医療機器射出成形プロセス
- ISO 9001:2015, ISO 13485 認定書
- 無料 & 自動DFMフィードバック
- 最大公差 ±0.002mm
- OEM & ODM 1Pcsから

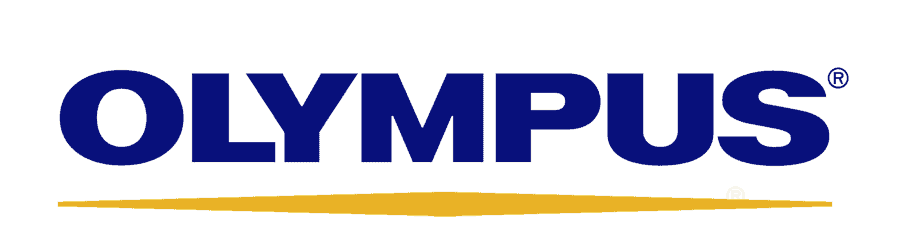
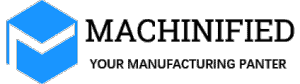

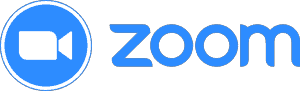
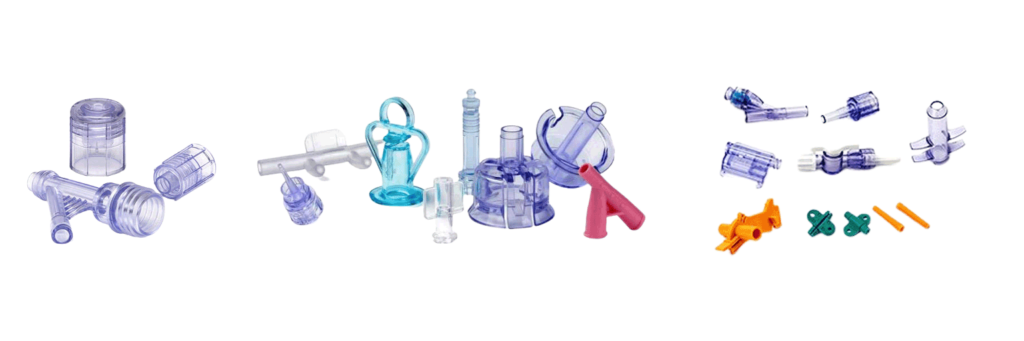
医療用射出成形の見積もりをもらう
STEP | STP | SLDPRT | IGS | X_T | PDF ファイル
- すべてのアップロードは安全で秘密保持されています
医療機器用プラスチック射出成形プロセス
医療用射出成形はプラスチック医療機器と部品を製造する技術である。プラスチック樹脂粒子を溶解して、溶解した材料を金型に注入して特定の形状に形成する方法です。この成形方法は、製品の寸法と形状を正確にコントロールできて、厳し品質と規制基準を守ることができます。医療用射出成形は、耐久性が高い、信頼性があるFDA承認取った医療機器を製造することができます。必要なFDAの承認を取るためプロトタイプの作成するにも適用です。
FDA 要求
アメリカ食品医薬品監督管理局(FDA)は、医療機器や部品は人体との接触の程度に応じて、プラスチック材料に対して、3つの要求があります。
規則最も厳しい医療機器は人体に埋め込まれるプラスチックである。これらの医療機器に対して、多くの要求があります。必ず認証されて毒性がなく、インプラント品はライフサイクル全体で分解されないことを証明できる材料で作ること。部品製造用環境として、認証されたクリーンルームで製造する必要があります。
医療機器の定格値は人体の皮膚と長時間接触することである。これらの医療機器のFDAの要求は比較的緩和されており、多くの射出成形会社が製造できます。
最後の医療機器は人体との接触が限られている。例えば、電子血圧計、人の体と接触するのは、ディスプレイのプラスチック筐体やプラスチックボタンが限られています。他の医療機器と比べてこれらの医療機器のFDA法規は最も少ないです。
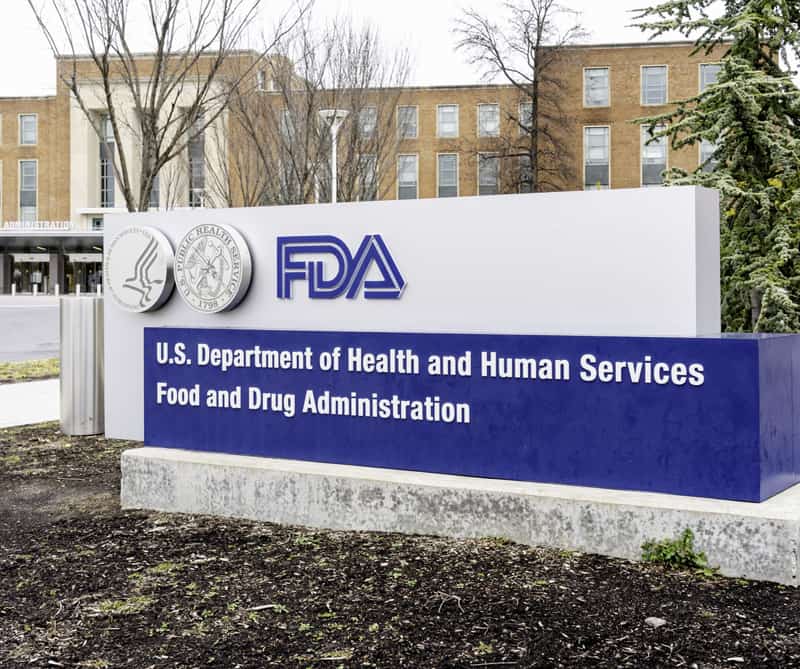
医療用射出成形とは?
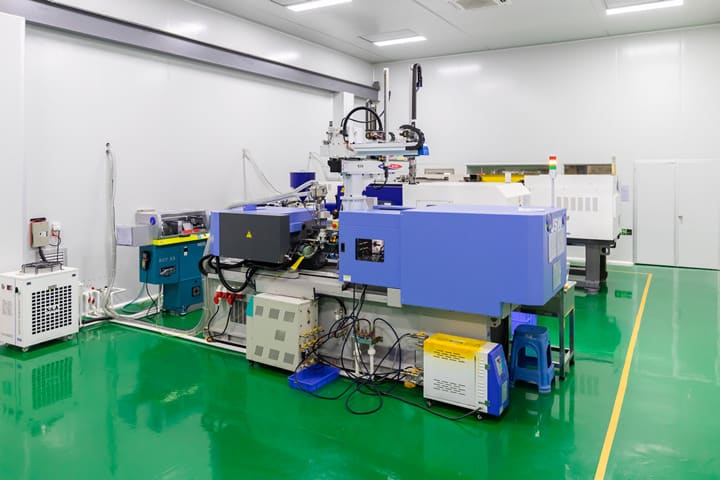
世界中各地の病院、診療所、毎日大量の医療用プラスチック製品を使っている、研究実験室、大学はは、プラスチックで医療部品、設備、器具、サポート設備を製造している。プラスチック射出成形方法は、量産の精密医療製品を製造する理想的な方法である。射出成形された医療機器には、中実部品、中空部品、半中空部品と中空シェル部品などあります。
射出成形方法は、時間的に速くて、コスト効果がある製造技術であり、プラスチック部品のロット生産に適用されています。医療用射出成形は、医療業界で使用されているプラスチック部品の製造方法である。射出成形は先に鋼型から始まります、部品のマイナスのキャビティを2つの強度高い鋼型に加工して、その2つの金型を射出成形機に入れて、圧力によって金型が固定されます。溶かしたプラスチックの溶体を金型に注入して、プラスチックが固まると、金型は開かれて部品が押し出されます。同じサイクルを繰り返します。
AN-Prototype医療用射出成形クリーンルーム
AN-PrototypeはISO 901:2015とISO 13485の認証を取得した射出成形会社で、各業界の製品を製造した経験を持っています。近年、新型コロナウイルスが世界中で猛威を振るっている時期、AN-Prototypeは巨額の資金を投じて国内有名ブランドの先進的な射出成形機を購入し、さらにISO 8(100 K)認証のクリーンルームに投資しています。AN-Prototypeは、医療および歯科業界に卓越した医療射出成形ソリューションを提供しています。私たちはさまざまな医療用樹脂材料を使って、II級とIII級の医療用部品及び設備を製造した経験を持っています。
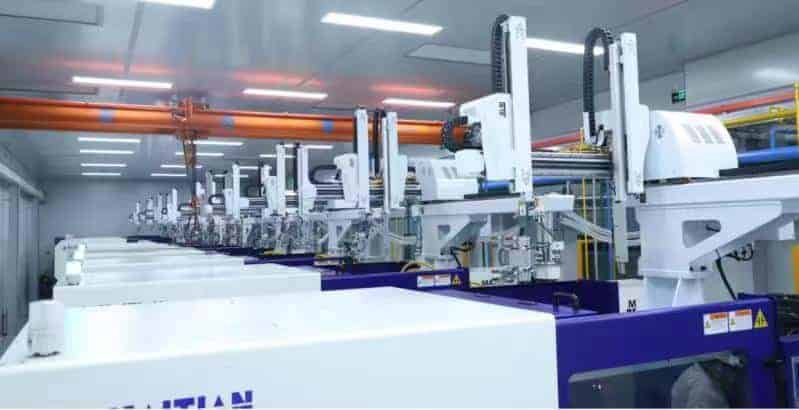
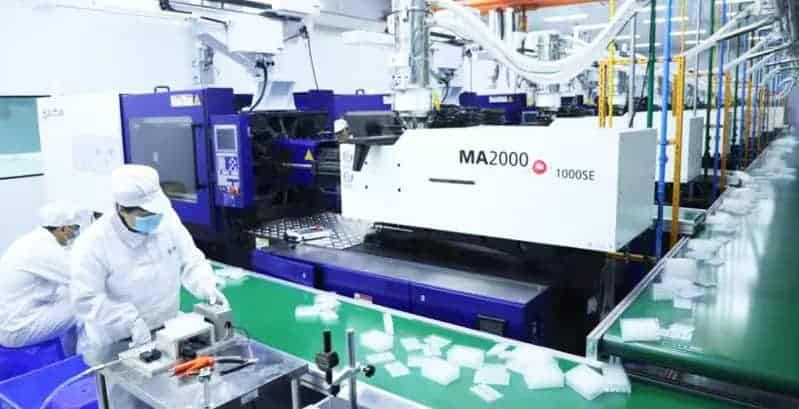
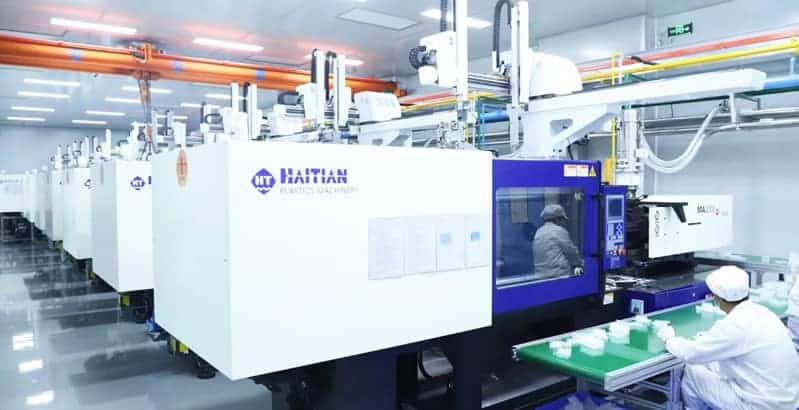
AN-PROTOTYPE医療用射出成形品写真
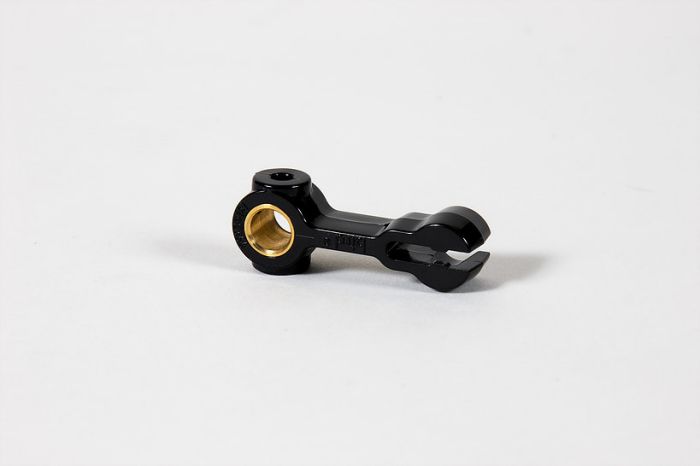
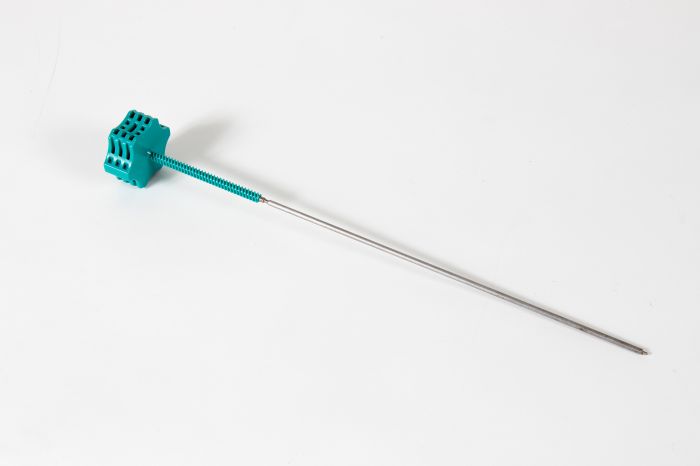
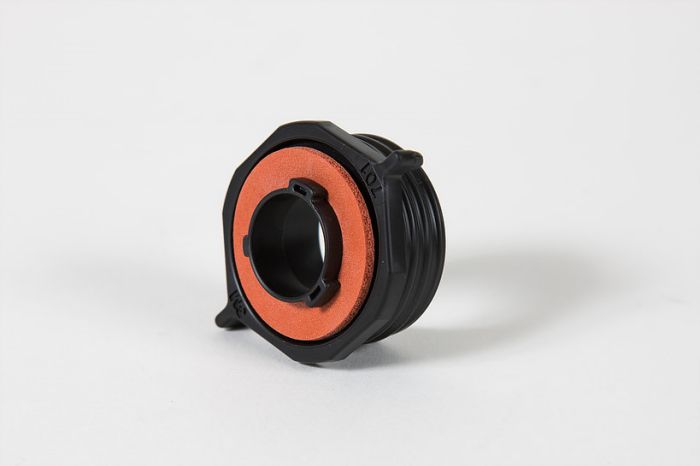
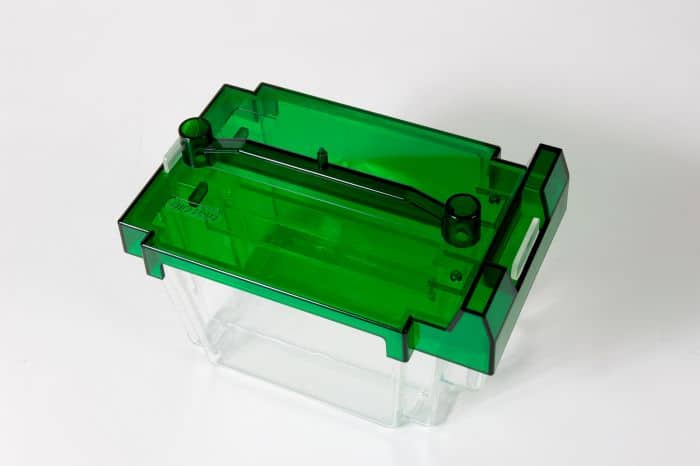
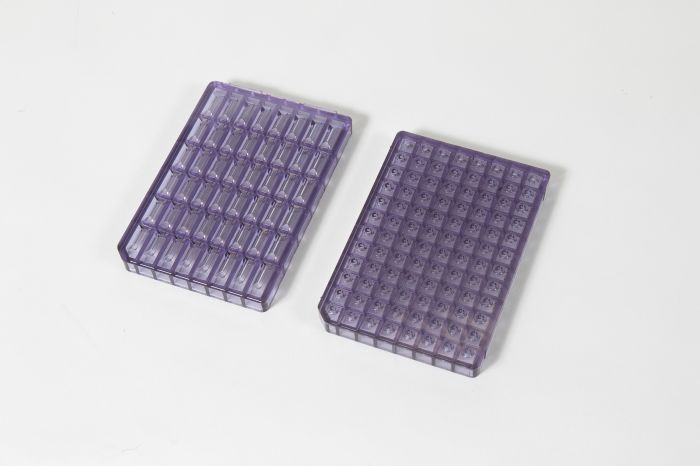
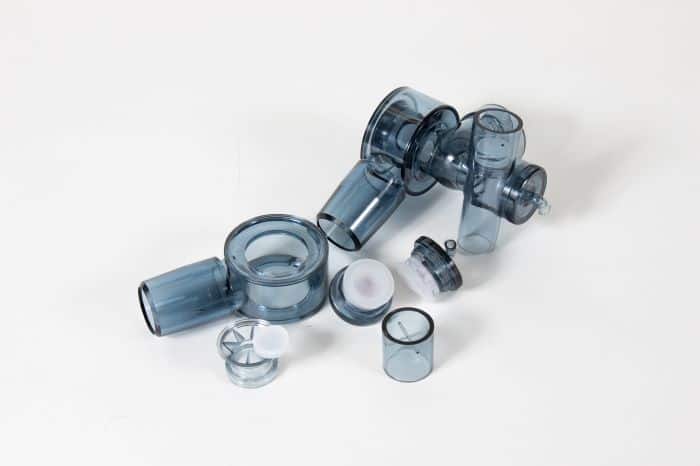
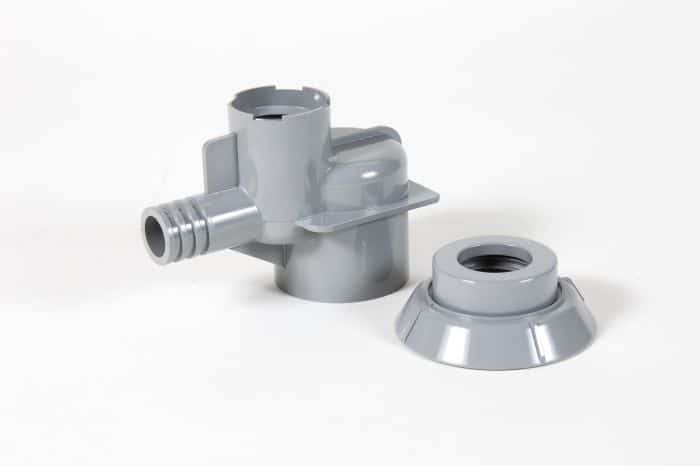
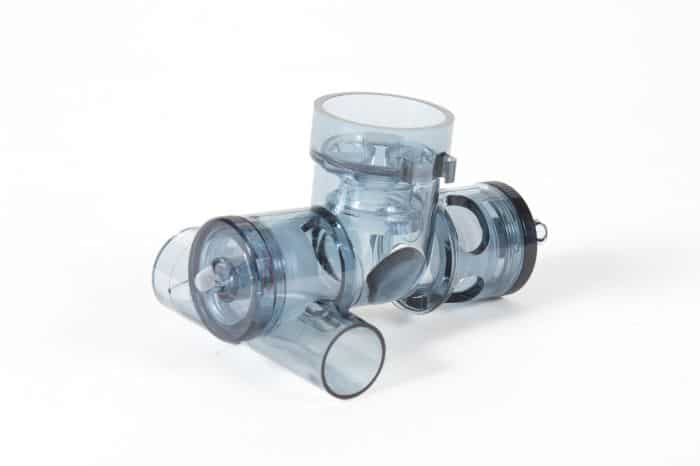
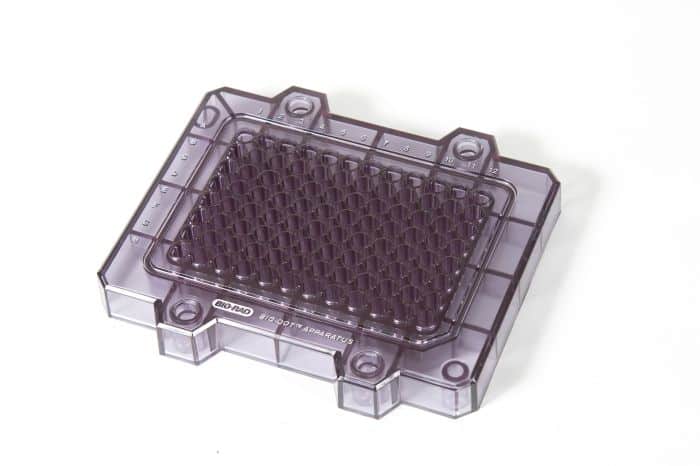
適切な医療用プラスチック材料を選択する
医療機器を製造するために使用される材料は、医療機器標準を遵守しなければなりません。熱可塑性プラスチック、特に「医療用レベルプラスチック」と呼ばれるプラスチックは、FDAのすべての要求に合致し、医療用注射器具を製造する優れた材料となっている。医療用プラスチックの射出成形に使用できる様々な等級のプラスチックがたくさんあります。AN-Prototypeはプラスチックには、それぞれのタイプの利点と欠点があることを考慮すべきです。医療用プラスチックの射出成形を使用する際、下記のすべての要素を考慮しなければならない。
強度
作業環境
抗菌
耐化学性及び耐熱性
射出成形方法はさまざまなプラスチック材料成形に適用です、必要な医療用レベルのプラスチックを使用して医療部品や製薬部品を製造するのに最適でな方法です。多くのプラスチックは医療用射出成形に適用して、それぞれのプラスチックは独特の性能と性能特徴を持っている。医療用射出成形の一般的なプラスチック材料の選択には、下記の素材が含まれています。
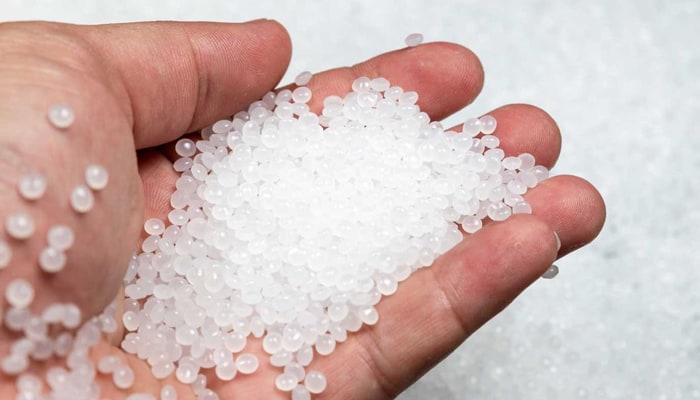
ポリプロピレン(PP)
ポリプロピレン(PP)は強度と耐久性がある素材で、医療用射出成形品の最も一般的なプラスチックの1つである。ポリプロピレンは強い化学結合が含まれて、ビーカーや試験管などの医療機器用より良い材料である。
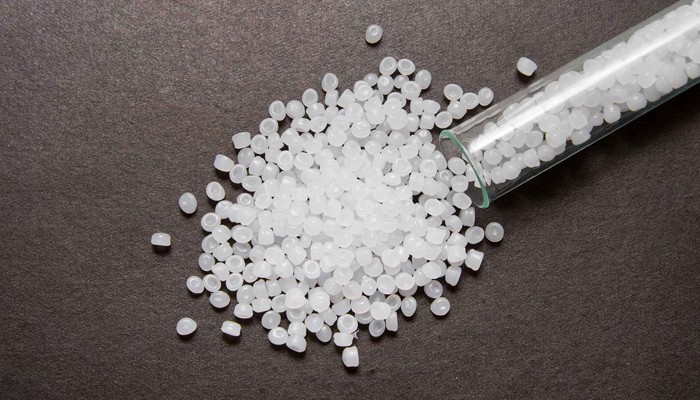
ポリエチレン
ポリエチレンはよく使用されている熱可塑性プラスチックであり、LDPE、HDPE、UHMWなど多種類のバリエーションがあり、それぞれレベルの剛性と耐久性を持っています。UHMWは通常、股関節、膝関節または他の関節の義肢に使用されている。
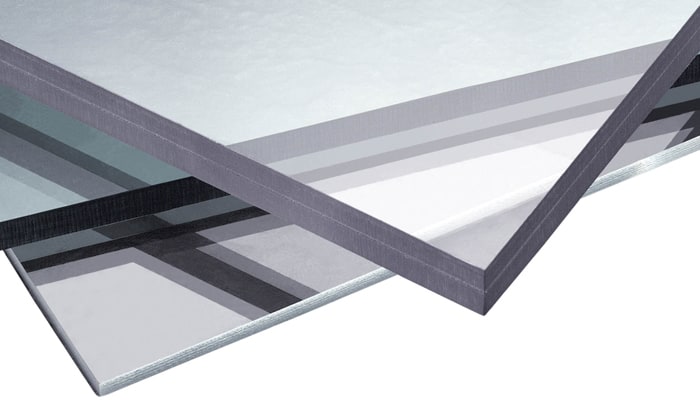
ポリカーボネート
ポリカーボネートは天然で透明な医療用レベルの材料であり、医療用の管材によく使われて、高い延伸、せん断、曲げ強度などの特性があります。また、高耐熱性、低吸湿性があり、アクリル酸よりも硬くである。
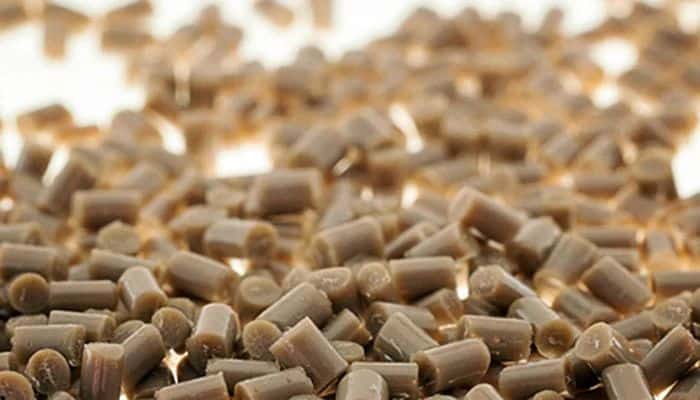
ポリエーテルエーテルケトン(PEEK)
PEEKは特殊な医療用レベルのプラスチック樹脂であり、耐化学性、耐裂性、耐疲労性が強くて、高圧滅菌により滅菌することができる。FDAによって食品接触用に承認されており、UL 94 V-0可燃性等級がある。
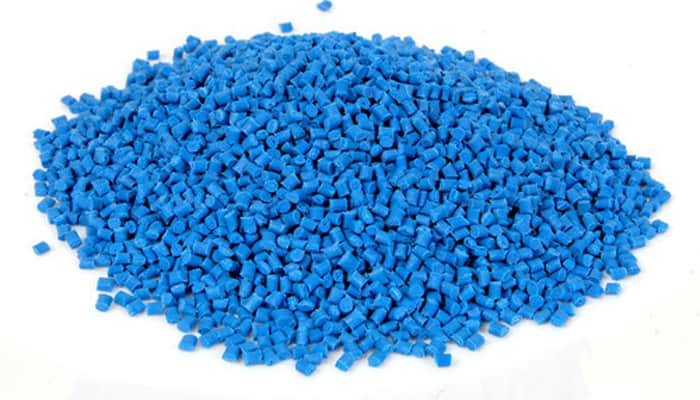
ポリアミド(ナイロン)
ナイロンはその強度、靭性、耐化学性、耐摩耗性など特性があり、医療用部品によく使用されている。ナイロンは多くの化学品に抵抗力があるが、強酸やアルコールに敏感である。
- ISO 9001:2015, ISO 13485 認定書
- 無料 & 自動DFMフィードバック
- 最大公差 ±0.002mm
- OEM & ODM 1Pcsから
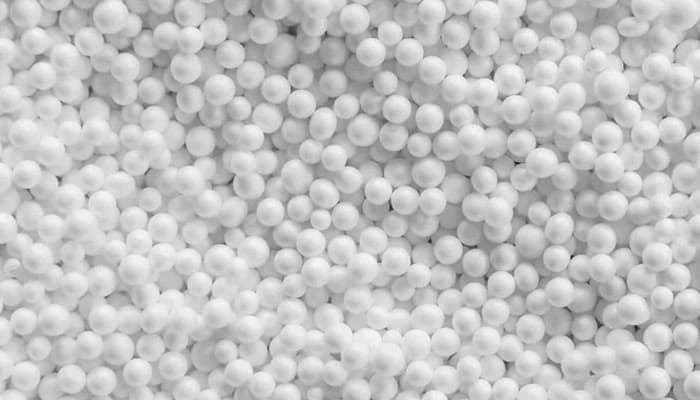
ポリスチレン(PS)
ポリスチレンは柔軟性が低て、硬いプラスチック素材であり、優れた加工性、良好な耐衝撃性、良好な寸法安定性を持っている。殆どその美学的品質とカスタマイズしやすい表面処理にて使用されている。
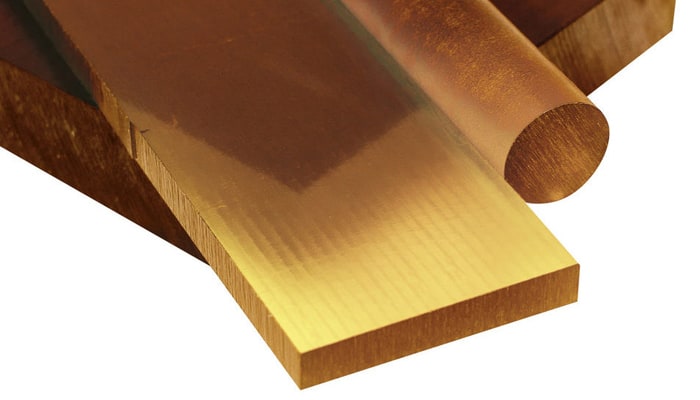
ウルトラム™
Ultem ™は 外部環境において耐応力と耐裂く割れ性、優れた寸法安定性を持って、優れた強度と剛性で、医療機器によく使用されている。
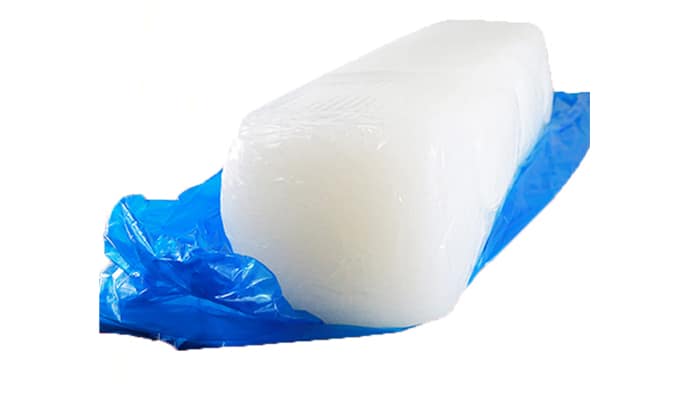
シリコーン
シリコーンは柔軟性医療コンポーネントの第一選択材料である。シリカゲル医療部品は非常に耐久性があり、生体適合性があり、価格も合理的で、大量生産のコストを下げることができる。
医療機器製造用各タイプの射出成形
射出成形は、高温でプラスチックポリマーを液化して、アルミニウムまたは鋼金型で再成形または射出成形によって必要な形状にする、プラスチック射出成形は医療業界に対して、非常に価値があります。この成形作業が必要な衛生的な条件下で行われます。液化されたプラスチックの高温は、患者の健康に危険する汚染物や微生物が含まれていないことを保証すること。医療機器を製造するための射出成形方法を幾つか紹介させていただきます。
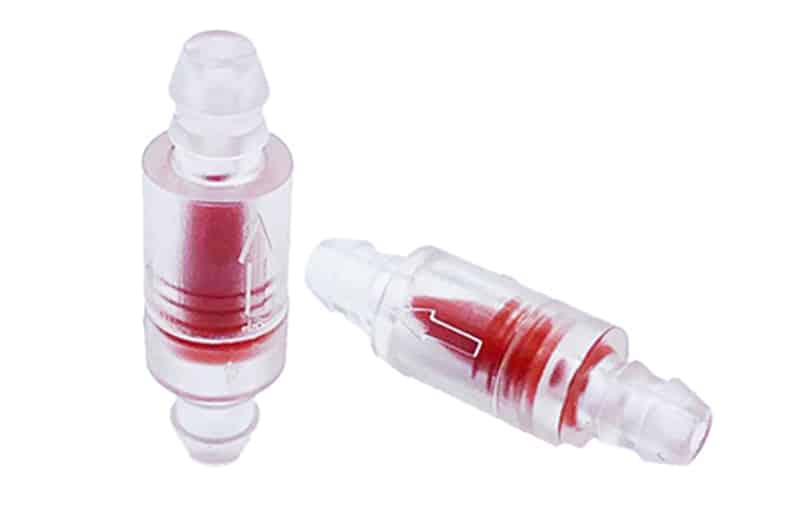
被覆成形
被覆成形は射出成形であり、成形および硬化された構造(基材)上に1つまたは2つの部品を成形すること。このプロセスは複射成形と呼ばれ、少なくとも2つのステップとより長い製造サイクルが必要です。この技術は、プラスチック製造にとって価値がある。特にしっかりと把持する必要なハンドルやアセンブリ部品を製造する際によく使う成形方法である。
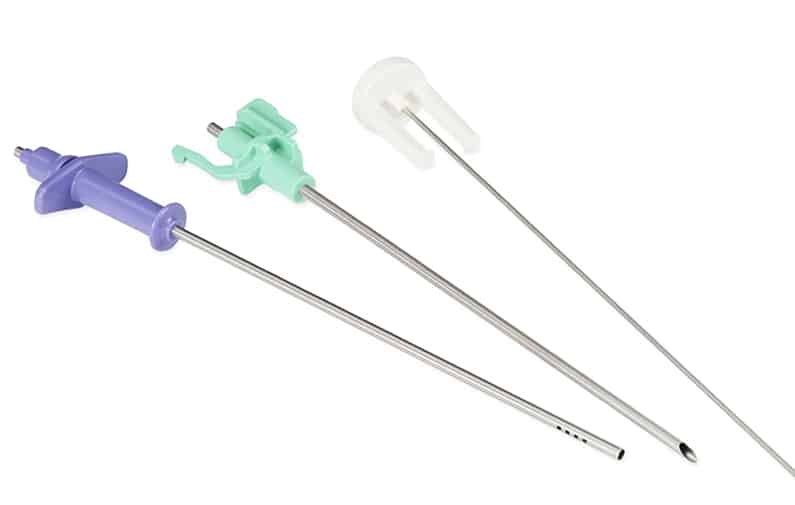
インサート成形
インサート成形は、被覆成形と似ていますが、インサート成形は単一のプロセスである。1つの部品が既にある部品(インサート)上で成形されるので、基材(インサート)は予め存在している構造ですある、また、この技術はプラスチック部品に限らず、成形インサートは金属または合金でも作られます。
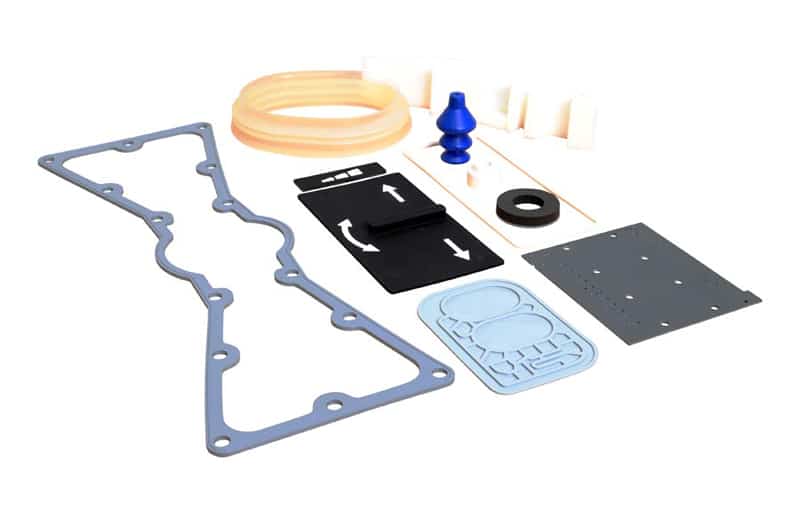
シリコン射出成形
シリコンは加熱によって溶融状態になって、医療製品に必要な形状に成形する。シリコンは医療業界で使用される代表的なプラスチックポリマーでありますが、シリコン金型はアルミニウムや鋼金型ほど耐久性がないため、シリコン射出成形は一般的に小ロットの医療部品、特に医療プロトタイプの製造と製品開発の初期段階で使用することができます。
ご注意していただくこと
医療機器用射出成形に関するご注意項目
医療機器のプラスチック射出成形は重要な技術であり、故障リスクの発生は非常に高いので、設計、計画、製造の途中に注意すべき項目があります。
FDA法規
ISO認証
材料特性
耐久性
表面処理オプション
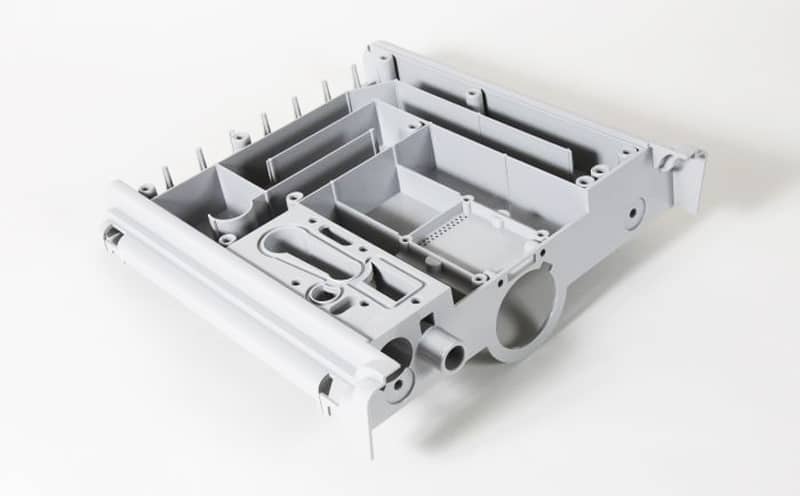
成形後加工
射出成形部品に追加でCNC加工を行い、部品のバリを除去することで、設計仕様をよりよく満たすために製品を完成させることができます。
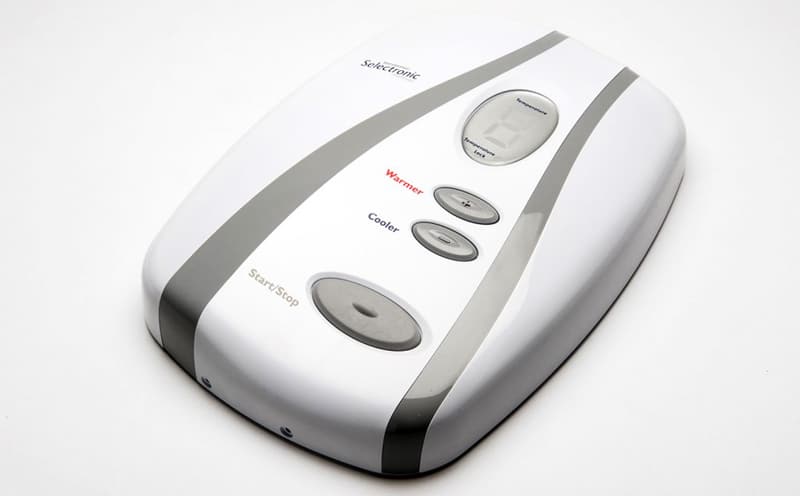
パットプリント
ロゴ、ラベル、部品番号などディテールやブランドをプラスチック部品に追加する方法。また、カスタム着色剤を開発することにより、Pantoneカラーまたは物理サンプルにマッチングすること。
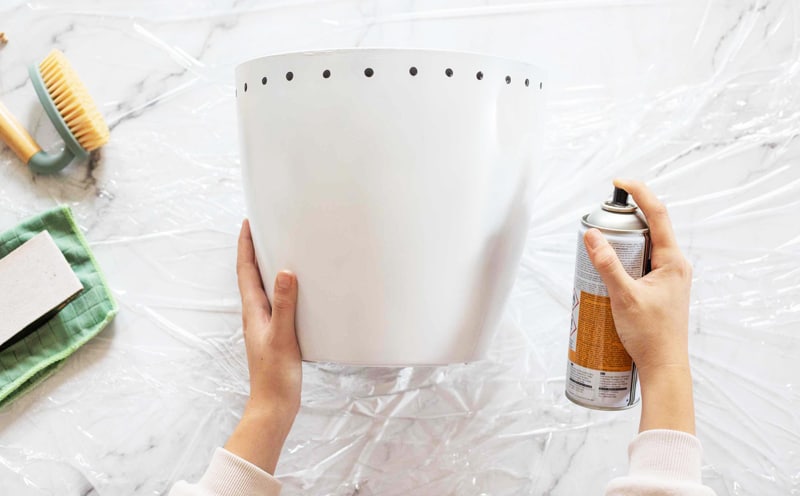
ペイント
塗装は部品に色を追加する最も簡単で、最もコスト効果のある方法です。AN-Prototypeの専門家は、部品の最終用途に最適なコーティング提案を提供することができます。
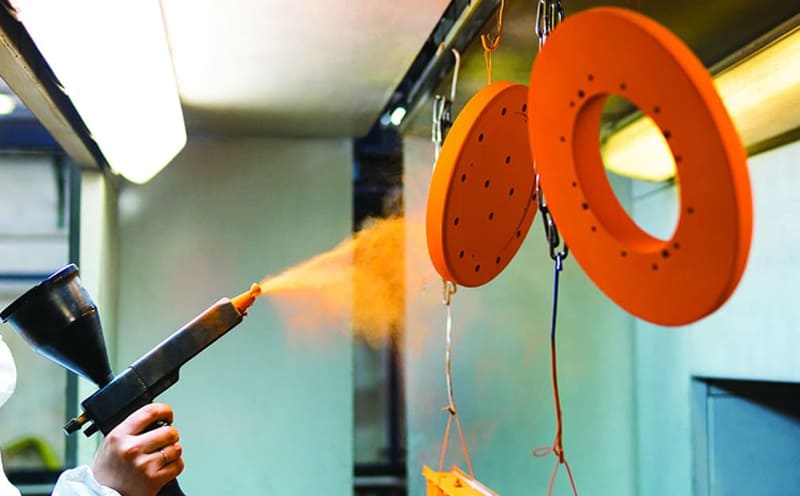
粉末塗料
粉末塗料はペンキより耐久性が高く、衝撃、湿気、化学品を防ぐための追加保護になります。粉末塗料にはさまざまな色と木目があります
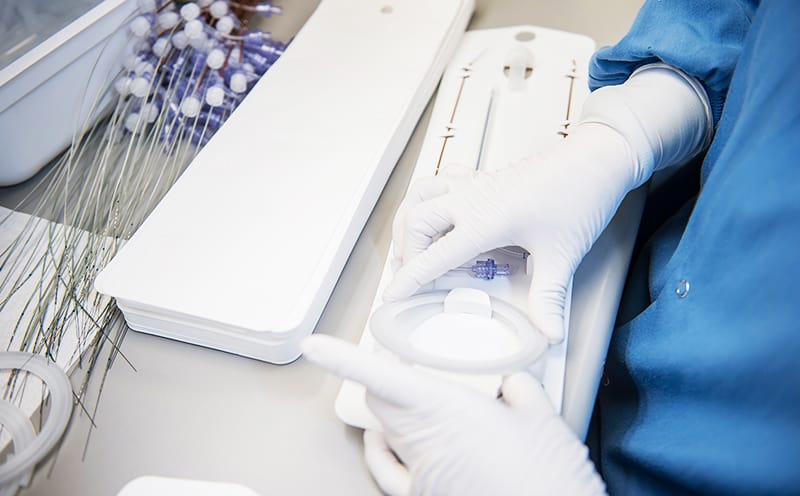
組み付け
AN-Prototypeは、加工した部品を組み付けて、機能的な製品になります。
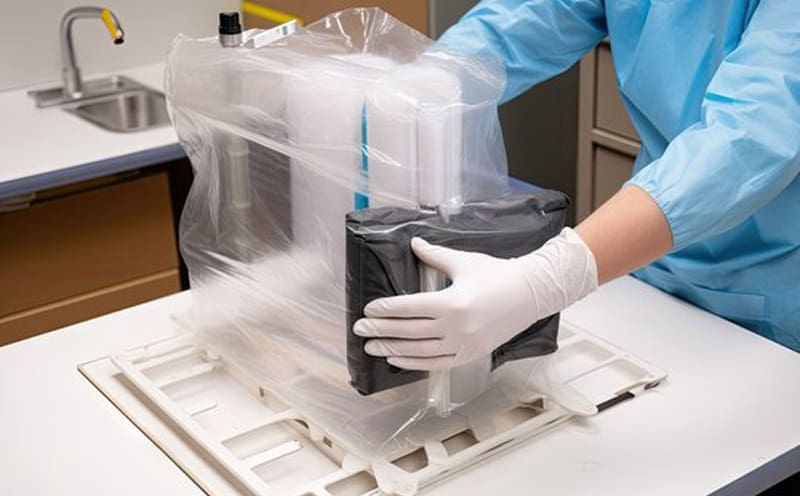
梱包
組み立て後、AN-Prototypeは完成品をバブルボックスまたはカスタムボックスに入れ、DHLまたはFEDEXにて、お客様に届けます。
ISO認定の医療用プラスチック射出成形メーカ
AN-Prototypeはエンジニアリング樹脂と特殊医療用プラスチックに関する専門知識により、医療用射出成形製品が適切な規格を満たすことができます。ISO 13485:2016医療機器製造の全面的な品質保証管理認証を取得しました。
設計要件について、お客様のお問い合わせによって、必要な医療成形プロセスと材料の最適性を判断して提案します。医療用射出成形に適用しない部品もありますが、その場合は適切なプロセスを提供します。私たちの目標は、お客様の予算範囲内で医療成形および医療機器プロトタイプ作成ソリューションを提供するとともに、お客様のアプリケーション設計要件を満たす製品を提供することです。また、生体適合性を持つ、医療成形法の要件に適合する医療用レベルのプラスチック材料を提供することの重要性を十分理解しています。
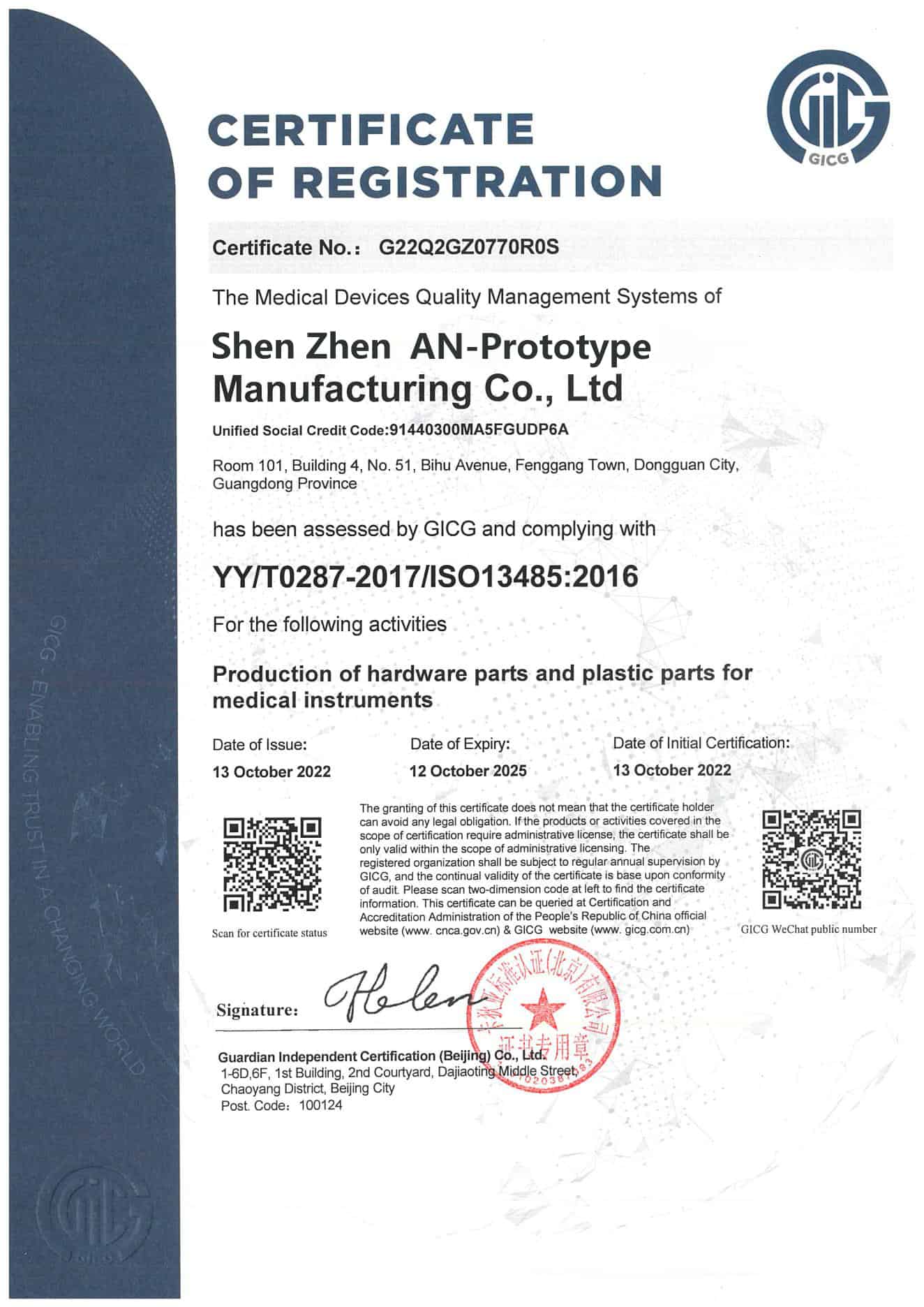
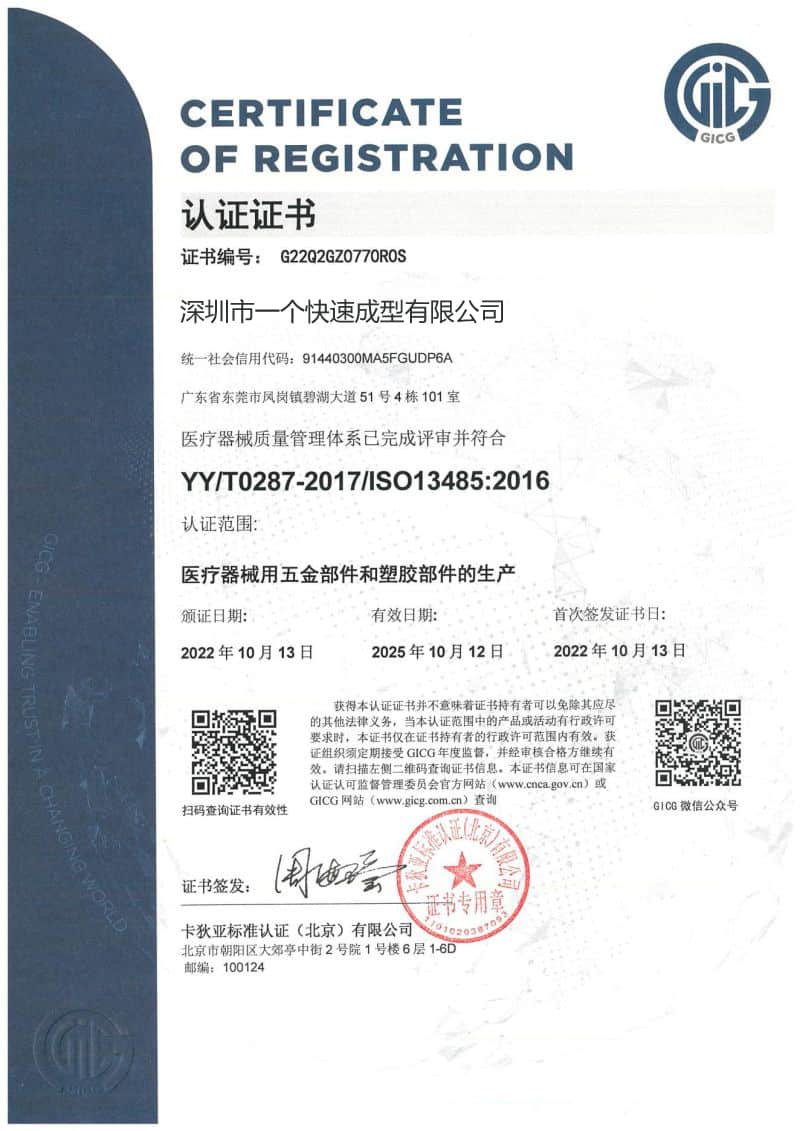
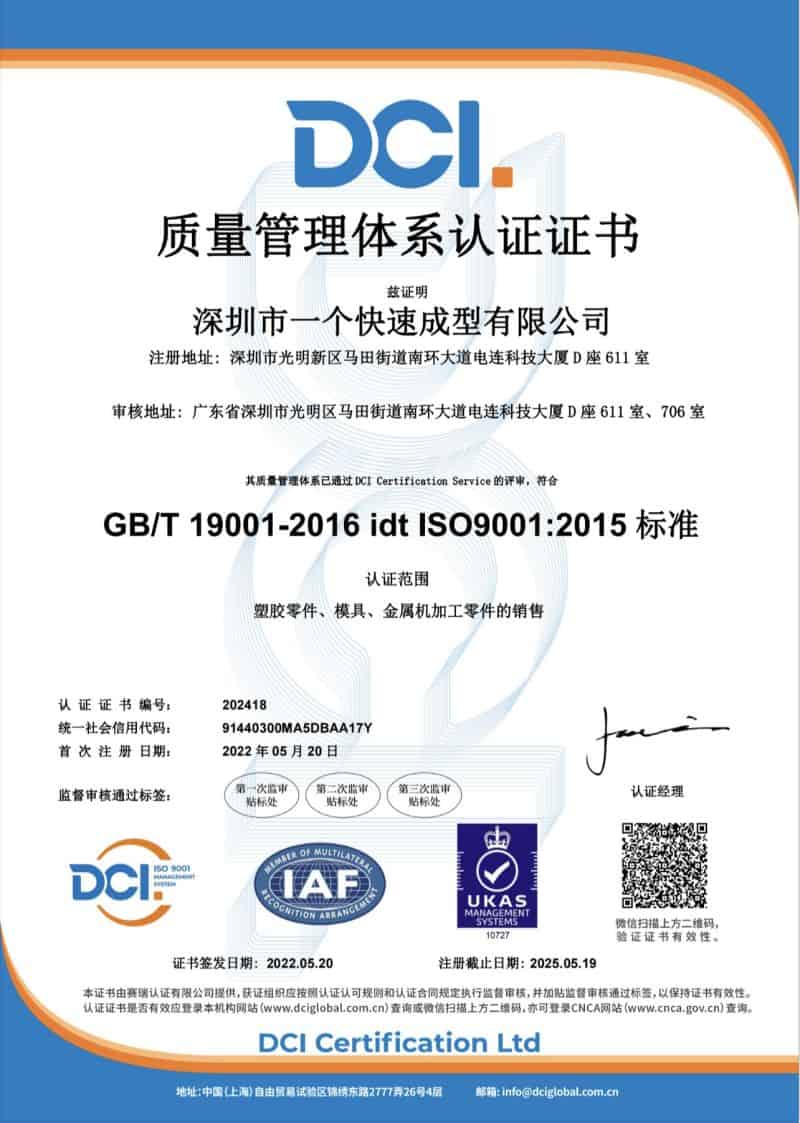
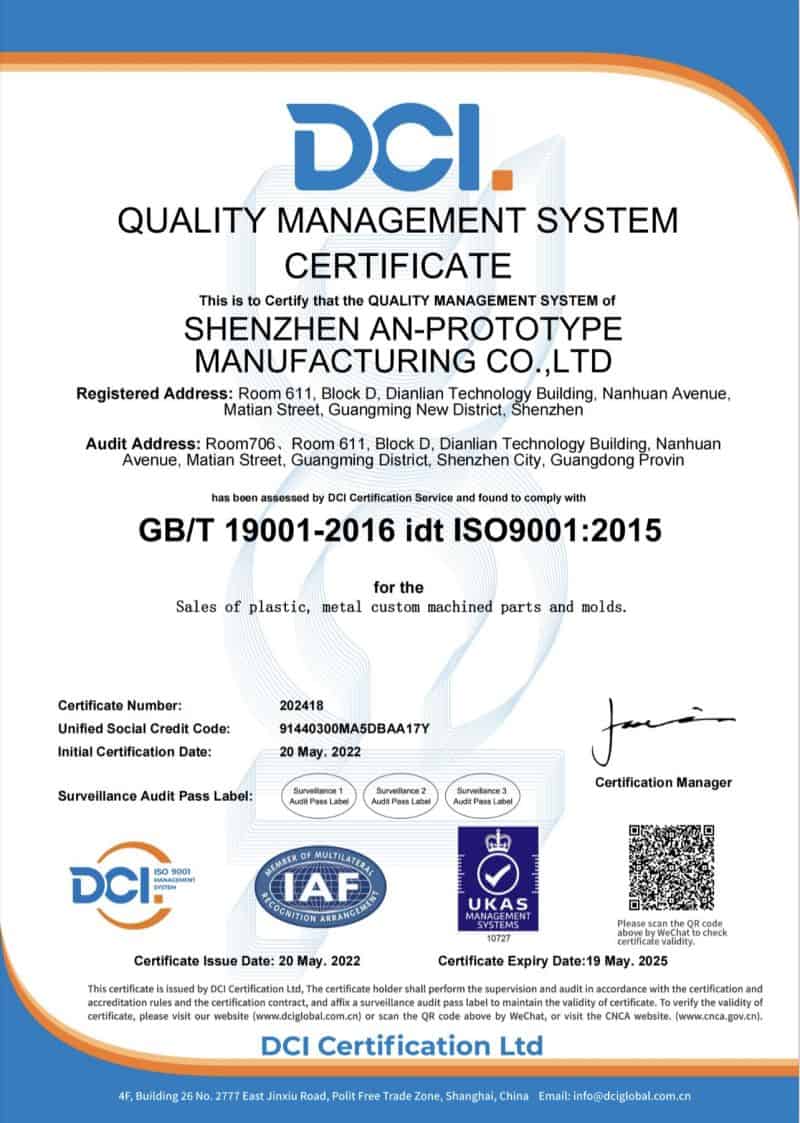
お客様からの評価
「私がAN-Prototypeと協力した経験は素晴らしいです。彼らのコミュニケーションは非常に優れており、Michinはいつも私の質問に答えることができます。私たちが受け取った完成品は予想通りの最高品質を持っています。本当に存在するのは、私がいつもMitchinから得ている良質なサービスです。彼はいつも私たちの満足を確保することに力を入れている。総合的には、信頼できるベンダーを探している人にAN-PrototypeとMichinを強くお勧めします。
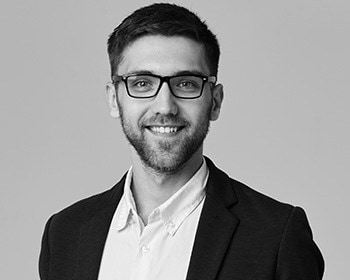
「複雑な5軸CNC加工部品であっても、AN-Prototypeからは非常に良い結果が得られました。過去2年間、AN-Prototypeと共に多くのプロジェクトを手掛けてきましたが、彼らは常に非常に優れた品質(彼からCNC加工サービスとアルマイト処理を薦めてもらったこともできます)、信頼性、非常に迅速で完璧なコミュニケーションを提供してくれました。DavideとVivianとの協力に感謝し、すでに多くのパートナーに推薦してくれました。

「私のAN-Prototypeに対する体験はとても特別です。最初から通信は正確で迅速であり、難しい設計に対しても、ソリューションを提供します。プロトタイプ制作の価格は競争力があります。最終製品のQCも非常に優れています。続けて加工部品を依頼します。
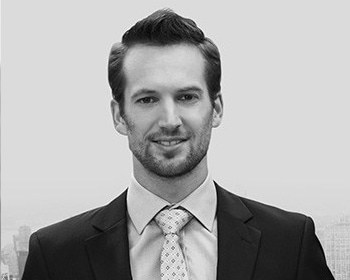