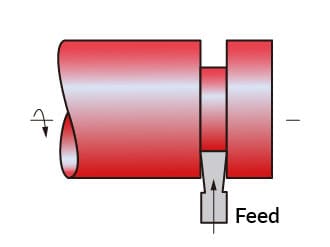
切断
工具はワークピースのある点に沿って回転ワークピースに半径方向に送り込まれ、部品の端まで切断されます。この操作は分解と呼ぶ時もあります。
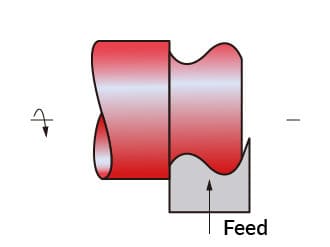
外形旋削
ツールを回転軸に平行な直線に沿って送ります。ツールは曲ラインのプロファイルフィードに従って送られて、旋削部品にプロファイル形状を加工します。
CNC旋盤加工能力
CNC 旋盤台数
- エンジン旋盤 x 4
- タレット旋盤 x 6
- CNC 旋盤 x 15
- CNC フライス盤盤 x 5
厳し公差管理
- 直線度 : ±0.001mm / ± 0.00005 in
- 同心度: ±0.001mm / ± 0.00005 in
- 直径 (外径/内径): ± 0.0005 in (± 0.0127 mm)
旋削部品規格
- 部品直径: φ5.0mm-380mm
- 部品長さ: 2.0mm から 300.0mmまで
CNC 旋削素材
CNC旋削部品は、各金属及びプラスチック材料で作製されます。金属材料は、アルミニウム、鋼、ステンレス鋼、黄銅、銅、マグネシウム合金、チタン合金などで加工できます。プラスチック材料は、ABS、POM、PEEK、アクリル、ナイロンなどで加工できます。ある工具鋼は固くて、旋盤やフライス盤で切断できないことで、特殊な処理することで製造時間が長くなります。柔らかな弾性体や柔らかなプラスチック素材の場合、回転できないので、切削工具の圧力によって、本来の形を維持できなくて、変形されることがあります。
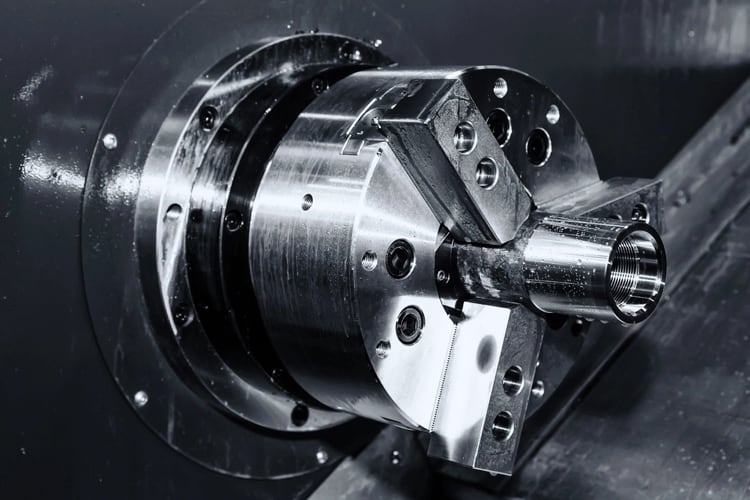
CNC 旋削金属素材
アルミニウムは、NC旋削金属材料の中で最も一般的な材料で、マグネシウム、鋼、ステンレス、黄銅、銅、青銅、チタン、ニッケル合金などの金属の加工にも使用されます。CNC旋削は、高強度と高精度、優れた表面仕上げを持つ部品を製造することができます。
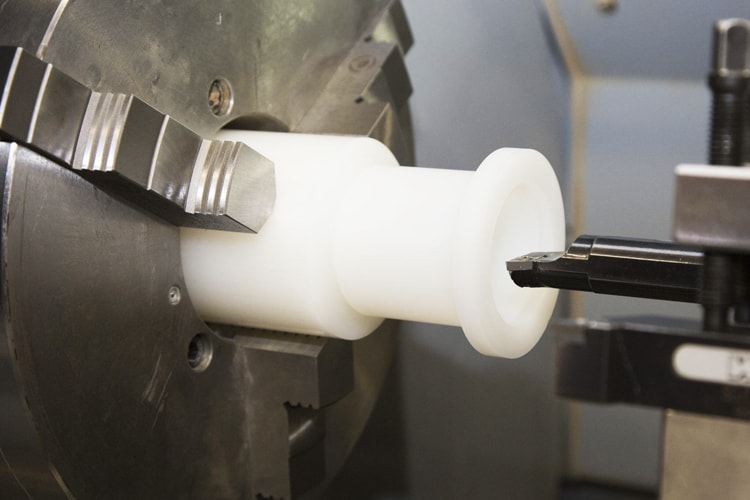
CNC 旋削プラスチック素材
精密CNC旋削加工は、通常に金属素材で行わいますが、プラスチック部品にも使用できます。一般的なCNC旋削材料としては、ナイロン、ポリカーボネート、ABS、POM、PP、PMMA、PTFE、PEI、PEEKで、3 Dプリントによりも最も良いカスタム部品を加工ができます。
CNC旋削後の表面処理
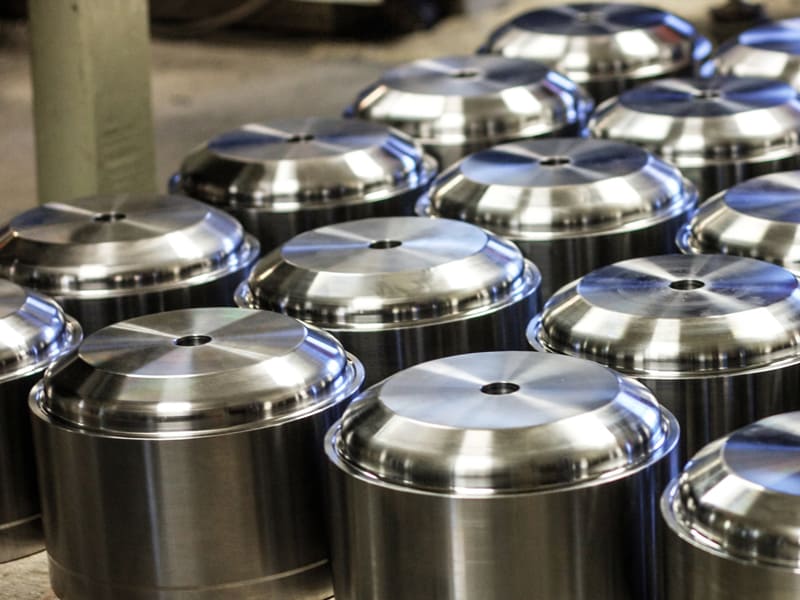
加工工数
これは最も経済的で迅速な表面処理オプションであり、旋削部品の表面には目で見える加工跡が残ります。表面仕上げは3.2 RAμmに相当し、特殊要求の場合0.1 RAμmのレベルになります。
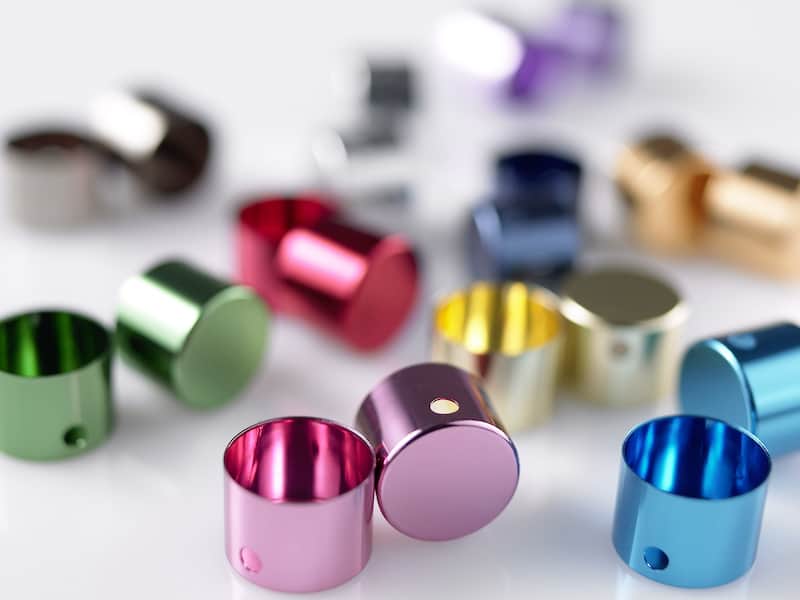
アルマイト
アルマイトは通常アルミニウム材部品に使用されている表面処理方法で、それ以外にチタン材部品にも使用されている。アルマイトされた部分の表面に硬い非導電性セラミックコーティング層があり、耐摩耗性を高くして、金属の質感と光沢を保ちし、外観が綺麗です。
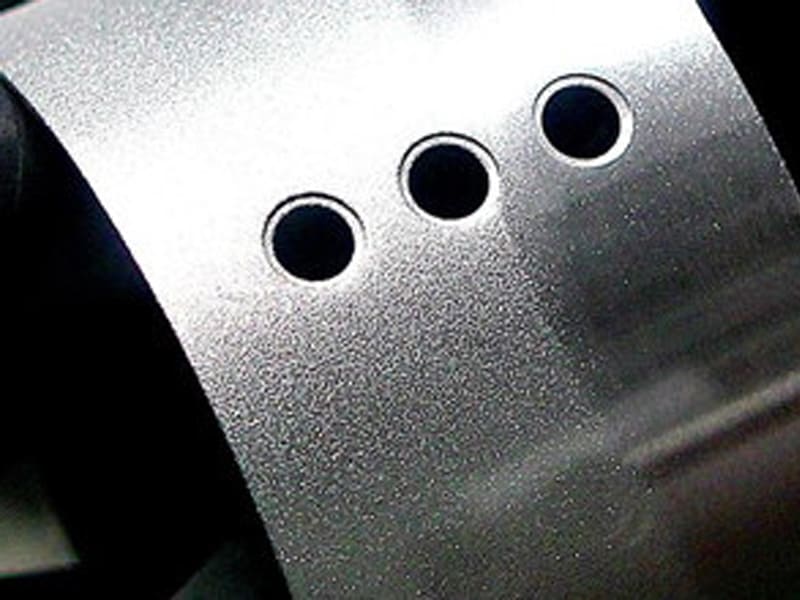
サンドブラスト
サンドブラストは、高圧条件で研磨剤を部品表面に研磨剤を噴射してマット効果にする方法です。サンドブラスト金属部品はサテンテクスチャまたはマット仕上げがあり、後処理跡を除去することができます。
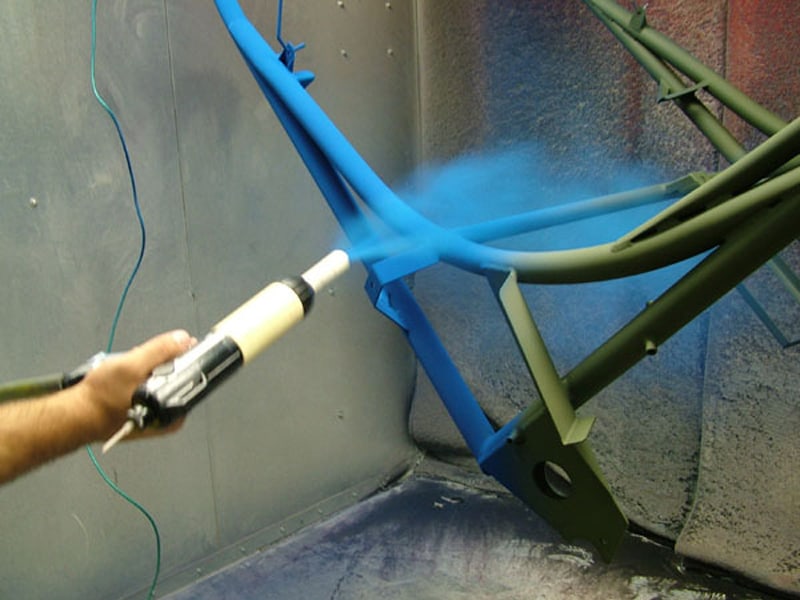
粉末スプレー
粉末スプレーは、高圧スプレーガンを使用して固体、カラーポリマーコーティングを部品の表面に塗布し、部品の耐摩耗性と耐食性を向上させる一般的な表面処理の一つです。
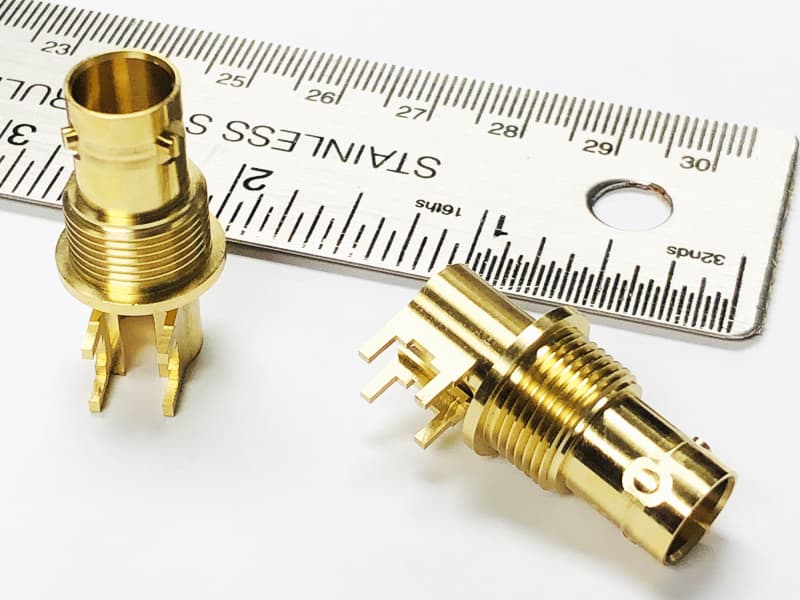
電解研磨
電解研磨はめっきの裏面であり、化学溶液を用いて金属表面を綺麗にする。電解研磨後、金属部品はより光沢があり、表面粗さを削減することができます。
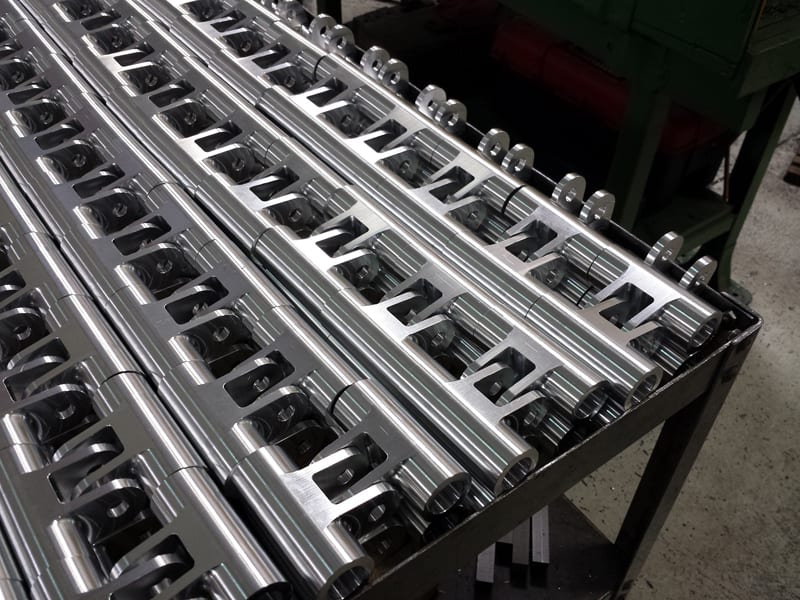
クロメート
クロメート クロメートは部品表面を酸化しにくい状態に変え、腐食速度を遅くする方法である。ステンレス部品によく使われています。
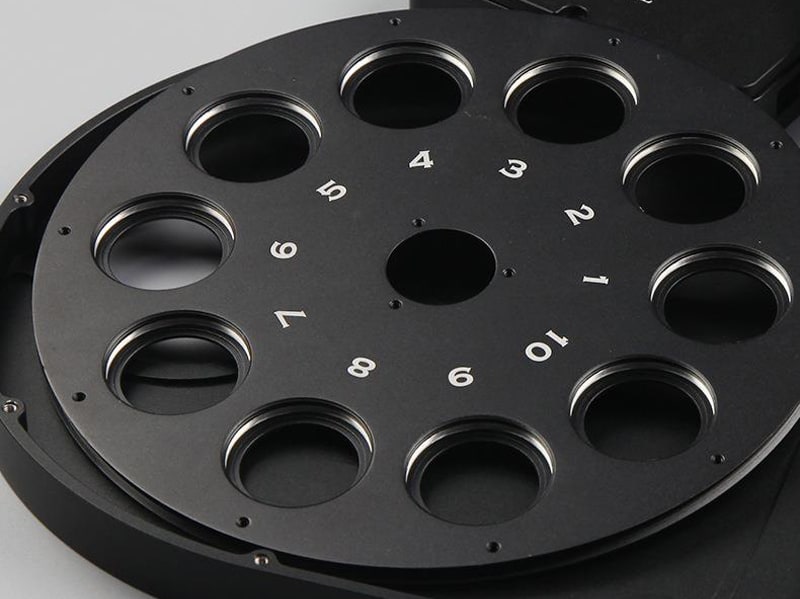
黒な染め
黒な染めは、鉄と酸化塩は、黒い酸化溶液中で化学反応により生成された化学コーティングである。黒な染めで酸化した部品は耐食性を高めることができます。
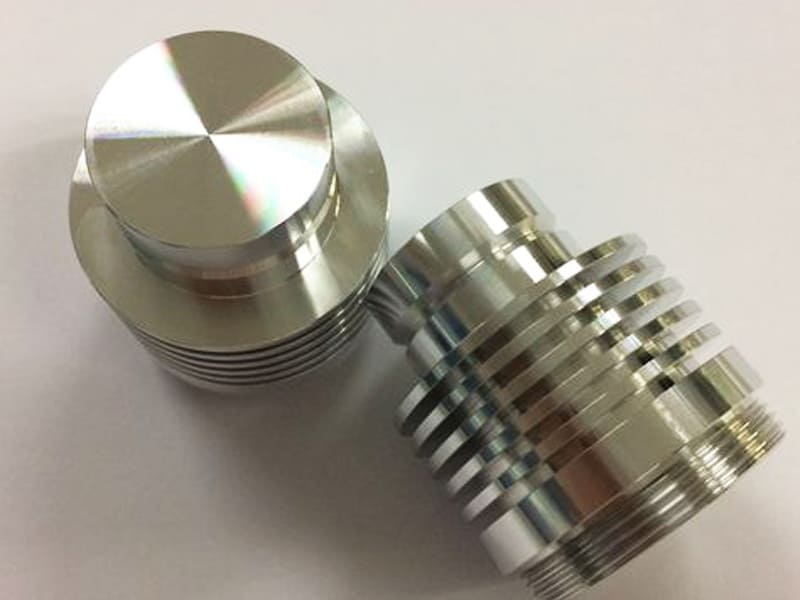
バフ仕上げ
バフ仕上げは、物理的な磨く処理によって部品表面を滑らかにする加工方法であり、通常は腐食防止と酸化除去に使用されます。
CNC旋削加工事例
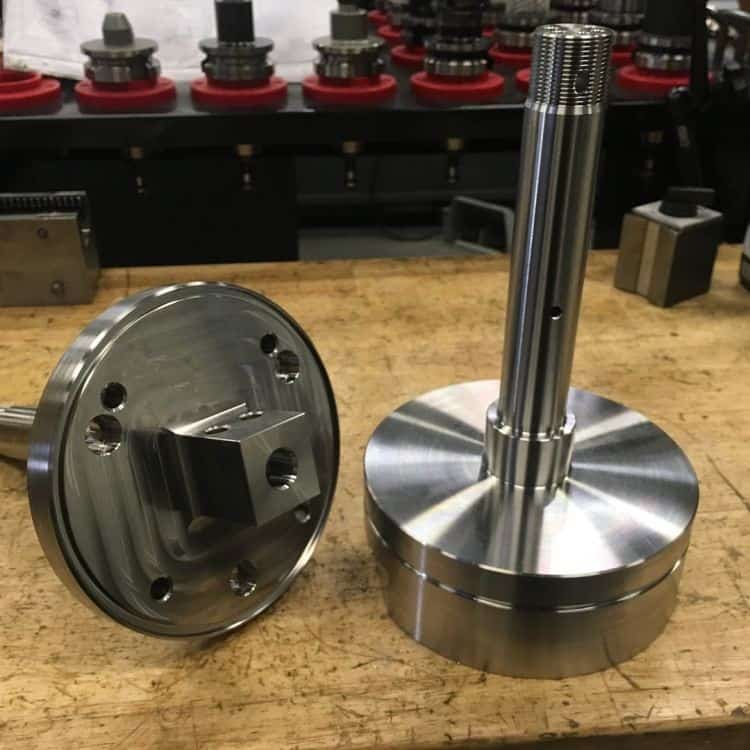
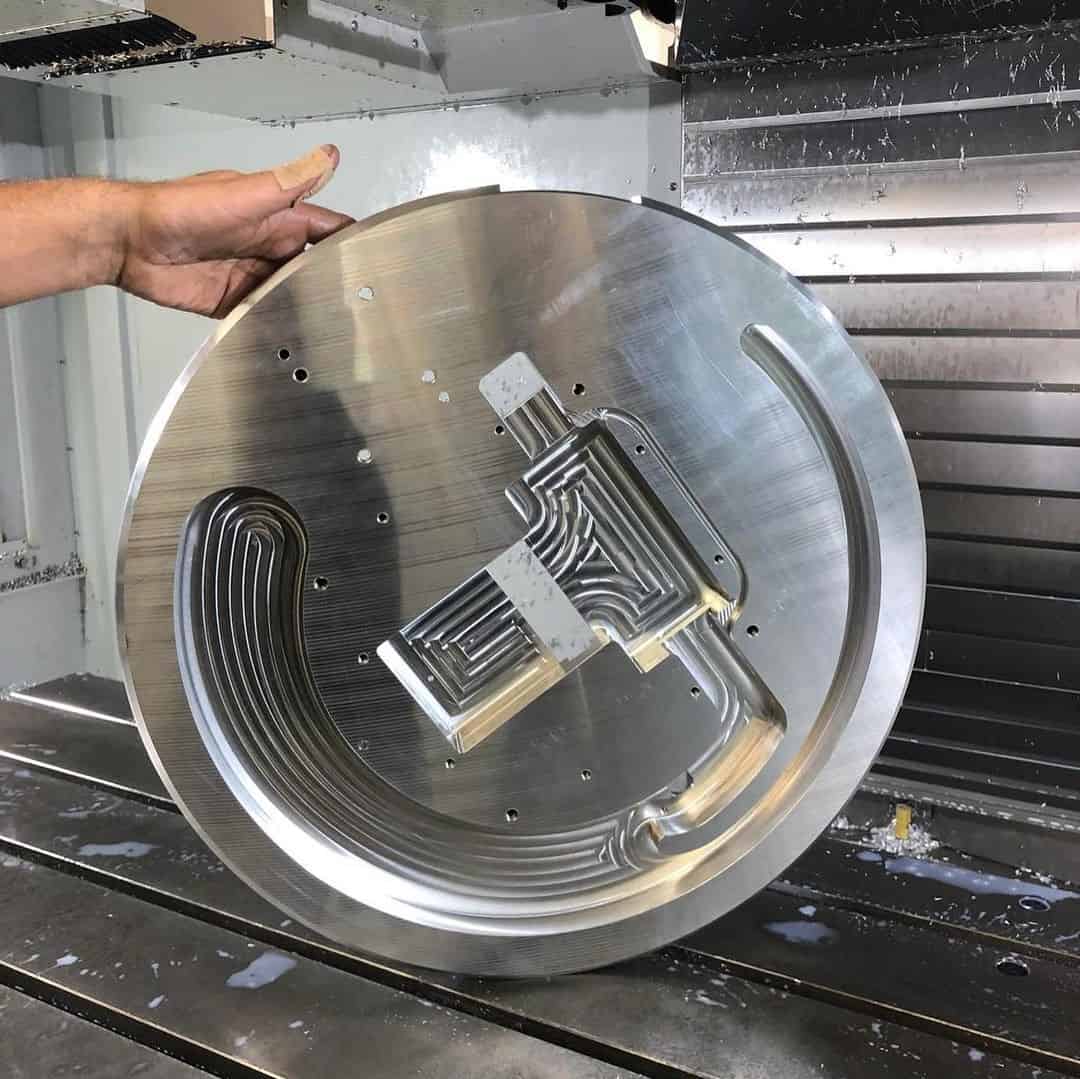
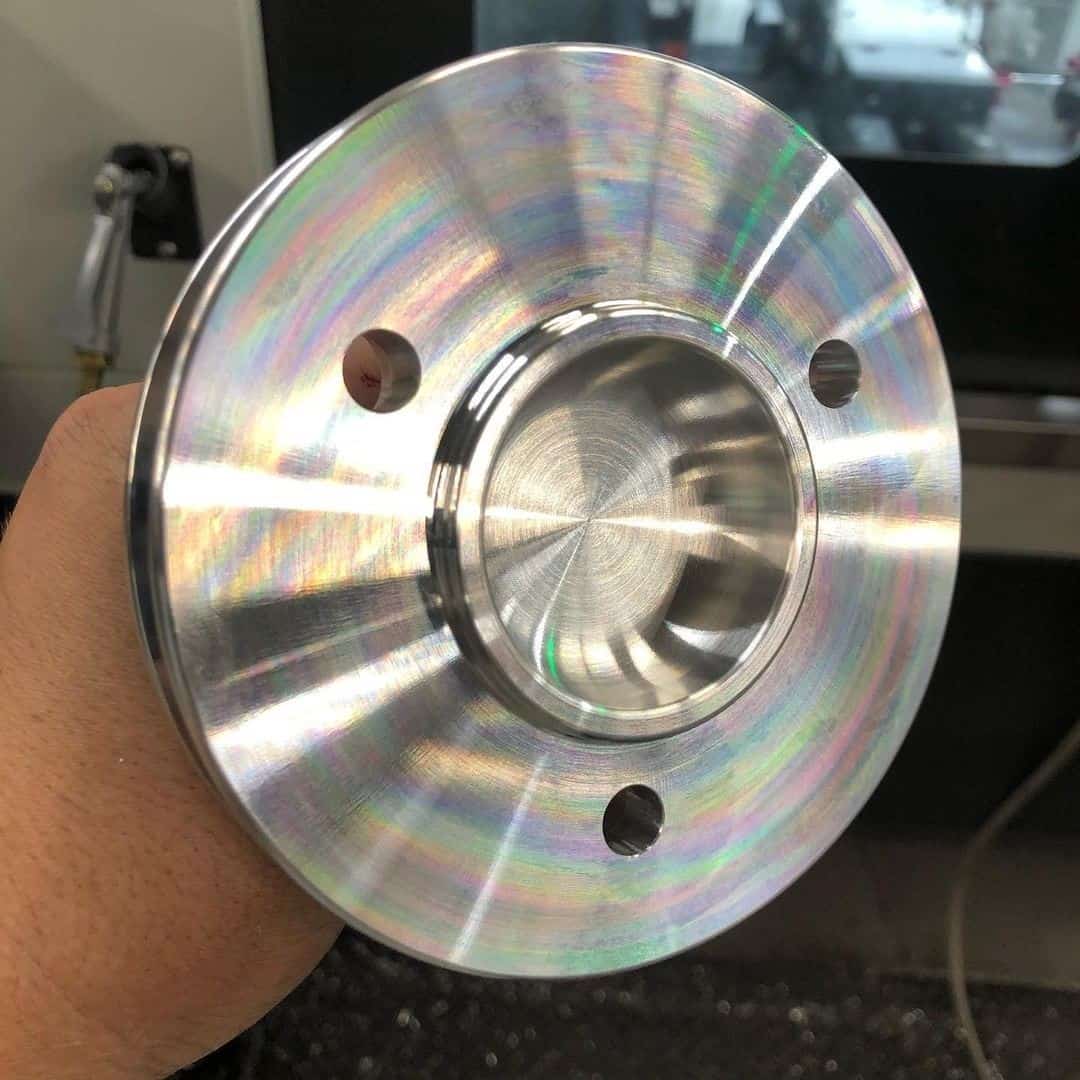
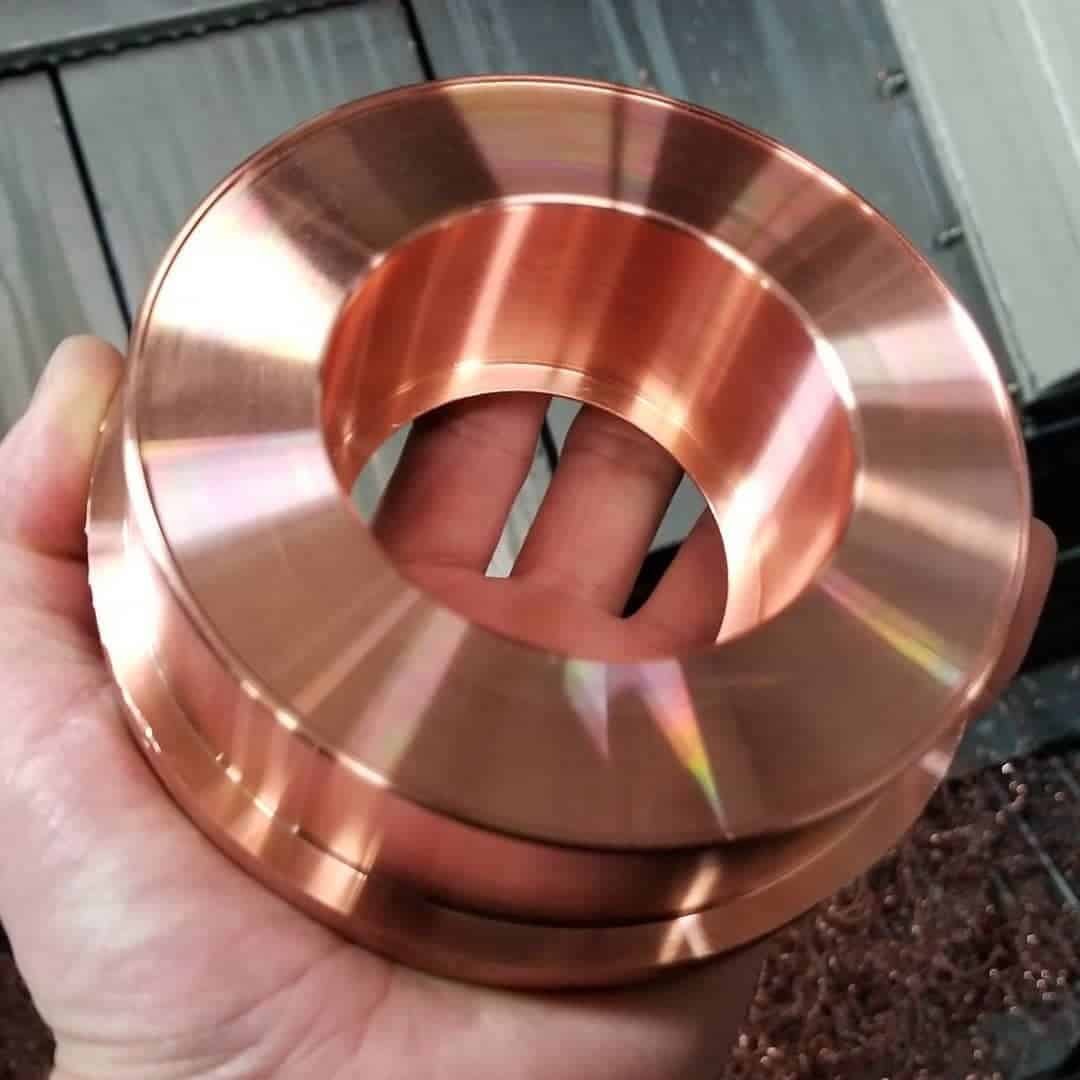
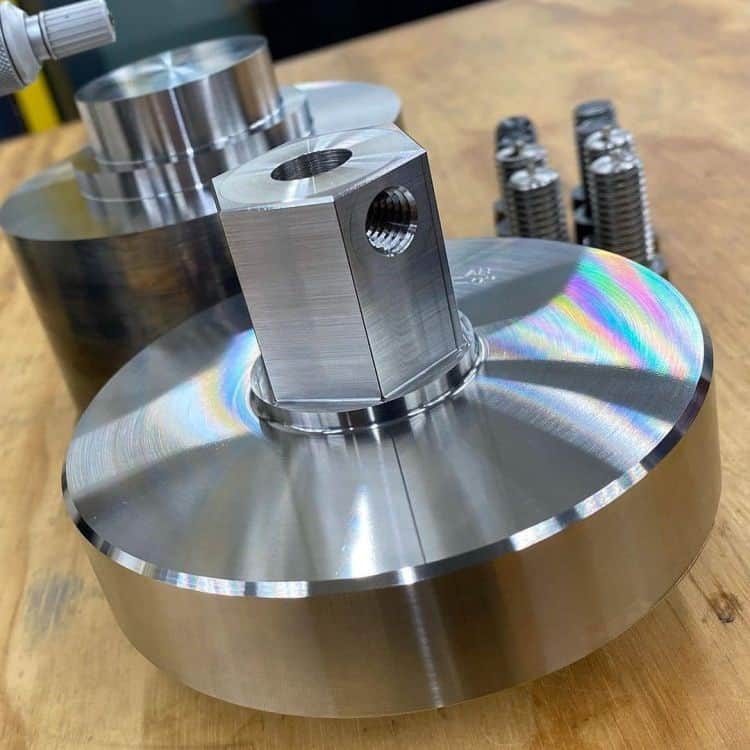
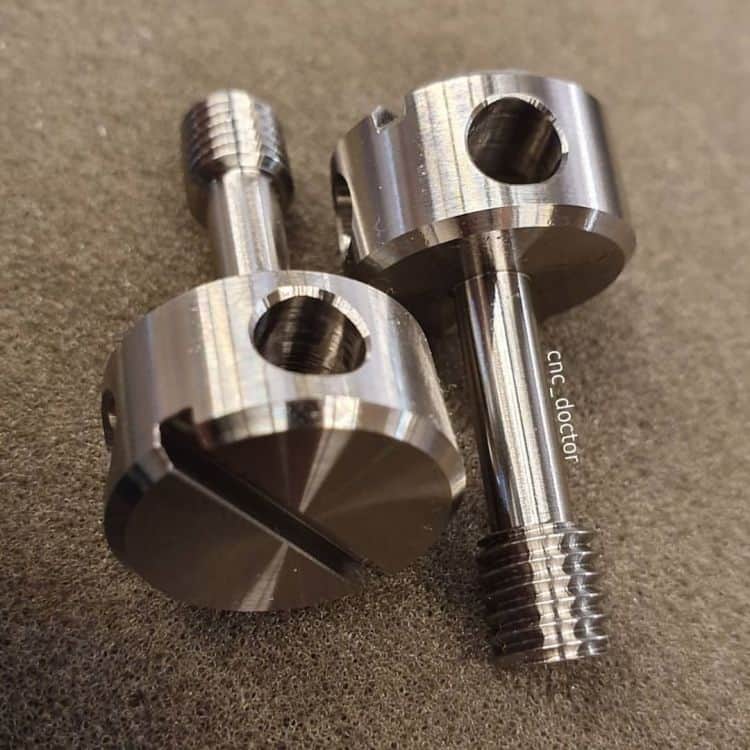
お客様の評価
「私がAN-Prototypeと協力した経験は素晴らしいです。彼らのコミュニケーションは非常に優れており、Michinはいつも私の質問に答えることができます。私たちが受け取った完成品は予想通りの最高品質を持っています。感謝するのは、私がいつもMitchinから得ている良質なサービスです。彼はいつも私たちの要求を満足することに力を入れている。総じて、信頼できるベンダーを探している人にはAN-PrototypeとMichinを強く推薦します。
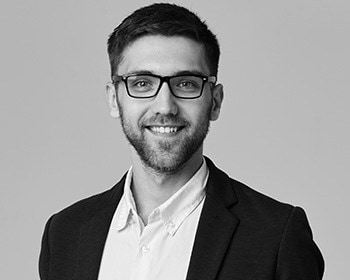
「複雑な5軸CNC加工部品であっても、AN-Prototypeからは非常に良い結果が得られました。過去2年間、AN-Prototypeと共に多くのプロジェクトを手掛けてきましたが、彼らは常に非常に優れた品質(彼からCNC加工サービスとアルマイト処理を薦めてもらったこともできます)、信頼性、非常に迅速で完璧なコミュニケーションを提供してくれました。DavideとVivianとの協力に感謝し、すでに多くのパートナーに紹介した。

「私のAN-Prototypeに対する体験はとても特別です。最初から通信は正確で迅速であり、難しい設計に対しても、ソリューションを提供します。プロトタイプ制作の価格は競争力があります。最終製品のQCも非常に優れています。続けて加工部品を依頼します。
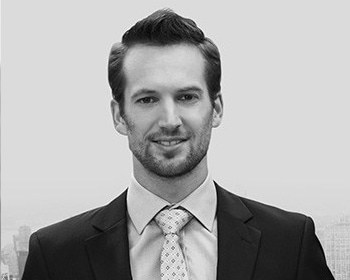